Die Anwendung der Rapid Prototyping-Technologie im Feinguss
Rapid Prototyping (RP) ist eine in den 1990er Jahren entwickelte Hightech-Technologie. Es kann die Designkonzepte in den Köpfen der Menschen schnell in reale Objekte verwandeln. Besonders hervorzuheben ist, dass der gesamte Produktentwicklungsprozess ohne Formen und Prozessanlagen auskommt, was den Probeproduktionszyklus von Prototypen und neuen Produkten stark verkürzt und schnell zu einem wichtigen Mittel und Werkzeug zur Steigerung der Wettbewerbsfähigkeit von Unternehmen wird. Die von INCAST 2004 (11) veröffentlichte Internet-Fragebogenumfrage zeigt, dass mehr als 93 % von mehr als 400 Feingussherstellern in Europa Rapid Prototyping eingesetzt haben. Alle Befragten sind sich einig, dass der Einsatz dieser neuen Technologie für die Beschleunigung neuer Produkte unerlässlich ist. Es ist sehr wichtig, die Fähigkeit der Unternehmen zu entwickeln und zu verbessern, schnell auf den Markt zu reagieren.
Die Anwendung gängiger Rapid-Prototyping-Methoden beim Feinguss
Die Anwendung der Rapid-Prototyping-Technologie im Feinguss umfasst im Wesentlichen folgende Aspekte:
1. Machen Sie eine Investition
Bei der Herstellung von Mustern kann die Rapid-Prototyping-Maschine nicht nur dreidimensionale geometrische Modelle eingeben, die von anderer CAD-Software erstellt wurden, sondern auch Datendateien empfangen, die durch industrielle CT (Computertomographie) gescannt wurden. Scannen Sie beispielsweise zuerst das Teil (Propellerschraube, Abbildung 12-1a) mittels CT, um ein zweidimensionales Bild seines Querschnitts zu erhalten (Abbildung 12-1b). Anschließend kombiniert die Bildverarbeitungssoftware die zweidimensionalen Bilder jedes Abschnitts (Abbildung 12-1c) zu einem dreidimensionalen geometrischen Modell (Abbildung 12-1d). Senden Sie es dann an die Rapid-Prototyping-Maschine, um ein Muster zu erstellen (Abbildung 12-1e) [2]. Diese Wiederherstellungs-(Reverse-)Engineering-Methode kann nicht nur Maschinenteile restaurieren, sondern auch bestimmte menschliche Organe imitieren.
2. Herstellung von Formen (Formpressen) und anderen Prozessgeräten
Es gibt zwei Methoden zur Herstellung von Präzisionsgussformen durch Rapid Prototyping: Eine besteht darin, zuerst eine Urform herzustellen und dann ein Epoxid- oder Silikongummiprofil neu zu erstellen; die andere Methode besteht darin, den im CAD-System generierten dreidimensionalen Profilierungsblock zu verwenden. Das geometrische Modell wird direkt in die Rapid-Prototyping-Maschine eingegeben, um Harzformen herzustellen. Diese Art der Profilierung eignet sich vor allem für die Kleinserienfertigung (dutzende Stückzahlen). Wenn eine Metallschicht von etwa 2 mm Dicke auf die Oberfläche der Urform gesprüht wird und anschließend Epoxidharz eingefüllt wird, um ein Metall-Epoxid-Verbundprofil herzustellen, kann es die Anforderungen zur Herstellung von Hunderten von Präzisionsgussteilen erfüllen. Bei Verwendung des SLS-Verfahrens wird beispielsweise das Bearbeitungsobjekt von Harzpulver zu Stahlpulver mit einer dünnen Schicht aus duroplastischem Harz auf der Oberfläche geändert, lasergesintert, um einen Pressling zu bilden, und dann gebrannt, um das Harz zu entfernen, und schließlich Kupferflüssigkeit wird in die Poren des Presslings infiltriert. Die resultierende Profilierung ist in Bezug auf Festigkeit und Wärmeleitfähigkeit Metall ähnlich. Darüber hinaus kann die Rapid-Prototyping-Technologie auch verwendet werden, um bestimmte unregelmäßig geformte Formen herzustellen.
3. Direkte Herstellung von Formgussteilen
In den frühen 1990er Jahren führte das Sandiana National Laboratory in den USA eine spezielle Studie namens Fast Casting (FastCAST) durch, die den Namen Direct Shell Casting (DSPC) erhielt. Leider gibt es später nur sehr wenige Berichte.
1994 entwickelte die Z Corporation aus den USA erfolgreich die 3D-Drucktechnologie 3D Printing. Die Technologie wurde ursprünglich von Professor Ely Sachs vom Massachusetts Institute of Technology erfunden und patentiert. Das Grundprinzip ähnelt dem SLS-Verfahren. Zunächst wird mit einer Walze eine Schicht aus feuerfestem Material oder Kunststoffpulver aufgesprüht. Der Unterschied zu SLS besteht darin, dass anstelle eines Laseremissionskopfes ein Tintenstrahldruckkopf angesteuert wird, um Klebstoff zum "Drucken" entsprechend der Querschnittsform des Produkts zu sprühen. Wiederholen Sie die obigen Aktionen, bis die Teile fertig sind, daher heißt es "3D-Drucktechnologie". Seine Vorteile sind niedrige Betriebs- und Materialkosten sowie eine hohe Geschwindigkeit. Wenn das gespritzte Pulver ein gemischtes Pulver aus Gips und Keramik ist, kann es direkt und schnell zu einer Form (Gipsform) zum Gießen von Aluminium-, Magnesium-, Zink- und anderen Nichteisenlegierungsgussteilen verarbeitet werden, die als ZCast bezeichnet wird (Abbildung 12-2) .
Der Vergleich häufig verwendeter Rapid-Prototyping-Methoden Anwendungseffekte
Derzeit sind die populäreren Rapid-Prototyping-Methoden in der tatsächlichen Produktion dreidimensionale Lithographie (SLA), selektives Lasersintern (SLS), Schmelzabscheidung (FDM), Laminatherstellung (LOM) und Direktformguss (DSPC). Warten Sie. In den letzten Jahren haben viele ausländische Forschungseinrichtungen die oben genannten Verfahren hinsichtlich der Qualität der Produktionsmuster und der Leistung beim Feinguss verglichen. Die Ergebnisse sind wie folgt:
- 1) Die SLA-Methode hat die höchste Maßgenauigkeit des Musters, gefolgt von SLS und FDM, und die LOM-Methode ist die niedrigste [4].
- 2) Oberflächenrauheit des Musters Die Oberfläche des Musters wird poliert und endbearbeitet und mit einem Oberflächenrauheitsmesser gemessen. Die Ergebnisse sind in Tabelle 12-1 [4] dargestellt. Es ist ersichtlich, dass die Oberflächenrauheit bei den SLA- und LOM-Methoden feiner ist und die FDM-Methode am dicksten ist.
- 3) Die Fähigkeit, feine Teile zu reproduzieren Die Fähigkeit dieser vier Verfahren, feine Teile zu reproduzieren, wurde mit einer Zahnstange mit einer Zahnteilung von etwa 3 mm als Gegenstand untersucht. Als Ergebnis ist SLA das beste und FDM das schlechteste [4].
- 4) Leistung beim Feinguss Unter den oben genannten vier Verfahren ist das Produkt selbst ein Wachsformverfahren (wie FDM oder SLS), das sich leicht an die Anforderungen des Feingussverfahrens anpassen lässt und zweifellos besser funktioniert. Kunstharz- oder Papiermodelle können zwar auch gebrannt werden, sind aber nicht so einfach an die Anforderungen des Feingusses anzupassen wie Wachsformen. Kontinuierliche Verbesserungen sind erforderlich, um Nachteile zu vermeiden.
Vergleich der Oberflächenrauheit von Mustern
Messteil | LOM | SLS | FDM | SLA |
Ebene Ebene | 1.5 | 5.6 | 14.5 | 0.6 |
Schiefe Ebene | 2.2 | 4.5 | 11.4 | 6.9 |
Vertikale Ebene | 1.7 | 8.2 | 9.5 | 4.6 |
Insgesamt gesehen ist das SLA-Verfahren zwar inkompatibel mit dem Feingussverfahren, aber wegen seiner guten Maßhaltigkeit und Oberflächenqualität beliebt. Im Ausland, insbesondere in der Luftfahrt- und Militärindustrie, sind Feingussunternehmen weit verbreitet. Obwohl die Qualität des SLS-Verfahrens der von SLA leicht unterlegen ist, lässt es sich leicht an die Prozessanforderungen des Feingusses anpassen. Daher werden immer mehr Anwendungen im häuslichen Feinguss verwendet. Obwohl sich das FDM-Verfahren am einfachsten an die Prozessanforderungen des Feingusses anpassen lässt, sind die Maßhaltigkeit und Oberflächenqualität der Wachsformen nicht zufriedenstellend; Das LOM-Verfahren ist zwar von akzeptabler Qualität, lässt sich jedoch nur schwer an den Feinguss anpassen. Daher ist die Anpassung an den Feinguss schwierig. Die Förderung und Anwendung der beiden Verfahren im Feinguss unterliegt gewissen Einschränkungen.
Neue Entwicklungen bei der Anwendung von SLA und SLS im Feinguss
1. Neues lichthärtendes Harz
Die SLA-Methode wurde bereits 1987 kommerzialisiert. Ursprünglich wurde sie verwendet, um physikalische Modelle und Prototypen mit bestimmten Funktionen herzustellen. In den frühen 1990er Jahren wurde die QuickCast-Software von 3D System Inc in den USA erfolgreich entwickelt, die es der SLA-Rapid-Prototyping-Maschine ermöglichte, eine wabenförmige Struktur zu erzeugen (Abbildung 12-3a) und gleichzeitig ein glattes und dichtes Erscheinungsbild beizubehalten (Abbildung 12 -3b) , spart nicht nur 90% der Formstoffe, sondern auch beim Brennen der Schale kollabiert das Modell zunächst nach innen, ohne die Schale zu knacken. Darüber hinaus stellte sich nach und nach heraus, dass lichthärtende Kunststoffe für den Formenbau auch folgende besondere Anforderungen erfüllen müssen:
- Viskosität – Wenn die Harzviskosität zu hoch ist, wird es schwierig, das verbleibende Harz in der Kavität nach der Modellherstellung abzulassen. Wenn zu viel Harzreste vorhanden sind, kann es beim Backen trotzdem zu Rissen in der Schale kommen, daher ist oft eine Zentrifugalabscheidung erforderlich. Mittel. Außerdem ist die Oberfläche des fertigen Musters auch schwer zu reinigen.
- Restasche – das ist vielleicht die wichtigste Voraussetzung. Wenn die Restasche nach dem Einbrennen der Schale nichtmetallische Einschlüsse und andere Defekte auf der Oberfläche des Gussstücks verursacht.
- ·Schwermetallgehalt – dies ist besonders wichtig für das Gießen von Superlegierungen. Antimon ist beispielsweise ein relativ häufiges Element in lichthärtenden SLA-Kunststoffen. Wenn es nach dem Brennen der Schale in der Restasche auftaucht, kann es die Legierung verunreinigen und sogar zum Verschrotten des Gussstücks führen.
- Dimensionsstabilität – die Größe des Musters sollte während der gesamten Operation stabil bleiben. Aus diesem Grund ist auch die geringe Feuchtigkeitsaufnahme des Harzes sehr wichtig.
DSM Somos aus den USA hat in den letzten Jahren erfolgreich einen neuartigen lichthärtenden Kunststoff Somos 10120 entwickelt, der die oben genannten Hauptanforderungen erfüllt und von Feingussherstellern sehr beliebt ist. Dieses neue Produkt wurde in drei verschiedenen Feingussanlagen in drei Legierungen (Aluminium, Titan und Kobalt-Molybdän-Legierung) gegossen und zufriedenstellende Ergebnisse erzielt.
2. Verwenden Sie das SLA-Modell für die Kleinserienproduktion
Bei der Kleinserienfertigung von Präzisionsgussteilen mit SLA-Modellen sind zwei Hauptaspekte zu beachten: Zum einen die Maßhaltigkeit, die Modell und Gussteil erreichen können, und zum anderen, ob Produktionskosten und Lieferzeit Vorteile haben. Mehrere Präzisionsgusswerke in den Vereinigten Staaten, wie Solidiform, Nu-Cast, PCC und Uni-Cast, haben SLA-Modelle verwendet, um Hunderte von Gussteilen zu gießen. Nach der tatsächlichen Messung der Gussgröße zeigt die statistische Analyse, dass das neue lichthärtende Harz 11120 von DSM Somos verwendet wird. Mit der QuickCast-Technologie weist das resultierende SLA-Muster eine Größenabweichung von nicht mehr als 50% des Gusstoleranzwertes auf. Die Größe der meisten Gussteile erfüllt die Toleranzanforderungen und die Passrate beträgt mehr als 95 % (Abbildung 12-4) [7].
Obwohl die Kosten für die Herstellung eines SLA-Musters viel höher sind als die der Herstellung derselben Wachsform und es dauert länger, besteht jedoch keine Notwendigkeit, die Profilierung zu entwerfen und herzustellen. Daher sind bei der Herstellung eines Einzelstücks in Kleinserien die Kosten und die Lieferzeit immer noch Vorteile. Je komplexer der Guss, desto deutlicher wird dieser Vorteil. Nehmen Sie das komplex geformte Luftfahrt-Präzisionsgussteil von Nu-Cast als Beispiel (Abbildung 12-5) [7], die Kosten für den Formenbau betragen etwa 85,000 US-Dollar, 4 Wachsformen werden täglich hergestellt und die Kosten für jedes Wachs Schimmel (einschließlich Materialien und Arbeit) 150 USD. Bei Anwendung der SLA-Methode kostet jedes SLA-Modell 2846 US-Dollar, aber es müssen keine Formen konstruiert und hergestellt werden. Nach dieser Berechnung sind die Kosten für die Verwendung von SLA-Formen niedriger als die von Wachsformen, wenn die Produktion weniger als 32 Stück beträgt; bei mehr als 32 Stück sind die Kosten höher als bei Wachsformen (Abbildung 12-6); Mit Wachsformen dauert es 14-16 Wochen, um Formen zu entwerfen und herzustellen, und die SLA-Form erfordert keine Form. Wenn die Ausgabe weniger als 87 Stück beträgt, ist die Lieferung von Gussteilen bei Verwendung von SLA-Formen daher schneller als bei Wachsformen (Abbildung 12-7). Aber mehr als 87 Stück ist die Wachsform schneller [7]. Ein weiterer Faktor, der berücksichtigt werden muss, ist, dass bei Verwendung einer Wachsform die Form bei der Aktualisierung des Produkts neu hergestellt werden muss, was kostspielig ist; während beim SLA-Erscheinungsbild nur das CAD-Geometriemodell geändert werden muss, was viel einfacher und schneller ist, als die Form neu zu erstellen. .
3. SLS gesintertes Polystyrolpulver imprägniertes Wachsmodell
SLS hat zunächst mit einem Laser ein spezielles Wachspulver in eine Wachsform gesintert, die für die Prozesseigenschaften des Feingusses sehr gut geeignet ist. Bereits Ende 1990 gab es in den USA mehr als 50 Gießereien, die etwa 3000 Wachsformen herstellten und erfolgreich gießen. Produzieren Sie eine Vielzahl von Metallgussteilen. Wachspulver ist jedoch nicht das idealste Formmaterial. Die Festigkeit der daraus hergestellten Wachsform ist unzureichend, und sie wird leicht weich und verformt sich, wenn die Temperatur hoch ist, und sie bricht leicht, wenn die Temperatur niedrig ist. Daher versuchten in den frühen 1990er Jahren einige SLA-Anwender in den Vereinigten Staaten, Wachspulver durch thermoplastische Pulver wie Polystyrol (PS) oder Polycarbonat (PC) zu ersetzen. Diese Art von Material wird in eine lockere und poröse Form gebracht (die Porosität beträgt mehr als 25%), wodurch die Gefahr des Quellens und der Rissbildung der Schale beim Entformen verringert wird. Nach dem Brennen der Schale ist der Aschegehalt geringer, aber die Oberfläche des Musters ist rau. Daher muss das Muster nach der Herstellung von Hand gewachst und poliert werden, um die Oberfläche glatt und dicht zu machen. Gegenwärtig ist diese Methode im In- und Ausland weit verbreitet.
Bitte bewahren Sie die Quelle und Adresse dieses Artikels für den Nachdruck auf:Die Anwendung der Rapid Prototyping-Technologie im Feinguss
Minghe Casting Company widmet sich der Herstellung und Bereitstellung von hochwertigen und leistungsstarken Gussteilen (die Palette der Metalldruckgussteile umfasst hauptsächlich mainly Dünnwandiger Druckguss,Heißkammerdruckguss,Kaltkammerdruckguss), Runder Service (Druckguss-Service,CNC-Bearbeitung,Formenbau,Oberflächenbehandlung). Alle kundenspezifischen Aluminium-Druckguss-, Magnesium- oder Zamak/Zink-Druckguss- und andere Gussanforderungen können uns gerne kontaktieren.
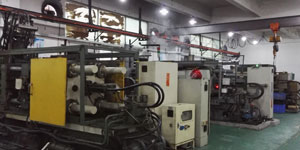
Unter der Kontrolle von ISO9001 und TS 16949 werden alle Prozesse durch Hunderte von fortschrittlichen Druckgussmaschinen, 5-Achsen-Maschinen und anderen Einrichtungen durchgeführt, von Blasgeräten bis hin zu Ultraschall-Waschmaschinen.Minghe verfügt nicht nur über fortschrittliche Ausrüstung, sondern auch über professionelle Team aus erfahrenen Ingenieuren, Bedienern und Inspektoren, um das Design des Kunden zu verwirklichen.
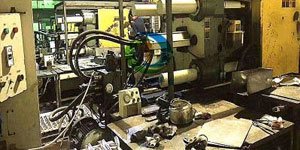
Auftragsfertigung von Druckgussteilen. Zu den Fähigkeiten gehören Kaltkammer-Aluminium-Druckgussteile von 0.15 lbs. bis 6 lbs., Schnellwechseleinrichtung und Bearbeitung. Mehrwertdienste umfassen Polieren, Vibrieren, Entgraten, Kugelstrahlen, Lackieren, Plattieren, Beschichten, Montage und Werkzeugbau. Zu den Materialien, mit denen gearbeitet wird, gehören Legierungen wie 360, 380, 383 und 413.
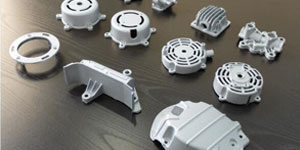
Unterstützung bei der Konstruktion von Zinkdruckguss / gleichzeitige Engineering-Dienstleistungen. Auftragsfertigung von Präzisions-Zink-Druckgussteilen. Es können Miniaturgussteile, Hochdruck-Kokillengussteile, Mehrschieber-Kokillengussteile, konventionelle Kokillengussteile, Einzel- und Einzeldruckgussteile sowie hohlraumdichte Gussteile hergestellt werden. Gussteile können in Längen und Breiten bis zu 24 Zoll in +/-0.0005 Zoll Toleranz hergestellt werden.
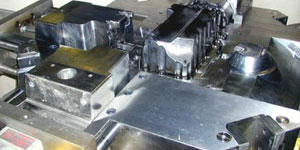
ISO 9001: 2015 zertifizierter Hersteller von Magnesium-Druckguss. Zu den Fähigkeiten gehören Hochdruck-Magnesium-Druckguss bis zu 200 Tonnen Heißkammer und 3000 Tonnen Kaltkammer, Werkzeugdesign, Polieren, Formen, Bearbeitung, Pulver- und Flüssiglackierung, vollständige Qualitätssicherung mit KMG-Fähigkeiten , Montage, Verpackung & Lieferung.
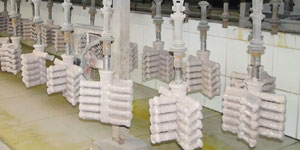
ITAF16949-zertifiziert. Zusätzlicher Casting-Service inklusive Feinguss,Sandguss,Schwerkraftguss, Verlorener Schaumguss,Schleuderguss,Vakuumgießen,Dauerguss,.Zu den Fähigkeiten gehören EDI, technische Unterstützung, Volumenmodellierung und Sekundärverarbeitung.
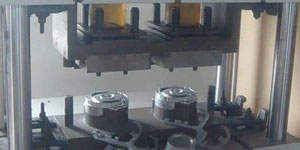
Gussindustrie Teile-Fallstudien für: Autos, Fahrräder, Flugzeuge, Musikinstrumente, Wasserfahrzeuge, optische Geräte, Sensoren, Modelle, elektronische Geräte, Gehäuse, Uhren, Maschinen, Motoren, Möbel, Schmuck, Vorrichtungen, Telekommunikation, Beleuchtung, medizinische Geräte, Fotogeräte, Roboter, Skulpturen, Tongeräte, Sportgeräte, Werkzeuge, Spielzeug und mehr.
Was können wir Ihnen als nächstes helfen?
∇ Zur Startseite gehen für Druckguss China
→Gussteile- Finden Sie heraus, was wir getan haben.
→Bewertete Tipps zu Druckgussdienste
By Minghe Druckgusshersteller |Kategorien: Hilfreiche Artikel |Werkstoff Stichworte: Aluminiumguss, Zinkguss, Magnesiumguss, Titanguss, Edelstahlguss, Messingguss,Bronzeguss,Casting-Video,Unternehmensgeschichte,Aluminiumdruckguss |Kommentare deaktiviert