Verfahren zur Behandlung von duktilem Eisen mit Zufuhrdrahtmethode
Bei der eigentlichen Produktion werden das Stanzverfahren und das Zuführverfahren zur Herstellung von Sphäroguss verwendet und die Eigenschaften der beiden Prozesse analysiert. Durch den Vergleich ist die Gesamtleistung der mit der Zuführmethode hergestellten Gussteile stabiler als die der Stanzmethode; und der Fütterungsprozess ist sphäroidisiert. Um einige der Erfahrungen darin zu teilen.
1. Überblick
Wie wir alle wissen, ist die Achse ein wichtiger tragender Teil des Fahrzeugs und steht in direktem Zusammenhang mit der Sicherheit des Fahrzeugs. Das Achsgehäuse ist eine der Schlüsselkomponenten der Achse. Die Leistungsfähigkeit des Achsgehäusematerials bestimmt direkt die Tragfähigkeit des Fahrzeugs. Gegenwärtig werden die Achsgehäuse in der Schwerlastkraftwagenindustrie im Allgemeinen in zwei Kategorien unterteilt: gestanzte und geschweißte Achsgehäuse und gegossene Achsgehäuse, und gegossene Achsgehäuse können in Achsgehäuse aus Gussstahl und Achsgehäuse aus Gusseisen unterteilt werden.
Das gegossene Achsgehäuse nimmt aufgrund seines hohen Traggewichts und der geringen Produktionskosten seit jeher die Hauptposition des schweren Lkw-Achsgehäuses ein. Aufgrund der rauen Arbeitsumgebung des Achsgehäuses und der langfristigen Arbeit unter dynamischer Belastung stellt dies hohe Anforderungen an die Materialeigenschaften des Achsgehäuses. Während die Festigkeit gewährleistet ist, muss es auch eine höhere Plastizität und Zähigkeit erreichen, um sich an das Achsgehäuse anzupassen. Arbeitsmerkmale.
Wir wissen, dass der Sphäroidisierungsprozess bei Sphäroguss ein Schlüsselelement bei der Herstellung von Sphäroguss ist und dass die Qualität der Sphäroidisierungsbehandlung direkten Einfluss auf die Qualität des Sphärogusses hat. Zu Beginn verwendeten wir das Sphäroidisierungsverfahren nach der Rush-in-Methode. Obwohl diese Methode einfach und leicht durchzuführen ist, weist sie viele Nachteile auf, wie zum Beispiel: geringe Legierungsausbeute; großer Rauch und schlechte Arbeitsumgebung; Reaktion Die dabei erzeugte Schlackenmenge ist groß; Der Behandlungseffekt wird leicht durch äußere Faktoren beeinflusst, was zu Schwankungen in der Qualität der Gussteile und oft zu unqualifizierter Sphäroidisierung führt. Diese Qualitätsschwankungen beeinträchtigen die Leistung des Achsgehäuses und beeinträchtigen sogar die Sicherheit des Fahrzeugs.
Bei der Herstellung von Gusseisen wurde das Drahtzuführungsverfahren Sphäroidisierungsverfahren angewendet. Es begann in den 1980er Jahren im Ausland. Obwohl die inländische Produktion von Kugelgraphit erst spät mit der Anwendung dieser Technologie begann, wurde die Technologie im Land schnell populär gemacht und eingesetzt und ist nützlich für die Verbesserung der Produktion von Kugelgraphit. Der Stabilitätseffekt der Gusseisenqualität ist offensichtlich.
2. Sphäroidisierungsprozess des Vorschubdrahtes
Das Grundprinzip des Sphäroidisierungsprozesses mit Fadenzuführung besteht darin, eine bestimmte Zusammensetzung aus pulverförmigem Sphäroidisierungsmittel und Impfmittel durch die Stahlhaut zu wickeln und sie mit einer bestimmten Geschwindigkeit durch die Ausrüstung in das Sphäroidisierungsbehandlungspaket zu schicken, so dass die Sphäroidisierung am Boden erfolgt Das Paket wird explodieren. Um den Zweck der Sphäroidisierungs-Inokulationsbehandlung zu erreichen.
Derzeit verwenden wir das Sphäroidisierungsverfahren zur Drahtzuführung wie folgt: Passen Sie die chemische Zusammensetzung an die Prozessanforderungen an, erhitzen Sie es auf 1510 bis 1520 °C und lassen Sie es stehen. Die Abstichtemperatur beträgt 1480 bis 1500 °C, die Eisenleistung beträgt 2 t Die Temperatur der Sphäroidisierungsbehandlung beträgt 1420 bis 1450 °C. Die Gießtemperatur beträgt 1370 bis 1380 °C. Die Impfrate mit der Strömung beträgt 0.1 %.
Die Länge der Sphäroidisierungslinie beträgt 39–46 m, angepasst an den Schwefelgehalt der ursprünglichen Eisenschmelze. Je höher der Schwefelgehalt, desto länger muss die Sphäroidisierungslinie hinzugefügt werden und umgekehrt. Die Länge der Impfleitung beträgt 32m.
3. Der Sphäroidisierungsprozess beim Zuführen von Draht verbessert die Qualität der Gussteile
Nach mehr als einem Jahr Produktionszeit hat sich die Qualität unserer Achsgehäuse im Vergleich zu zuvor deutlich verbessert. Insbesondere die Stabilität der Zusammensetzung, Metallographie und mechanischen Eigenschaften wurden erheblich verbessert.
Vergleich der metallografischen Struktur Wählen Sie die gleiche Position des Gussstücks zum Polieren und beobachten Sie die metallografische Struktur. Das aufgenommene metallografische Bild ist in Abbildung 2 dargestellt. Im Vergleich zur Stanzmethode sind die Graphitkugeln des durch die Zuführmethode erzeugten Gussstücks größer und dünner und die Rundheit ist besser.
4. Vorteile des Sphäroidisierungsprozesses mit Zuführfaden
Laut unserem tatsächlichen Produktionsvergleich hat der Sphäroidisierungsprozess mit Fadenzuführung viele Vorteile gegenüber dem Sphäroidisierungsprozess der Stanzmethode.
- Verbesserung der Produktionsumgebung vor Ort. Wenn das Sphäroidisierungsmittel mit dem geschmolzenen Eisen reagiert, entstehen große Mengen Rauch und starkes Licht, was die Arbeitsumgebung vor Ort verschlechtert; Wenn die Drahtvorschubmethode zur Sphäroidisierung verwendet wird, verfügt die Verarbeitungsstation über eine Abdeckung zum Abdecken des Sphäroidisierungsbeutels, und die Abdeckung ist mit dem Staubentfernungssystem der Verarbeitungsstation verbunden, sodass der Rauch stattdessen vom Staubentfernungssystem verarbeitet wird direkt in der Werkstatt freigegeben zu werden.
- Die Menge der zugesetzten Legierung wird reduziert und die Produktionskosten werden gesenkt. Nach der Berechnung kann die Verarbeitung von 1 Tonne geschmolzenem Eisen mit der Zufuhrmethode etwa 78 Yuan an Rohstoffkosten einsparen als mit der Impulsmethode. Entsprechend der jährlichen Produktionskapazität von 10,000 Tonnen Achsgehäusen aus Sphäroguss in unserem Werk beträgt die jährliche Einsparung 780,000 Yuan und die Vorteile sind beträchtlich.
- Verwirklichen Sie die Arbeitsautomatisierung und reduzieren Sie die Arbeitsintensität der Arbeitnehmer. Wenn der Sphäroidisierungsprozess durchgeführt wird, sind die vorbereitenden Vorbereitungen der Arbeiter umständlich, einschließlich des Abwiegens des Sphäroidisierungsmittels und des Impfmittels, des Hinzufügens des Sphäroidisierungsmittels und des Impfmittels in den Beutel sowie der erforderlichen Stampf- und Abdeckvorgänge; Die Zugabemenge der Sphäroidisierungs- und Impfleitungen der Fadenzuführmethode wird automatisch über den Schaltschrank hinzugefügt, was viel Arbeit reduziert.
- Die Qualität der Sphäroidisierung ist stabil und der Sphäroidisierungseffekt ist besser. Laut Statistik liegt die Erfolgsquote der Sphäroidisierung seit der Verwendung des fadenführenden Sphäroidisierungsprozesses im Jahr 2013 bei über 99.5 %, während die Erfolgsquote des Sphäroidisierungsprozesses nur 95, % beträgt.
5. So wählen Sie die Prozessparameter für die Sphäroidisierung des Vorschubfadens richtig aus
In der tatsächlichen Produktion sind zur Überprüfung der korrekten Auswahl der Parameter des Drahtvorschubprozesses eine Reihe von Tests erforderlich. Vom Beginn der Testorganisation bis zur formellen Massenproduktion haben wir zahlreiche Prozessanpassungen vorgenommen. Im Folgenden teilen wir unsere Erfahrungen mit Kollegen.
Um die Prozessparameter der Vorschubfaden-Sphäroidisierung richtig auszuwählen, müssen Sie auf folgende Aspekte achten:
- (1) Die Wahl des Fülldrahts Einige Erfahrungen im Ausland raten von der Verwendung von Fülldraht mit hohem Mg-Gehalt ab. Der Mg-Gehalt ist zu hoch, die Sphäroidisierungsreaktion ist intensiv, das Mg verbrennt stark und die Schlackenmenge ist groß. Im Allgemeinen wird empfohlen, einen Mg-Gehalt von etwa 30 % zu wählen und einen Ba-haltigen Impffaden zu verwenden, der einen Rückgang der Impfung wirksam verhindern kann. Die Hauptparameter des von unserem Unternehmen verwendeten Fülldrahts sind: Die Dicke des äußeren Stahlmantels beträgt 0.4 mm und der Durchmesser des Kerndrahts beträgt 13 mm. Überprüfen Sie vor der Verwendung, ob das Aussehen des Fülldrahts rund und frei von Rissen, Pulveraustritt usw. ist. Bei der tatsächlichen Produktion ist eine Anpassung an die Behandlungstemperatur und die Höhe des geschmolzenen Eisens erforderlich. Im Allgemeinen gilt: Je höher die Behandlungstemperatur, desto höher ist die Höhe des geschmolzenen Eisens und desto schneller ist die Drahtvorschubgeschwindigkeit. Zusätzlich. Einige Materialien haben auch eine praktische und praktikable Methode zur Messung der optimalen Drahtvorschubgeschwindigkeit eingeführt: Messen Sie zunächst die Höhe des geschmolzenen Eisens im Verarbeitungsbeutel und führen Sie dann die Drahtmaschine manuell so vor, dass der Kerndraht gerade die Flüssigkeitsoberfläche berührt Leeren Sie den Zähler. Die manuelle Drahtvorschubmaschine führt den Drahtvorschub durch. Wenn Sie das „Boom“-Antwortgeräusch hören, überprüfen Sie sofort die Einzugslänge. Wenn diese Länge im Wesentlichen der Höhe der Eisenschmelze entspricht, sollte die Geschwindigkeit angemessen sein. Nach der Überprüfung haben wir die Vorschubgeschwindigkeit von 30 m/min gewählt.
- Auswahl der Fadenvorschubmenge Die geeignete Fadenvorschubmenge besteht darin, den Faden mit dem geringsten Kern zuzuführen, unter der Prämisse, den Sphäroidisierungseffekt sicherzustellen. Die Menge der Drahtzufuhr sollte entsprechend dem Verarbeitungsvolumen der Eisenschmelze, der Verarbeitungstemperatur und dem Schwefelgehalt der Eisenschmelze bestimmt werden. Gemäß unseren ursprünglichen Anforderungen an den Schwefelgehalt an geschmolzenem Eisen und an den Produktprozess, kombiniert mit experimenteller Überprüfung, beträgt die Länge der Sphäroidisierungslinie unter der Bedingung, dass der Restmagnesiumgehalt sichergestellt ist, 39–46 m und die Länge der Impflinie 32 m.
- Die Wahl der Verarbeitungstemperatur Die Verarbeitungstemperatur sollte unter der Prämisse, die Gießtemperatur sicherzustellen, so weit wie möglich reduziert werden. Je niedriger die Verarbeitungstemperatur, desto höher ist die Absorptionsrate von Magnesium und desto geringer ist der Fülldrahtverbrauch. Laut tatsächlichen Produktionstests beträgt die Zeit vom Beginn der Sphäroidisierungsbehandlung bis zum Beginn des Gießens 4 bis 5 Minuten, wobei der Temperaturabfall 40 bis 50 °C beträgt und die Reaktionszeit der Sphäroidisierung 80 bis 90 Sekunden beträgt. Da der Sphäroidisierungsprozess umgedreht werden muss, stellen wir die Verarbeitungstemperatur auf 1410 bis 1450 °C ein. Der obere Grenzwert gilt, wenn die Raumtemperatur unter 5 °C liegt, und der untere Grenzwert, wenn die Raumtemperatur über 25 °C liegt.
- Auswahl des Restmagnesiumgehalts in geschmolzenem Eisen nach der Behandlung. Der Restmagnesiumgehalt sollte entsprechend den Eigenschaften des Gussstücks selbst für einen bestimmten Magnesiumgehalt reserviert werden. Zuerst haben wir den Restmagnesiumgehalt auf 0.03 % bis 0.06 % kontrolliert, aber nach der tatsächlichen Produktionsüberprüfung ist es angemessener, den Restmagnesiumgehalt auf 0.05 % bis 0.06 % zu kontrollieren, da wir festgestellt haben, dass der Restmagnesiumgehalt geringer ist als 0.04 %, sein Graphit. Die Rundheit der Kugel ist etwas schlechter. Wenn er höher als 0.07 % ist, tritt leicht Zementit auf und die Schrumpfungsneigung der Eisenschmelze nimmt zu.
- Lösung des Problems des Drahtstaus während des Gebrauchs Das Phänomen des Drahtstaus tritt während des Fördervorgangs des Fülldrahts auf, was dazu führt, dass die gesamte Packung geschmolzenen Eisens verschrottet wird. Zu diesem Zweck haben wir die folgenden Maßnahmen ergriffen: Eine besteht darin, einen Stahlring über der Kerndrahtspule zu installieren, wie in Abbildung 5 dargestellt, der die Biegung des Kerndrahts verringern und dafür sorgen kann, dass er reibungslos in den Führungsmechanismus gelangt. Die zweite besteht darin, die beiden Spulen zu verbinden. Polieren Sie beim Schweißen nach dem Schweißen die größeren Unebenheiten weg, um zu verhindern, dass sich der Draht während des Fördervorgangs verklemmt. Drittens sind Biegungen mit einem Durchmesser von weniger als 1 m in der Förderleitung oder dem Weg des Fülldrahts zu vermeiden, um zu verhindern, dass der Fülldraht transportiert wird. Während des Prozesses kommt es zu Pulverlecks oder -staus
6 Fazit
- Der Sphäroidisierungsprozess mit der Vorschubdrahtmethode weist eine geringe Legierungszugabemenge und eine hohe Mg-Absorptionsrate auf und kann Rauch und starke Lichtverschmutzung in der Werkstatt wirksam reduzieren, was gute wirtschaftliche und ökologische Vorteile für Gießereiunternehmen mit sich bringt.
- Der Sphäroidisierungsprozess mit der Gewindezuführungsmethode kann die Ausfallrate der Sphäroidisierung wirksam reduzieren, die Qualität von Kugelgraphitguss verbessern, seine umfassenden mechanischen Eigenschaften verbessern und die Wettbewerbsfähigkeit des Unternehmens auf dem Markt steigern.
- Jede Gießerei sollte die geeigneten Prozessparameter für die Drahtkugelformung gemäß ihren eigenen Produktionsbedingungen und Produktprozessanforderungen auswählen, kombiniert mit der Produktionserfahrung der Kollegen.
Der Sphäroidisierungsprozess der Zuleitung kann die Stabilität der Qualität von Sphäroguss erheblich verbessern, die Produktionskosten senken, die Produktionsumgebung verbessern und die Arbeitsintensität der Arbeiter verringern. Dies ist der jüngste Entwicklungstrend des Sphäroidisierungsprozesses.
Bitte bewahren Sie die Quelle und Adresse dieses Artikels für den Nachdruck auf: Feeding Wire Method Verfahren zur Behandlung von duktilem Eisen
Mingh Druckgussunternehmen sind der Herstellung und Bereitstellung von hochwertigen und leistungsstarken Gussteilen gewidmet (das Angebot an Metalldruckgussteilen umfasst hauptsächlich) Dünnwandiger Druckguss,Heißkammerdruckguss,Kaltkammerdruckguss), Runder Service (Druckguss-Service,CNC-Bearbeitung,Formenbau,Oberflächenbehandlung). Alle kundenspezifischen Aluminium-Druckguss-, Magnesium- oder Zamak/Zink-Druckguss- und andere Gussanforderungen können uns gerne kontaktieren.
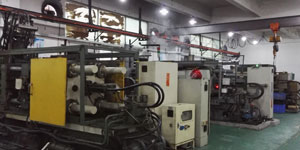
Unter der Kontrolle von ISO9001 und TS 16949 werden alle Prozesse durch Hunderte von fortschrittlichen Druckgussmaschinen, 5-Achsen-Maschinen und anderen Einrichtungen durchgeführt, von Blasgeräten bis hin zu Ultraschall-Waschmaschinen.Minghe verfügt nicht nur über fortschrittliche Ausrüstung, sondern auch über professionelle Team aus erfahrenen Ingenieuren, Bedienern und Inspektoren, um das Design des Kunden zu verwirklichen.
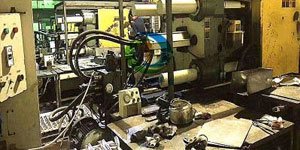
Auftragsfertigung von Druckgussteilen. Zu den Fähigkeiten gehören Kaltkammer-Aluminium-Druckgussteile von 0.15 lbs. bis 6 lbs., Schnellwechseleinrichtung und Bearbeitung. Mehrwertdienste umfassen Polieren, Vibrieren, Entgraten, Kugelstrahlen, Lackieren, Plattieren, Beschichten, Montage und Werkzeugbau. Zu den Materialien, mit denen gearbeitet wird, gehören Legierungen wie 360, 380, 383 und 413.
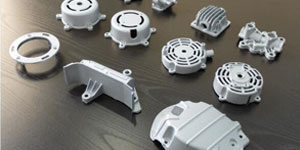
Unterstützung bei der Konstruktion von Zinkdruckguss / gleichzeitige Engineering-Dienstleistungen. Auftragsfertigung von Präzisions-Zink-Druckgussteilen. Es können Miniaturgussteile, Hochdruck-Kokillengussteile, Mehrschieber-Kokillengussteile, konventionelle Kokillengussteile, Einzel- und Einzeldruckgussteile sowie hohlraumdichte Gussteile hergestellt werden. Gussteile können in Längen und Breiten bis zu 24 Zoll in +/-0.0005 Zoll Toleranz hergestellt werden.
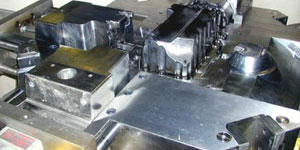
ISO 9001: 2015 zertifizierter Hersteller von Magnesium-Druckguss. Zu den Fähigkeiten gehören Hochdruck-Magnesium-Druckguss bis zu 200 Tonnen Heißkammer und 3000 Tonnen Kaltkammer, Werkzeugdesign, Polieren, Formen, Bearbeitung, Pulver- und Flüssiglackierung, vollständige Qualitätssicherung mit KMG-Fähigkeiten , Montage, Verpackung & Lieferung.
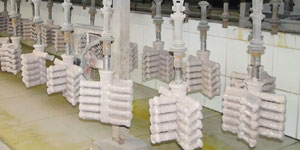
ITAF16949-zertifiziert. Zusätzlicher Casting-Service inklusive Feinguss,Sandguss,Schwerkraftguss, Verlorener Schaumguss,Schleuderguss,Vakuumgießen,Dauerguss,.Zu den Fähigkeiten gehören EDI, technische Unterstützung, Volumenmodellierung und Sekundärverarbeitung.
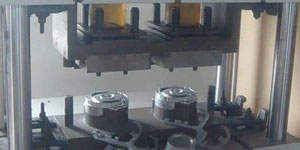
Gussindustrie Teile-Fallstudien für: Autos, Fahrräder, Flugzeuge, Musikinstrumente, Wasserfahrzeuge, optische Geräte, Sensoren, Modelle, elektronische Geräte, Gehäuse, Uhren, Maschinen, Motoren, Möbel, Schmuck, Vorrichtungen, Telekommunikation, Beleuchtung, medizinische Geräte, Fotogeräte, Roboter, Skulpturen, Tongeräte, Sportgeräte, Werkzeuge, Spielzeug und mehr.
Was können wir Ihnen als nächstes helfen?
∇ Zur Startseite gehen für Druckguss China
→Gussteile- Finden Sie heraus, was wir getan haben.
→Bewertete Tipps zu Druckgussdienste
By Minghe Druckgusshersteller |Kategorien: Hilfreiche Artikel |Werkstoff Stichworte: Aluminiumguss, Zinkguss, Magnesiumguss, Titanguss, Edelstahlguss, Messingguss,Bronzeguss,Casting-Video,Unternehmensgeschichte,Aluminiumdruckguss |Kommentare deaktiviert