Zerspanende Bearbeitung von pulvermetallurgischen (P/M) Teilen
Der Einsatz von Pulvermetallurgie (P/M)-Prozessen zur Herstellung von Teilen für Kraftfahrzeugantriebe nimmt weiter zu. Teile, die im P / M-Verfahren hergestellt werden, haben viele wichtige und einzigartige Vorteile. Die absichtlich in diesen Teilen verbleibende poröse Reststruktur ist gut für die Selbstschmierung und Schalldämmung. Komplexe Legierungen, die im traditionellen Gießverfahren nur schwer oder gar nicht herstellbar sind, können mit der P/M-Technologie hergestellt werden. Teile, die mit dieser Technologie hergestellt werden, haben normalerweise keine oder nur eine geringe Verarbeitungskapazität, was sie billiger macht und weniger Materialverschwendung macht. Leider sind P / M-Teile hinter der Attraktivität dieser Funktionen schwer zu bearbeiten.
Obwohl eine der ursprünglichen Absichten der P/M-Industrie darin besteht, jegliche Verarbeitung zu eliminieren, wurde dieses Ziel noch nicht erreicht. Die meisten Teile können nur "nahe der endgültigen Form" sein und müssen noch nachbearbeitet werden.
Im Vergleich zu Guss- und Schmiedeteilen ist jedoch eine geringe Materialmenge, die von P / M-Teilen entfernt werden muss, ein typisches verschleißfestes Material.
Die poröse Struktur ist eine der Eigenschaften, die P / M-Teile zu einem breiten Anwendungsspektrum machen, aber die Standzeit wird auch durch die poröse Struktur beeinträchtigt. Die poröse Struktur kann Öl und Geräusche speichern, führt aber auch zu mikrointermittierenden Schnitten. Beim Hin- und Herbewegen von der Bohrung zu den festen Partikeln wird die Werkzeugspitze ständig geschlagen, was zu sehr kleinen Ermüdungsbruchverformungen und einem feinen Kantenkollaps entlang der Schneide führen kann. Erschwerend kommt hinzu, dass die Partikel meist sehr hart sind. Auch wenn die Makrohärte des gemessenen Materials zwischen 20 und 35 Grad liegt, beträgt die Partikelgröße des Bauteils bis zu 60 Grad. Diese harten Partikel verursachen einen starken und schnellen Kantenverschleiß. Viele p/M-Teile sind wärmebehandelbar und die Härte und Festigkeit des Materials sind nach der Wärmebehandlung höher. Schließlich enthält die Oberfläche des Materials aufgrund der Sinter- und Wärmebehandlungstechnologie und der verwendeten Gase harte und verschleißfeste Oxide und / oder Karbide.
Leistung von P/M-Teilen
Die meisten Eigenschaften von P/M-Teilen, einschließlich der Bearbeitbarkeit, hängen nicht nur mit der chemischen Zusammensetzung der Legierung, sondern auch mit dem Porositätsgrad der porösen Struktur zusammen. Die Porosität vieler Bauteile beträgt bis zu 15 % ~ 20 %. Die Porosität von Teilen, die als Filtervorrichtungen verwendet werden, kann bis zu 50 % betragen. Am anderen Ende der Reihe beträgt die Porosität von Schmiede- oder Hüftteilen nur 1% oder weniger. Diese Materialien gewinnen insbesondere in Automobil- und Flugzeuganwendungen an Bedeutung, da sie höhere Festigkeiten erreichen können.
Die Zugfestigkeit, Zähigkeit und Duktilität von P/M-Legierungen nehmen mit zunehmender Dichte zu, und auch die Bearbeitbarkeit kann verbessert werden, da die Porosität für die Werkzeugspitze schädlich ist.
Die Erhöhung des Porositätsgrades kann die Schalldämmleistung von Teilen verbessern. Die Dämpfungsschwingung bei Normteilen wird bei P/M-Teilen deutlich reduziert, was bei Werkzeugmaschinen, Klimablasrohren und Druckluftwerkzeugen sehr wichtig ist. Auch bei selbstschmierenden Getrieben ist eine hohe Porosität erforderlich.
Schwierigkeiten bei der Bearbeitung
Obwohl eines der Ziele der kontinuierlichen Entwicklung der P / M-Industrie darin besteht, die maschinelle Bearbeitung zu eliminieren, und eine der Hauptattraktionen des P / M-Prozesses darin besteht, dass nur ein geringer Bearbeitungsaufwand erforderlich ist, müssen viele Teile noch nachbehandelt werden, um sie zu erhalten höhere Genauigkeit oder bessere Oberflächengüte. Leider ist die Bearbeitung dieser Teile äußerst schwierig. Die meisten der auftretenden Probleme werden durch Porosität verursacht. Porosität führt zu Mikroermüdung der Schneide. Die Schneide schneidet ständig ein und aus. Es passiert zwischen Partikeln und Löchern. Wiederholte kleine Schläge führen zu kleinen Rissen an der Schneide.
Diese Ermüdungsrisse wachsen, bis die Schneidkante kollabiert. Diese Art von Mikroabsplitterung ist in der Regel sehr klein und weist in der Regel normalen abrasiven Verschleiß auf.
Porosität verringert auch die Wärmeleitfähigkeit von P/M-Teilen, was zu einer hohen Temperatur an der Schneidkante und zu Kraterverschleiß und Verformung führt. Die intern verbundene poröse Struktur stellt einen Weg für die Ableitung von Schneidflüssigkeit aus dem Schneidbereich bereit. Dies kann insbesondere beim Bohren zu Heißrissen oder Verformungen führen.
Die durch die innere poröse Struktur verursachte Oberflächenvergrößerung führt auch während der Wärmebehandlung zu Oxidation und/oder Karbonisierung. Wie bereits erwähnt, sind diese Oxide und Karbide hart und verschleißfest.
Die poröse Struktur führt auch zum Versagen der Härtemessung des Teils, was äußerst wichtig ist. Wenn die Makrohärte eines P/M-Teils absichtlich gemessen wird, beinhaltet sie den Faktor der Lochhärte. Die poröse Struktur führt zum Zusammenbruch der Struktur und vermittelt den falschen Eindruck von relativ weichen Teilen. Die Partikel sind viel härter. Wie oben beschrieben, ist der Unterschied dramatisch.
Nachteilig ist auch das Vorhandensein von Einschlüssen in PM-Teilen. Während der Bearbeitung werden diese Partikel von der Oberfläche hochgezogen und es bilden sich Kratzer oder Kratzer auf der Oberfläche des Teils, wenn es vor dem Werkzeug gerieben wird. Diese Einschlüsse sind normalerweise groß und hinterlassen sichtbare Löcher auf der Oberfläche des Teils.
Der Unterschied im Kohlenstoffgehalt führt zu einer uneinheitlichen Bearbeitbarkeit. Zum Beispiel reicht der Kohlenstoffgehalt der fc0208-Legierung von 0.6% bis 0.9%. Eine Materialcharge mit 0.9% Kohlenstoffgehalt ist relativ hart, was zu einer geringen Standzeit führt. Die andere Materialcharge mit 0.6% Kohlenstoffgehalt hat eine ausgezeichnete Standzeit. Beide Legierungen liegen im zulässigen Bereich.
Das Problem der Endbearbeitung hängt mit der Art des Schneidens zusammen, das am P / M-Teil auftritt. Da das Teil der endgültigen Form nahe kommt, ist die Schnitttiefe in der Regel sehr gering. Dies erfordert eine freie Schneide. Spanaufbau an der Schneide führt oft zu Mikroausbrüchen.
Verarbeitungstechnologie
Um diese Probleme zu überwinden, werden verschiedene (in der Branche einzigartige) Technologien eingesetzt. Die poröse Oberflächenstruktur wird oft durch Infiltration versiegelt. In der Regel ist zusätzlicher Freischnitt erforderlich. In letzter Zeit wurden verbesserte Pulverherstellungsverfahren verwendet, die darauf ausgelegt sind, die Pulverreinheit zu erhöhen und Oxide und Karbide während der Wärmebehandlung zu reduzieren.
Die poröse Struktur mit geschlossener Oberfläche wird durch Metall- (üblicherweise Kupfer) oder Polymerinfiltration erreicht. Es wurde spekuliert, dass Infiltration als Schmiermittel wirkt. Die meisten experimentellen Daten zeigen, dass der eigentliche Vorteil darin liegt, die poröse Oberflächenstruktur zu schließen und so die Mikroermüdung der Schneidkante zu verhindern. Die Reduzierung des Ratterns verbessert die Standzeit und die Oberflächengüte. Der dramatischste Einsatz der Infiltration zeigt eine 200% längere Standzeit, wenn die poröse Struktur geschlossen ist.
Additive wie MNS, s, MoS2, MgSiO3 und BN erhöhen bekanntermaßen die Standzeit. Diese Zusätze verbessern die Zerspanbarkeit, indem sie die Späneabscheidung vom Werkstück erleichtern, Späne brechen, Spänebildung verhindern und die Schneidkante schmieren. Eine Erhöhung der Additivmenge kann die Bearbeitbarkeit verbessern, jedoch die Festigkeit und Zähigkeit verringern.
Die Pulverzerstäubungstechnologie zur Kontrolle von Sinter- und Wärmebehandlungsofengasen ermöglicht die Herstellung sauberer Pulver und Teile, wodurch das Auftreten von Einschlüssen und Oberflächenoxidkarbiden minimiert wird.
Werkzeugmaterial
Die am häufigsten verwendeten Werkzeuge in der P / M-Industrie sind Materialien, die verschleißfest, kantenrissbeständig und bei guter Oberflächengüte spanfrei sind. Diese Eigenschaften sind für jeden Bearbeitungsvorgang nützlich, insbesondere für P / M-Teile. Die in dieser Kategorie enthaltenen Werkzeugmaterialien sind Werkzeuge aus kubischem Bornitrid (CBN), unbeschichtete und beschichtete Cermets und verbesserte beschichtete gesinterte Hartmetalle.
CBN-Werkzeuge überzeugen durch ihre hohe Härte und Verschleißfestigkeit. Dieses Werkzeug wird seit vielen Jahren bei der Bearbeitung von Stahl und Gusseisen ab einer Rockwellhärte von 45 eingesetzt. Aufgrund der einzigartigen Eigenschaften der P / M-Legierung und des signifikanten Unterschieds zwischen Mikrohärte und Makrohärte können CBN-Werkzeuge jedoch für P / M-Teile mit einer Rockwell-Härte von 25 verwendet werden. Der Schlüsselparameter ist die Härte der Partikel. Wenn die Härte der Partikel Rockwell 50 Grad überschreitet, sind CBN-Werkzeuge unabhängig vom Makrohärtewert verfügbar. Die offensichtliche Einschränkung dieser Werkzeuge ist ihre mangelnde Zähigkeit. Bei intermittierendem Schnitt oder hoher Porosität ist eine Kantenverstärkung einschließlich negativer Fasen und starkes Honen erforderlich. Einfaches leichtes Schneiden ist mit geschliffener Schneide möglich.
Es gibt verschiedene Materialien von CBN, die wirksam sind. Das Material mit der besten Zähigkeit besteht hauptsächlich aus dem gesamten CBN. Sie haben eine ausgezeichnete Zähigkeit, so dass sie zum Schruppen verwendet werden können. Ihre Grenzen hängen normalerweise mit der Oberflächenbeschaffenheit zusammen. Sie wird maßgeblich von den einzelnen CBN-Partikeln bestimmt, aus denen das Werkzeug besteht. Wenn die Partikel von der Schneide abfallen, wirken sie auf die Oberfläche des Werkstückmaterials. Es ist jedoch nicht so schwerwiegend, dass das Feinpartikelwerkzeug von einem Partikel abfällt.
Das üblicherweise verwendete CBN-Material hat einen hohen CBN-Gehalt und eine mittlere Partikelgröße. Die CBN-Schlichtklinge ist feinkörnig und der CBN-Gehalt ist gering. Sie sind am effektivsten, wenn leichte Zerspanung und Oberflächengüte erforderlich sind oder die zu bearbeitende Legierung besonders hart ist.
Bei vielen Zerspanungsanwendungen ist die Standzeit unabhängig von der Materialart. Mit anderen Worten, jedes CBN-Material kann ähnliche Standzeiten erreichen. In diesen Fällen richtet sich die Materialauswahl hauptsächlich nach den niedrigsten Kosten jeder Schneide. Eine runde Klinge hat eine ganze CBN-Oberseite und kann vier oder mehr Schneidkanten bieten, was billiger ist als vier eingelegte CBN-Klingen.
Wenn die Härte von P / M-Teilen niedriger als Rockwell 35 Grad ist und die Härte der Partikel innerhalb des Bereichs liegt, ist Cermet normalerweise eine der Optionen. Cermets sind sehr hart, können Spanbildung effektiv verhindern und halten hohen Geschwindigkeiten stand. Da Cermets seit jeher für die Hochgeschwindigkeits- und Schlichtbearbeitung von Stahl und Edelstahl verwendet wurden, weisen sie außerdem in der Regel ideale geometrische Nuten auf, die sich für nahe an umgeformte Teile eignen.
Heutige Cermets sind in der Metallurgie kompliziert und enthalten bis zu 11 Legierungselemente. Sie werden normalerweise aus TiCN-Partikeln und Ni-Mo-Klebstoff gesintert. TiCN bietet Härte, Spanbildungsbeständigkeit und chemische Stabilität, die für den erfolgreichen Einsatz von Cermets wichtig sind. Zudem weisen diese Werkzeuge meist einen hohen Klebstoffanteil auf, wodurch sie eine gute Zähigkeit aufweisen. Mit einem Wort, sie haben alle Eigenschaften, um P / M-Legierungen effektiv zu verarbeiten. Mehrere Arten von Cermets sind wirksam, ebenso wie gesintertes Hartmetall aus Wolframkarbid. Je höher der Bindemittelgehalt, desto besser die Zähigkeit.
Eine bekannte relativ neue Entwicklung ist, dass die chemische Gasphasenabscheidung bei mittlerer Temperatur (mtcvd) auch einen Vorteil für die P/M-Industrie bietet. Mtcvd behält die gesamte Verschleißfestigkeit und Kraterverschleißfestigkeit der traditionellen chemischen Gasphasenabscheidung (CVD) bei, verbessert aber auch objektiv die Zähigkeit. Die Zunahme der Zähigkeit kommt hauptsächlich von der Abnahme von Rissen. Die Beschichtung wird bei hoher Temperatur abgeschieden und dann im Ofen abgekühlt. Die Beschichtung enthält Risse, wenn das Werkzeug aufgrund der inkonsistenten Wärmeausdehnung Raumtemperatur erreicht. Ähnlich wie Kratzer auf Flachglas verringern diese Risse die Festigkeit der Schneide. Die niedrigere Abscheidungstemperatur von mtcvd führt zu einer geringeren Rissfrequenz und einer besseren Zähigkeit der Schneidkante.
Wenn das Substrat der CVD-Beschichtung und der mtcvd-Beschichtung die gleichen Eigenschaften und Kantenbearbeitung aufweisen, kann der Unterschied ihrer Zähigkeit nachgewiesen werden. Bei Anwendungen, bei denen Kantenzähigkeit erforderlich ist, ist die Leistung der mtcvd-Beschichtung besser als die der CVD-Beschichtung. Durch Analyse ist bei der Bearbeitung von P/M-Teilen mit poröser Struktur die Kantenzähigkeit wichtig. Mtcvd-Beschichtung ist besser als CVD-Beschichtung.
Die PVD-Beschichtung (Physical Vapor Deposition) ist dünner und weniger verschleißfest als mtcvd- oder CVD-Beschichtung. Die PVD-Beschichtung kann jedoch erheblichen Auswirkungen bei der Anwendung standhalten. Die PVD-Beschichtung ist effektiv, wenn das Schneiden abrasiver Verschleiß ist, CBN und Cermets zu spröde sind und eine hervorragende Oberflächengüte erfordern.
Beispielsweise kann die Schneidkante aus C-2 Hartmetall fc0205 mit einer Liniengeschwindigkeit von 180 m/min und einem Vorschub von 0.15 mm/Umdrehung bearbeitet werden. Nach der Bearbeitung von 20 Teilen kann die Spanbildung zu einem Mikrokollaps führen. Wenn eine PVD-Titannitrid-(TIN)-Beschichtung verwendet wird, wird die Spanbildung gehemmt und die Werkzeugstandzeit verlängert. Wenn für diesen Test eine Zinnbeschichtung verwendet wird, wird erwartet, dass die abrasiven Verschleißeigenschaften von P / M-Teilen mit TiCN-Beschichtung effektiver sind. TiCN hat fast die gleiche Spanbildungsbeständigkeit wie Zinn, ist jedoch härter und verschleißfester als Zinn.
Die poröse Struktur ist wichtig und beeinflusst die Bearbeitbarkeit der fc0208-Legierung. Wenn sich die poröse Struktur und die Eigenschaften ändern, bieten unterschiedliche Werkzeugmaterialien entsprechende Vorteile. Bei geringer Dichte (6.4 g/cm3) ist die Makrohärte gering. In diesem Fall bietet mtcvd-beschichtetes Hartmetall die beste Standzeit. Die Mikroermüdung der Schneidkante ist sehr wichtig, und die Kantenzähigkeit ist sehr wichtig. In diesem Fall bietet eine Cermet-Klinge mit guter Zähigkeit die maximale Standzeit.
Bei der Herstellung derselben Legierung mit einer Dichte von 6.8 g/cm3 wird abrasiver Verschleiß wichtiger als Kantenrisse. In diesem Fall bietet die mtcvd-Beschichtung die beste Standzeit. Zur Prüfung der beiden Arten extrem harter Teile wird PVD-beschichtetes Hartmetall verwendet, das bei Berührung mit der Schneide bricht.
Wenn die Geschwindigkeit zunimmt (die lineare Geschwindigkeit beträgt mehr als 300 Meter pro Minute), führen Cermets und sogar beschichtete Cermets zu Kraterverschleiß. Beschichtetes Hartmetall ist besser geeignet, insbesondere wenn die Schneidkantenzähigkeit von beschichtetem Hartmetall gut ist. Die Mtcvd-Beschichtung ist besonders effektiv für Hartmetall mit kobaltreichen Bereichen.
Cermets werden am häufigsten beim Drehen und Bohren verwendet. PVD-beschichtete Hartmetalle sind ideal für die Gewindebearbeitung, da niedrigere Drehzahlen und mehr Aufmerksamkeit beim Aufbau erwartet werden können.
Bitte bewahren Sie die Quelle und Adresse dieses Artikels für den Nachdruck auf:Zerspanende Bearbeitung von pulvermetallurgischen (P/M) Teilen
Minghe Casting Company widmet sich der Herstellung und Bereitstellung von hochwertigen und leistungsstarken Gussteilen (die Palette der Metalldruckgussteile umfasst hauptsächlich mainly Dünnwandiger Druckguss,Heißkammerdruckguss,Kaltkammerdruckguss), Runder Service (Druckguss-Service,CNC-Bearbeitung,Formenbau,Oberflächenbehandlung). Alle kundenspezifischen Aluminium-Druckguss-, Magnesium- oder Zamak/Zink-Druckguss- und andere Gussanforderungen können uns gerne kontaktieren.
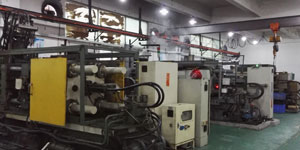
Unter der Kontrolle von ISO9001 und TS 16949 werden alle Prozesse durch Hunderte von fortschrittlichen Druckgussmaschinen, 5-Achsen-Maschinen und anderen Einrichtungen durchgeführt, von Blasgeräten bis hin zu Ultraschall-Waschmaschinen.Minghe verfügt nicht nur über fortschrittliche Ausrüstung, sondern auch über professionelle Team aus erfahrenen Ingenieuren, Bedienern und Inspektoren, um das Design des Kunden zu verwirklichen.
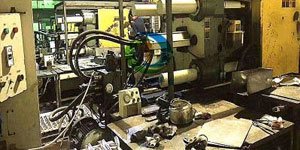
Auftragsfertigung von Druckgussteilen. Zu den Fähigkeiten gehören Kaltkammer-Aluminium-Druckgussteile von 0.15 lbs. bis 6 lbs., Schnellwechseleinrichtung und Bearbeitung. Mehrwertdienste umfassen Polieren, Vibrieren, Entgraten, Kugelstrahlen, Lackieren, Plattieren, Beschichten, Montage und Werkzeugbau. Zu den Materialien, mit denen gearbeitet wird, gehören Legierungen wie 360, 380, 383 und 413.
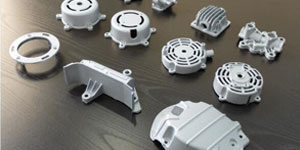
Unterstützung bei der Konstruktion von Zinkdruckguss / gleichzeitige Engineering-Dienstleistungen. Auftragsfertigung von Präzisions-Zink-Druckgussteilen. Es können Miniaturgussteile, Hochdruck-Kokillengussteile, Mehrschieber-Kokillengussteile, konventionelle Kokillengussteile, Einzel- und Einzeldruckgussteile sowie hohlraumdichte Gussteile hergestellt werden. Gussteile können in Längen und Breiten bis zu 24 Zoll in +/-0.0005 Zoll Toleranz hergestellt werden.
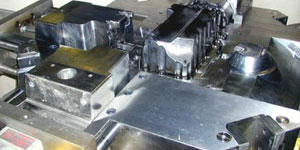
ISO 9001: 2015 zertifizierter Hersteller von Magnesium-Druckguss. Zu den Fähigkeiten gehören Hochdruck-Magnesium-Druckguss bis zu 200 Tonnen Heißkammer und 3000 Tonnen Kaltkammer, Werkzeugdesign, Polieren, Formen, Bearbeitung, Pulver- und Flüssiglackierung, vollständige Qualitätssicherung mit KMG-Fähigkeiten , Montage, Verpackung & Lieferung.
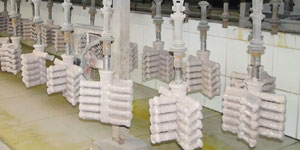
ITAF16949-zertifiziert. Zusätzlicher Casting-Service inklusive Feinguss,Sandguss,Schwerkraftguss, Verlorener Schaumguss,Schleuderguss,Vakuumgießen,Dauerguss,.Zu den Fähigkeiten gehören EDI, technische Unterstützung, Volumenmodellierung und Sekundärverarbeitung.
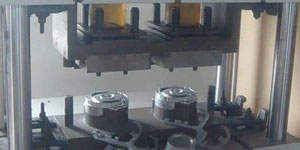
Gussindustrie Teile-Fallstudien für: Autos, Fahrräder, Flugzeuge, Musikinstrumente, Wasserfahrzeuge, optische Geräte, Sensoren, Modelle, elektronische Geräte, Gehäuse, Uhren, Maschinen, Motoren, Möbel, Schmuck, Vorrichtungen, Telekommunikation, Beleuchtung, medizinische Geräte, Fotogeräte, Roboter, Skulpturen, Tongeräte, Sportgeräte, Werkzeuge, Spielzeug und mehr.
Was können wir Ihnen als nächstes helfen?
∇ Zur Startseite gehen für Druckguss China
→Gussteile- Finden Sie heraus, was wir getan haben.
→Bewertete Tipps zu Druckgussdienste
By Minghe Druckgusshersteller |Kategorien: Hilfreiche Artikel |Werkstoff Stichworte: Aluminiumguss, Zinkguss, Magnesiumguss, Titanguss, Edelstahlguss, Messingguss,Bronzeguss,Casting-Video,Unternehmensgeschichte,Aluminiumdruckguss |Kommentare deaktiviert