Das Design und die Anwendung von Heißkanal für Zinkdruckguss
Verlust des Gussläufers
Jeder, der sich mit Druckguss auskennt, weiß, dass der Anguss oder das verbleibende Material Teil des Gussteils ist. Obwohl es keinen Gewinnwert gibt, kann dieser im Produktionsprozess nicht vermieden werden. Dieser Kostenanteil wird in der Regel nur als festes Verhältnis der Gussstückkosten berechnet. Gleichzeitig ist angesichts der Recyclingfähigkeit von Zinklegierungen die häufigste lokale Behandlungsmethode das Zurückwerfen in den Maschinenofen zum Umschmelzen in Echtzeit. Aufgrund der Notwendigkeit, Qualitätsprobleme zu kontrollieren, wird die Verwendung zentraler Schmelzöfen zur Wiederverwertung von Eingusskanälen oder Abfallprodukten von der Industrie nach und nach akzeptiert (Abbildung 1). Was die Schlacke betrifft, können größere Druckgussbetriebe diese selbst recyceln und die verbleibenden Materialien im Allgemeinen an die Rohstofflieferanten für neue Materialien zurückverkaufen. Der lokale Recyclingpreis für Zinkmaterialien beträgt in der Regel 50 bis 70 % des Neumaterialpreises. Ohne gute Umgebungsbedingungen kann der Umgang mit Schlacke leicht zu Luftverschmutzung führen.
Nehmen Sie als Beispiel eine 160 Tonnen schwere Warmkammer-Druckgussmaschine. Jedes Mal, wenn mindestens 150 Gramm Angusskanäle (ohne Überlaufbrunnen) produziert werden, beträgt der Produktionszyklus unter der Annahme von drei Schichten 20 Sekunden, die Maschinenauslastung 80 % und die Jahresproduktion 190 Tonnen. Ein weiteres Beispiel: Bei der Verwendung einer 80-Tonnen-Maschine zur Herstellung von jeweils 100 Gramm Läufern wird die gleiche Annahme getroffen, aber der Produktionszyklus wird auf 12 Sekunden geändert, und die jährliche Produktion von Läufern übersteigt 210 Tonnen.
Es ist ersichtlich, dass das Läuferdesign einen Einfluss auf die Kosten hat.
Verschiedene Recyclingmethoden
Unter den Recyclingmethoden ist das direkte Zurückwerfen des Angusskanals in den Ofen die einfachste und kostensparendste Methode. Der gerade durch Reflow-Schmelzen erzeugte Strömungskanal muss nicht vorgewärmt werden und der Lagerraum wird reduziert, aber es ist schwierig, die Qualität des geschmolzenen Materials zu kontrollieren, einschließlich mehr Schlacke, die Ofentemperatur ist schwer zu kontrollieren und die Legierung Zusammensetzung kann nicht bekannt sein; Noch wichtiger ist, dass es auf die handwerklichen Fähigkeiten des Bedienpersonals angewiesen ist, wie z. B. den Anteil neuer Materialien und die Beobachtung der Veränderungen im Kesselwasser, während das Personal Überlaufbrunnen und Blitze in den Ofen einbaut, was nicht nur die Situation verschlimmert, sondern diese Methode auch direkt Durch das Schmelzen wird der Abfall auch verborgen. Die hohe Fehlerquote, die Instabilität des Formendesigns und der Druckgussparameter haben die Manager daran gehindert, wirksame Verbesserungen vorzunehmen. Dieses Verfahren eignet sich nicht für die Herstellung von Gussteilen mit hohen Anforderungen an die Oberflächenqualität und es ist schwierig, die Kosten für Angussverluste genau zu berechnen.
Zentrale Ofenrückgewinnungsdüsen und fehlerhafte Produkte sind in Druckgussanlagen mit großer Produktion beliebt geworden. Die Vorteile liegen auf der Hand: Durch die zentrale Verarbeitung recycelter Materialien kann die Ofeneffizienz verbessert und die Legierungsqualität kontrolliert werden. Wenn die Metallschmelze direkt aus dem Zentralofen in den Ofen geleitet wird, kann die Materialtemperatur der Druckgussmaschine stabil gehalten werden und es entsteht weniger Schlacke. Bei Ausstattung mit einer automatischen Zufuhrsteuerung kann die Änderung des Flüssigkeitsstands minimiert werden. Derzeit beliebte zentrale Schmelzöfen sind in mehrere Kategorien unterteilt: Gusseisen-Tiegelöfen mit größerer Kapazität, Edelstahl-Tiegelöfen und kontinuierlich schmelzende Öfen ohne Tiegel. Der Transport von flüssigem Zink ist ebenfalls in mehrere Kategorien unterteilt: Es gibt den Transport von flüssigem Material vom Laufkrantyp, den Transport von Warmhalteöfen (mit Zuführvorrichtung) vom Bodenwagentyp (gleislos oder auf Raupen) und den Schwerkrafttransport vom Typ Haltetrog, der den Ofen und die Zentrale verbindet Ofen angeschlossen. Der Nachteil besteht darin, dass die Investition relativ groß ist, sie nur für eine einzige Legierung geeignet ist (kleiner Tiegelofen wird hier nicht behandelt) und die Werkstatt eine große Fläche einnimmt, sodass kleine Druckgussanlagen (weniger als fünf Maschinen) nicht geeignet sind geeignet, und die alten Werkstätten sind schwer umzuwandeln und zusammenzuarbeiten. Deshalb erfolgt in der Regel erst beim Bau einer neuen Anlage eine Neuplanung. Die Verwendung eines kleinen Tiegelofens zum Umschmelzen des Angussmaterials wird aufgrund fehlender Skaleneffekte mehr kosten als der Zentralofen und wird daher nicht als Referenz für die Berechnung verwendet.
Berechnung der Schmelzkosten
Verwenden Sie einfach den zentralen Schmelzofen, um die Schmelzkosten des Angusskanals als Referenz zu berechnen. Nehmen Sie als Beispiel ein Unternehmen mit fünf 80-Tonnen- oder 160-Tonnen-Druckgussmaschinen. Unter der Annahme, dass die Investition in die Ausrüstung 500,000 beträgt, wird sie in zehn Jahre aufgeteilt. Jedes Jahr werden etwa 1,000 Tonnen Läuferrecyclingmaterialien verarbeitet (die tatsächliche Situation sollte im Verhältnis zu den neuen Materialien geschmolzen werden, und es ist rein praktisch, die Kosten für das Umschmelzen zu berechnen).
Die Schmelzkosten pro Kilogramm Angussmaterial betragen 0.93 $. Nach der Berechnung der oben genannten fünf Maschinen umfasst die jährliche Produktion von 1000 Tonnen Laufdüsen fast 10 Millionen Yuan. Berücksichtigt man das Recycling fehlerhafter Produkte, ist diese Zahl noch alarmierender (z. B. Das durchschnittliche Gussgewicht beträgt 100 Gramm und die Rate fehlerhafter Produkte beträgt 5 %, der Zyklus beträgt 12 Sekunden und die jährliche Rückgewinnung fehlerhafter Produkte beträgt etwa 53). Tonnen). Je größer die Verarbeitungsmenge, desto niedriger sind zwar die Schmelzkosten, Umweltschutz und strenge Qualitätskontrollkosten werden hier jedoch nicht berücksichtigt. Es ist ersichtlich, dass die Kosten für das Umschmelzen des Angusses ziemlich alarmierend sind und die Druckgussanlage die Kosten minimieren muss. Daher ist die Reduzierung des Torgewichts ein wichtiger Schlüssel zur Kostenkontrolle.
- Grundstücksmiete 20.000 HKD
- Ausrüstungsinvestitionsaufteilung von HKD 50.000
- Die Zinsen betragen HKD 5.000
- Wartung und Reparatur HKD 25.000
- Heizölgebühr (100 Liter Ölrückstände pro Tonne · 2 US-Dollar/Liter) 200,000 HKD
- Stromgebühr (1 USD/kWh) 30.000 HKD
- Löhne (einschließlich Betriebspersonal, Managementpersonal, Qualitätskontrollpersonal) 100.000 Hongkong-Dollar
- Metallverlust 5 % (10 USD/kg) 500,000 HKD
- Gesamt: HKD 930.000
Berechnungsmethode zur Aufteilung der Angusskosten
Die Kosten für die Veredelung der Düse müssen in den Produktionskosten des Gussteils enthalten sein. Die gebräuchlichste Methode besteht darin, den Materialeinsatz mit einem festen Prozentsatz zu multiplizieren. Wenn der Rohmaterialpreis beispielsweise 10 $/kg beträgt und die Düsenschmelzkosten 3 % des Gussgewichts betragen, werden 10.3 $ bei der Berechnung des Materialpreises des Gussstücks verwendet. Obwohl diese Methode einfach ist, kann sie zu Abweichungen bei der Kostenberechnung führen und die tatsächlichen Kosten des Wasserrecyclings verschleiern. Nun können Sie zum Vergleich das folgende Beispiel heranziehen:
- Das Nettogewicht von Gussstück A beträgt 400 Gramm und das Gewicht des Düsenkanals beträgt 100 Gramm.
- Das Nettogewicht von Gussstück B beträgt 400 Gramm und das Gewicht des Düsenkanals beträgt 250 Gramm.
Bei Berechnung mit einem festen Prozentsatz:
- Die Kosten für den Guss von A und B sollten gleich sein (10.3 $ x 0.4) = 4.12 $.
Bei Berechnung anhand der tatsächlichen Wiederherstellungskosten:
- Casting A sollte (10 $ x 0.4 + 0.93 $ x 0.1) = 4.093 $ betragen
- Casting B sollte (10 $ x 0.4 + 0.93 $ x 0.25) = 4.233 $ betragen
Dieser Unterschied mag gering erscheinen, aber bei einem Produktionszyklus von 20 Sekunden beträgt die Maschinenauslastung 80 % und die Produktion erfolgt in drei Schichten, jede Maschine produziert 1,261,440 Mal pro Jahr. Der Unterschied ist wie folgt:
- Kosten für die Angussdüse, Gussteil A, Gussteil B
- Differenz Festverhältnismethode HKD 5.197.132 HKD 5.197.132 HKD 0
- Tatsächliche Kostenmethode: 5.163.074 HK$ 5.339.675 HK$ 176.601
- Differenz 34.058 HK$ 142.543 HK$
Wenn die Methode des festen Verhältnisses verwendet wird, sind die Kosten für Guss A und B gleich, tatsächlich sind die Kosten für Guss B jedoch höher. Aus diesem Fall ist ersichtlich, dass die Verwendung der Methode des festen Verhältnisses zur Berechnung von Gussteil B nicht nur die Produktionskosten unterschätzt, sondern auch indirekt die Konstrukteure dazu ermutigt, das Gewicht des Düsenkanals nicht als Ziel zu reduzieren, und die Anwendung des tatsächlichen zu fördern Kostenmethode (siehe Tabelle unten).
Um das Gewicht des Anschnitts zu reduzieren, ist es üblicher, einen kurzen Anschnitt (kurze Düse) zu verwenden und die Dicke der Schablone zu reduzieren. Es verwendet eine längere Maschinendüse (im Allgemeinen 20 mm länger als normal) in Kombination mit einer Anschnittform mit tiefem Hohlraum, um das Gewicht des Angusses zu reduzieren. Das Folgende ist ein neues Heißkammer-Druckguss-Läuferdesign.
Heißkammer-Druckguss-Läuferdesign
Der Druckgusskanal ist der Weg des geschmolzenen Metalls, das von der Düse in den Formhohlraum fließt. Es besteht aus den Zweigen des Angusses und des Ausgusses. Aufgrund der Notwendigkeit, die Gussteile zu befestigen und das Entformen zu erleichtern, muss der Anguss eine Neigung aufweisen. Gleichzeitig kann der Splitterblock auf der beweglichen Schablone die Dicke des Angusses reduzieren; Das Hinzufügen eines Kühlwasserkanals im Splitterblock erleichtert den Ausgleich der Formwärme, verkürzt die Abkühlzeit und zieht das Gussstück heraus und wirft es aus. Eine Anfang der 1970er Jahre vom australischen CSIRO durchgeführte Studie ergab, dass die Zinklegierungsflüssigkeit mit akzeptablen Fehlern im Fall von Druckguss wie folgt zusammengefasst werden kann:
Flüssigkeit verhält sich wie eine inkompressible Flüssigkeit
Beachten Sie die allgemeinen Grundsätze der Strömungsmechanik
Die hohe Reynoldszahl weist darauf hin, dass der Strömungsprozess turbulent ist.
Gemäß den oben genannten Forschungsergebnissen sollte der ideale Fließzustand der Metallschmelze sein:
1. Der Läuferabschnitt ist kreisförmig
Da das Verhältnis von Umfang zu Fläche am geringsten ist, ist der Oberflächenwiderstand des Rohrs mit kreisförmigem Querschnitt am geringsten und somit auch der Druckverlust am geringsten. Gegenüber der gleichen trapezförmigen Querschnittsfläche verringert sich der Umfang um mehr als 20 %.
2. Das Durchflussrohr ist gerade
Gebogene Rohre erzeugen eine Vorströmung, mischen Blasen in die Schmelze und verursachen einen Druckverlust. Insbesondere wenn das Verhältnis Biegeradius/Rohrdurchmesser kleiner als 1 ist, steigt der Druckverlust schnell an.
3. Das Strömungskanalprofil schrumpft im Hinblick auf den Flüssigkeitsfluss allmählich
Die schnelle Änderung des Rohrprofils, egal ob es größer oder kleiner wird, führt zu hohem Druckverlust und Wirbelströmen. Die beste Lösung besteht darin, das Profil schrittweise zu reduzieren, um den durch die Rohroberfläche verursachten Widerstandsverlust auszugleichen.
Bitte bewahren Sie die Quelle und Adresse dieses Artikels für den Nachdruck auf:Das Design und die Anwendung von Heißkanal für Zinkdruckguss
Minghe Casting Company widmet sich der Herstellung und Bereitstellung von hochwertigen und leistungsstarken Gussteilen (die Palette der Metalldruckgussteile umfasst hauptsächlich mainly Dünnwandiger Druckguss,Heißkammerdruckguss,Kaltkammerdruckguss), Runder Service (Druckguss-Service,CNC-Bearbeitung,Formenbau,Oberflächenbehandlung). Alle kundenspezifischen Aluminium-Druckguss-, Magnesium- oder Zamak/Zink-Druckguss- und andere Gussanforderungen können uns gerne kontaktieren.
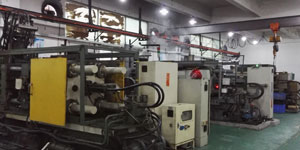
Unter der Kontrolle von ISO9001 und TS 16949 werden alle Prozesse durch Hunderte von fortschrittlichen Druckgussmaschinen, 5-Achsen-Maschinen und anderen Einrichtungen durchgeführt, von Blasgeräten bis hin zu Ultraschall-Waschmaschinen.Minghe verfügt nicht nur über fortschrittliche Ausrüstung, sondern auch über professionelle Team aus erfahrenen Ingenieuren, Bedienern und Inspektoren, um das Design des Kunden zu verwirklichen.
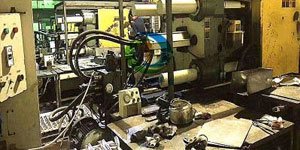
Auftragsfertigung von Druckgussteilen. Zu den Fähigkeiten gehören Kaltkammer-Aluminium-Druckgussteile von 0.15 lbs. bis 6 lbs., Schnellwechseleinrichtung und Bearbeitung. Mehrwertdienste umfassen Polieren, Vibrieren, Entgraten, Kugelstrahlen, Lackieren, Plattieren, Beschichten, Montage und Werkzeugbau. Zu den Materialien, mit denen gearbeitet wird, gehören Legierungen wie 360, 380, 383 und 413.
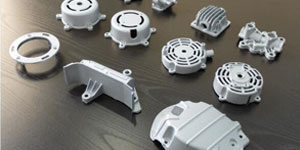
Unterstützung bei der Konstruktion von Zinkdruckguss / gleichzeitige Engineering-Dienstleistungen. Auftragsfertigung von Präzisions-Zink-Druckgussteilen. Es können Miniaturgussteile, Hochdruck-Kokillengussteile, Mehrschieber-Kokillengussteile, konventionelle Kokillengussteile, Einzel- und Einzeldruckgussteile sowie hohlraumdichte Gussteile hergestellt werden. Gussteile können in Längen und Breiten bis zu 24 Zoll in +/-0.0005 Zoll Toleranz hergestellt werden.
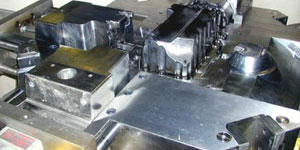
ISO 9001: 2015 zertifizierter Hersteller von Magnesium-Druckguss. Zu den Fähigkeiten gehören Hochdruck-Magnesium-Druckguss bis zu 200 Tonnen Heißkammer und 3000 Tonnen Kaltkammer, Werkzeugdesign, Polieren, Formen, Bearbeitung, Pulver- und Flüssiglackierung, vollständige Qualitätssicherung mit KMG-Fähigkeiten , Montage, Verpackung & Lieferung.
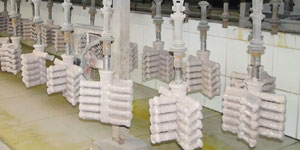
ITAF16949-zertifiziert. Zusätzlicher Casting-Service inklusive Feinguss,Sandguss,Schwerkraftguss, Verlorener Schaumguss,Schleuderguss,Vakuumgießen,Dauerguss,.Zu den Fähigkeiten gehören EDI, technische Unterstützung, Volumenmodellierung und Sekundärverarbeitung.
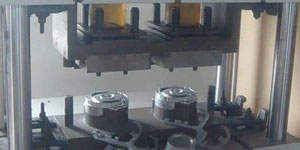
Gussindustrie Teile-Fallstudien für: Autos, Fahrräder, Flugzeuge, Musikinstrumente, Wasserfahrzeuge, optische Geräte, Sensoren, Modelle, elektronische Geräte, Gehäuse, Uhren, Maschinen, Motoren, Möbel, Schmuck, Vorrichtungen, Telekommunikation, Beleuchtung, medizinische Geräte, Fotogeräte, Roboter, Skulpturen, Tongeräte, Sportgeräte, Werkzeuge, Spielzeug und mehr.
Was können wir Ihnen als nächstes helfen?
∇ Zur Startseite gehen für Druckguss China
→Gussteile- Finden Sie heraus, was wir getan haben.
→Bewertete Tipps zu Druckgussdienste
By Minghe Druckgusshersteller |Kategorien: Hilfreiche Artikel |Werkstoff Stichworte: Aluminiumguss, Zinkguss, Magnesiumguss, Titanguss, Edelstahlguss, Messingguss,Bronzeguss,Casting-Video,Unternehmensgeschichte,Aluminiumdruckguss |Kommentare deaktiviert