Der Entwicklungstrend von Automobilgussteilen und seiner Fertigungstechnologie
Gießen ist eines der ältesten Verfahren der Metallumformung. Etwa 15 bis 20 % der Autoteile sind Gussteile, die mit unterschiedlichen Gussverfahren hergestellt werden. Diese Gussteile sind hauptsächlich Schlüsselkomponenten des Energiesystems und wichtige Strukturkomponenten. Gegenwärtig ist die Produktionstechnologie für Automobilgussteile in entwickelten Ländern der europäischen und amerikanischen Automobilindustrie fortschrittlich und weist eine gute Produktqualität, eine hohe Produktionseffizienz und eine geringe Umweltverschmutzung auf. Gussrohstoffe und -hilfsstoffe wurden serialisiert und standardisiert und der gesamte Produktionsprozess wurde mechanisiert, automatisiert und intelligent. Diese Länder nutzen im Allgemeinen digitale Technologie, um das Niveau der Gussprozessgestaltung zu verbessern. Die Ablehnungsrate bei Gussteilen liegt bei etwa 2 bis 5 %, und es wurde ein länderübergreifendes Servicesystem eingerichtet und ein technischer Netzwerksupport implementiert. Im Gegensatz dazu ist die Produktion von Automobilgussteilen in meinem Land zwar relativ groß, bei den meisten handelt es sich jedoch um Schwarzgussteile mit relativ geringem Mehrwert und technischem Inhalt sowie relativ einfacher Struktur, die weit vom ausländischen Niveau entfernt ist. In diesem Artikel wird hauptsächlich die Entwicklungsrichtung von Automobilgussteilen und Automobiltechnologie anhand der Entwicklungsbedürfnisse der Automobilenergieeinsparung und des Umweltschutzes erörtert.
Integriertes Design von Automobilgussteilen
Angesichts der steigenden Anforderungen an die Energieeinsparung und den Umweltschutz von Automobilen sowie die Reduzierung der Produktionskosten werden wir die Vorteile des Gießens voll ausnutzen, um das Gießen integrierter Teile durch vernünftige Konstruktion und strukturelle Optimierung mehrerer durch Stanzen, Schweißen, Formen usw. geformter Teile zu realisieren. Schmieden und Gießen. Durch das Umformen kann das Gewicht von Teilen effektiv reduziert und unnötige Verarbeitungsprozesse reduziert werden, wodurch leichte und leistungsstarke Teile erzielt werden.
Die Hauptform des herkömmlichen monolithischen Achsgehäusegusses besteht darin, dass nahtlose Stahlrohre als Halbachshülsen in die beiden Enden des Achsgehäuses eingepresst und mit Stiften befestigt werden, um die Achsgehäusebaugruppe zu bilden. Um die Festigkeit und Steifigkeit des Achsgehäuses weiter zu verbessern und den Prozess zu vereinfachen, hat die FAW Group ein integriertes Achsgehäuse entwickelt, bei dem die Achshülsen (die Teile auf beiden Seiten des Achsgehäuses in Abbildung 1) direkt angegossen sind Achsgehäuse. Die Verarbeitung ist schwierig, die Kostenreduzierung ist größer, die Struktur des Achsgehäuses ist tendenziell einfacher und die Steifigkeit des Achsgehäuses ist besser, es kann in eine komplexe und ideale Form gebracht werden, die Wandstärke kann geändert werden, eine ideale Spannungsverteilung kann erreicht werden und seine Festigkeit und Festigkeit ist besser Steifigkeit sind beide groß, arbeiten zuverlässig. Durch die Integration der Achshülse wird die Größe des Gussteils deutlich vergrößert. Die Länge des Gussteils beträgt 2 mm und das Einzelstückgewicht übersteigt 258 kg. Angesichts der Eigenschaften dieses integrierten Gussteils hat das Unternehmen eine eigene Produktionslinie eingerichtet, um die Produktion sicherzustellen.
Der Entwicklungstrend der Integration von Automobilgussteilen ist bei der Entwicklung von Gussteilen aus Nichteisenlegierungen deutlicher zu erkennen. Um die Eigenschaften des Gussprozesses, der die Herstellung komplexer Strukturgussteile ermöglicht, voll auszunutzen, wurde eine integrierte Konstruktion von Hochdruckgussteilen wie Türinnenverkleidungen, Sitzrahmen, Instrumententafelrahmen, Frontrahmen und Brandschutzwänden entwickelt aufgetaucht. Die Abmessungen sind deutlich größer als die derzeit produzierten. Bei Gussteilen ist für die Produktion eine Druckgussmaschine mit einer Tonnage von 4 bis 000 Tonnen oder sogar mehr erforderlich.
Leichtbau von Automobilgussteilen
Unter der Prämisse, die Festigkeit und Sicherheit des Fahrzeugs zu gewährleisten, reduzieren Sie das Leergewicht des Fahrzeugs so weit wie möglich, um ein geringes Gewicht zu erreichen, wodurch die Leistung des Fahrzeugs verbessert, der Kraftstoffverbrauch gesenkt und die Abgasverschmutzung verringert wird. Pro 100 kg Reduzierung des Leergewichts kann der Kraftstoffverbrauch pro 100 Kilometer um 0.3 bis 0.6 l gesenkt werden. Bei einer Reduzierung des Fahrzeuggewichts um 10 % kann die Kraftstoffeffizienz um 6 bis 8 % gesteigert werden. Mit dem Bedarf an Umweltschutz und Energieeinsparung ist der Leichtbau von Automobilen zum Trend der weltweiten Automobilentwicklung geworden, und der Leichtbau von Automobilgussteilen ist auch zu einer der wichtigen Entwicklungsrichtungen von Automobilgussteilen geworden.
Leichtbau von Automobilgussteilen
Aufgrund der Notwendigkeit des Gesamtsicherheitsfaktors von Gussteilen ist die Konstruktion mit gleicher Dicke eine der Hauptkonstruktionsmethoden für Automobilgussteile. Der Hauptnachteil der Konstruktion mit gleicher Dicke besteht jedoch darin, dass die strukturelle Leistung nicht vollständig genutzt werden kann und das Gewicht des Gussteils erhöht wird. Verwenden Sie CAE-Analyse, Topologieoptimierung und andere Methoden, um das Design der Teile so zu optimieren, dass die Spannungswerte der Teile nahe beieinander liegen, dh die Wandstärke jedes Teils ist inkonsistent und die Teile sind klein Kräfte werden ausgedünnt oder unnötig, um die Teile zu verkleinern. das Gewicht von. In Anbetracht der Tatsache, dass die Gussformung die Formung von Gussteilen mit komplexer Struktur ermöglichen kann, können verschiedene unregelmäßig geformte Querschnitte realisiert werden. Verwenden Sie beim Entwurf CAE oder Topologieoptimierung, um eine Spannungsanalyse für Komponenten durchzuführen. Bestimmen Sie anhand der Kraftverteilung die Form des Teils und die Materialstärke des jeweiligen Teils. Durch Verstärken, Bohren von Löchern und Verdicken der Gussteile kann das Gewicht der Teile erheblich reduziert werden.
Gussteile aus Leichtmetall für Automobile
Der Einsatz von Leichtmetallwerkstoffen wie Aluminium und Magnesium ist derzeit die wichtigste Gewichtsreduzierungsmaßnahme der Automobilhersteller in verschiedenen Ländern. Die Dichte von Aluminium beträgt nur 1/3 der von Stahl und es weist eine ausgezeichnete Korrosionsbeständigkeit und Duktilität auf. Magnesium hat eine geringere Dichte, nur 2/3 der von Aluminium, und verfügt unter Hochdruckgussbedingungen über eine ausgezeichnete Fließfähigkeit. Die spezifische Festigkeit (Verhältnis von Festigkeit zu Masse) von Aluminium und Magnesium ist recht hoch, was eine entscheidende Rolle bei der Reduzierung des Eigengewichts und der Verbesserung der Kraftstoffeffizienz spielt. Die zunehmende Wettbewerbsfähigkeit der US-amerikanischen Automobilindustrie in den letzten zwei Jahren steht in engem Zusammenhang mit der groß angelegten Einführung von Aluminium-Magnesium-Strukturgussteilen und integrierten Gussteilen.
Die neue 5er-Reihe des deutschen BMW-Unternehmens ist mit einem Reihensechszylinder-Reihenmotorblock aus Magnesium-Aluminium-Verbundwerkstoff der neuesten Generation ausgestattet. Das Gewicht wurde im Vergleich zur Vorgängergeneration um 10 kg reduziert, was die Leistung und den Kraftstoffverbrauch erheblich verbessert Wirtschaft. Es ist jedoch zu beachten, dass die Rohstoffpreise für Leichtmetalllegierungen wie Aluminium und Magnesium deutlich höher sind als die für Stahlwerkstoffe, was ihre breitere Anwendung in der Automobilindustrie einschränkt. Doch trotz der relativ hohen Rohstoffpreise steigt der aktuelle Verbrauch von Magnesium- und Aluminiumgussteilen für Fahrräder von Jahr zu Jahr. Einerseits hat der technische Fortschritt den Kostenanstieg kompensiert. Andererseits hat der Wettbewerb auf dem Markt die Automobilhersteller dazu gezwungen, ihre Gewinne zu reduzieren und mehr Leichtmetalllegierungen einzusetzen. Um jedoch die Menge an Leichtlegierungen deutlich zu erhöhen und den Einkaufspreis von Magnesium- und Aluminiumbarren zu senken, ist die Entwicklung fortschrittlicher Umformtechnologie einer der Schlüssel.
Hochleistungsfähige Gussmaterialien für die Automobilindustrie
Eine der Methoden, um das Gewicht des Gussstücks effektiv zu reduzieren, besteht darin, die Leistung des Materials zu verbessern, sodass das Stückgewicht des Teils höheren Belastungen standhalten kann. Strukturgussteile vom Halterungstyp machen einen großen Anteil der Automobilgussteile aus, daher ist die Entwicklung dieser Gussteile zu einem Schwerpunkt geworden. Durch Wärmebehandlung und andere Maßnahmen wird die Mikrostruktur des Materials verändert und dadurch die Festigkeit, Steifigkeit oder Zähigkeit der Teile verbessert, wodurch das Gewicht der Teile effektiv reduziert werden kann.
Austempered Sphäroguss hat nicht nur eine höhere Festigkeit als gewöhnliche Gussstahlwerkstoffe, sondern auch eine geringere Dichte als Stahl. Seine Dichte beträgt 7.1 g/cm3, während die Dichte von Gussstahl 7.8 g/cm3 beträgt, was in den letzten Jahren ein weithin empfohlenes Material ist. . Es wird austemperierter Sphäroguss verwendet, der bei gleicher Gussgröße 10 % leichter ist als Stahlgussteile. Die Dongfeng Motor Corporation hat eine Leichtgewichtsüberprüfung an einem bestimmten Nutzfahrzeugtyp durchgeführt, bei dem austemperiertes Sphäroguss anstelle von Stahlgussteilen verwendet wurde. Angesichts der hohen Festigkeitseigenschaften von Teilen aus vergütetem Sphäroguss wurden im Expertenforum 14 Aufhängungsteile neu konstruiert. Generell geht der Materialaustausch bei Automobilgussteilen häufig mit der Leichtbauweise der Teile einher.
Bei Gussteilen aus Aluminiumlegierungen und Magnesiumlegierungen werden stattdessen hochfeste und hochzähe Materialien verwendet. Aufbauend auf der ursprünglichen Gewichtsreduzierung durch Leichtmetalle werden Hochleistungswerkstoffe zur weiteren Gewichtsreduzierung eingesetzt. General Motors aus den USA verwendet stattdessen die Hochleistungslegierung AE44. Die ursprüngliche Aluminiumlegierung verwendet Hochdruckguss zur Herstellung des Hilfsrahmens, wodurch das Gewicht der Aluminiumlegierung um weitere 6 kg reduziert wird.
Digitalisierung der Automobilgussentwicklung
Die umfassende Kombination aus Automobilgussentwicklung und digitaler Technologie kann das Niveau der Gusstechnologie erheblich verbessern und den Produktdesign- und Versuchsproduktionszyklus verkürzen. Derzeit wird die digitale Fertigungstechnologie in großem Umfang bei der Entwicklung von Automobilgussteilen eingesetzt. In der Phase des Gussstrukturdesigns und des Gussprozessdesigns sind 3D-Designsoftware wie Pro/E, CATIA und UG weit verbreitet, und einige fortschrittliche Gussunternehmen haben papierloses Design realisiert. Software wie MAGMA, ProCAST und Huazhu CAE werden häufig zur Simulation des Erstarrungsprozesses, der Mikrostruktur, der Zusammensetzungsseigerung und der Materialeigenschaften von Automobilgussteilen verwendet. Es kann auch das Geschwindigkeitsfeld, das Konzentrationsfeld, das Temperaturfeld und die Phase im Gießprozess analysieren. Durch die Simulation von Feldern, Spannungsfeldern usw. kann sichergestellt werden, dass der Prozessplan vor der Massenproduktion optimiert wird.
Um den Anforderungen einer schnellen Entwicklung von Automobilgussteilen gerecht zu werden, wurde RP (Rapid Prototyping-Technologie) auf der Grundlage der Konstruktion und Entwicklung von CAD/CAE in großem Umfang für die schnelle Testproduktion von Automobilgussteilen eingesetzt. Nach Erhalt der ursprünglichen CAD/CAE-Daten wird die Schicht-für-Schicht-Methode angewendet, um den Prototyp des Gussstücks oder den Prototyp der Form zu erhalten, die zur Bildung des Gussstücks durch Kleben, Sintern oder Sintern erforderlich ist. Erstere können durch Feinguss, Gipsguss und andere Methoden versuchsweise hergestellte Gussproben sein, während letztere direkt als Form zur Herstellung von Sandkernen verwendet werden können und Gussteile durch Kernmontagemodellierung gegossen werden können. Darüber hinaus kann mit dem Pulver-Laser-Sinter-Verfahren (SLS) die Herstellung von Sandkernen und Sandformen direkt abgeschlossen werden, um die für die Probefertigung von Gussteilen benötigten Sandformen zu erhalten. Bei Außenformen mit relativ einfachen Strukturen können CNC-Werkzeugmaschinen auch verwendet werden, um CAM mit bearbeitbaren Kunststoffen zu verarbeiten, um den Kernkasten und das Muster zu erhalten, die für die Probeproduktion von Gussteilen erforderlich sind, oder um den Sandblock direkt zu verarbeiten, um die Sandform der Außenform zu erhalten direkt.
Im Allgemeinen hat die digitale Technologie alle Aspekte des Gussstückdesigns, der Entwicklung und der Versuchsproduktion durchdrungen und die Geschwindigkeit und Effizienz der Gussstückentwicklung effektiv verbessert. Das Hauptproblem besteht derzeit darin, dass die digitalen Technologien Design, Analyse und Rapid Manufacturing unabhängig voneinander sind. Wenn der Entwicklungsprozess von einer Phase in eine andere übergeht, sind auch recht mühsame Datenkonvertierungsarbeiten erforderlich. Es besteht die Hoffnung, dass in Zukunft eine einheitliche Datenschnittstellenplattform für die digitale Technologie entwickelt werden kann, die in allen Aspekten der Gussteilentwicklung zum Einsatz kommt, und dass standardisierte Datenkonvertierungsstandards etabliert werden können, um eine nahtlose Datenkonvertierung zwischen verschiedenen Softwareprogrammen zu erreichen und so eine weitere Steigerung zu erreichen die Entwicklungsgeschwindigkeit von Gussteilen.
Produktionstechnologie für dünnwandige Gussteile mit komplexer Struktur
Mit der Entwicklung der Automobilindustrie und der Forderung nach Energieeinsparung und Emissionsreduzierung werden Automobilteile immer leichter. Durch die dünnwandige Bauweise ist die Gewichtsreduzierung eine wichtige Entwicklungsrichtung bei Motorblöcken. Nehmen wir als Beispiel FAW Casting Co., Ltd. für die Produktion von Zylinderblöcken aus Gusseisen bei FAW-Volkswagen. Der früh produzierte 06A-Zylinderblock hat eine Wandstärke von 4.5 mm ± 1.5 mm und der EA111-Zylinderblock hat eine Wandstärke von 4 mm ± 1 mm. Der aktuell in Serie gefertigte Zylinderblock EA888Evo2 hat eine Wandstärke von 4 mm ± 1 mm. 3.5 mm ± 0.8 mm, die Produktstruktur des Zylinderblocks EA888Gen.3 der nächsten Generation ist komplexer, seine Wandstärke beträgt nur 3 mm ± 0.5 mm, es ist derzeit der dünnste Grauguss-Zylinderblock. Obwohl es in der Massenproduktion Probleme mit gebrochenen Kernen, schwebenden Kernen und großen Wandstärkenschwankungen gibt, kann das weit verbreitete horizontale Gießverfahren durch die Kontrolle der Qualität von Sandkernen und Formsand dennoch die Produktionsanforderungen von EA888Evo2-Zylindern erfüllen. Die Produktionsanforderungen des EA888Gen.3-Zylinderblocks können jedoch nicht erfüllt werden, sodass der gesamte vertikale Gussprozess der Kernbaugruppe übernommen werden muss.
Fertigungstechnologie für große Strukturteile aus Aluminium-Magnesium-Legierung
Angesichts der steigenden Anforderungen an Energieeinsparung, Umweltschutz und Reduzierung der Komponentenkosten sind großformatige Strukturgussteile aus Aluminium-Magnesium-Legierungen zu einem wichtigen Entwicklungstrend geworden, und auch ihre Herstellungstechnologie ist zu einem aktuellen Entwicklungsschwerpunkt geworden. Zu den wichtigsten Produktionstechnologien für großformatige Strukturteile aus Aluminium-Magnesium-Legierung gehören derzeit Hochdruckguss, Squeeze-Casting und Niederdruckguss. Aufgrund der hohen Produktionseffizienz des Hochdruckgusses und der guten Produktqualität ist es derzeit zum Hauptproduktionsverfahren geworden. Die Entwicklung seiner Fertigungstechnologie konzentriert sich hauptsächlich auf die leichte Mitnahme von Gas während des Hochdruckgussverfahrens und die Bildung von Poren im Inneren der Gussteile, was das Problem der Wärmebehandlung nicht verbessern kann.
Das deutsche Unternehmen Fulai hat das Vakuum-Unterdruck-Sauggussverfahren entwickelt. Der gesamte Druckgussprozess wird unter Hochvakuum (weniger als 30 mbar) durchgeführt. Das geschmolzene Metall durchläuft die Form, die Druckkammer und das Saugrohr im Vakuumzustand und wird vom Saugrohr ohne Oxidation aus dem Ofen gesaugt, und der Dampf des Trennmittels wird ebenfalls vom Vakuumsystem abgeführt. Die Hauptmerkmale des oben genannten Vakuum-Unterdruck-Sauggussverfahrens sind: Wenn mit dem quantitativen Gießen begonnen wird, befindet sich das gesamte System in einem Hochvakuumzustand; Beim quantitativen Gießvorgang können das Gas im Hohlraum und das geschmolzene Metall effektiv abgeführt werden. Während des Gießvorgangs kommt es zu keiner Oxidation der Metallschmelze; Während des Gießvorgangs entsteht kein Wärmeverlust, zum Gießen kann eine niedrigere Gießtemperatur verwendet werden und die störungsfreie Laminar-Flow-Befüllung kann unter Echtzeitüberwachung durchgeführt werden. Das obige Verfahren wurde vom Auto Expert Forum erfolgreich auf die Massenproduktion von Automobilstrukturgussteilen angewendet und bietet fortschrittliche Umformmethoden und -prozesse für die Anwendung hochwertiger Leichtlegierungsgussteile.
Das Schweizer Unternehmen Bühler hat ein Zweikreis-Vakuumsystem zur Herstellung von Strukturgussteilen entwickelt. Diese Produktionstechnologie wird strukturelle Produktionstechnologie genannt. Durch den Einsatz struktureller Produktionstechnologie kann die Geschwindigkeit des Vakuumierens erhöht werden, wodurch stabile Produktionsbedingungen erzielt und die Qualität der Druckgussteile deutlich verbessert werden. Wie in Abb. 5 dargestellt, ist der Luftabsauganschluss eines Kreislaufs im Zweikreis-Vakuumsystem am oberen Ende der Druckkammer angeordnet und dient hauptsächlich zum Absaugen von Luft in der Druckkammer. Es beginnt, wenn sich der Einspritzkolben nach vorne bewegt, um die Ausgießöffnung abzudichten, und schließt, wenn der Kolben dabei ist, die Ansaugöffnung abzudichten. Die andere Schaltungseinstellung ist die gleiche wie beim herkömmlichen Vakuumverfahren und wird hauptsächlich zum Absaugen von Luft aus dem Hohlraum verwendet. Derzeit wird die Technologie erfolgreich bei der Herstellung von integrierten Stoßdämpfungstürmen, Türinnenverkleidungen und Karosserieschienen aus Aluminiumlegierungen für Personenkraftwagen eingesetzt.
Präzisionsgussumformtechnik für Gussteile
Der allgemein als Präzisionsguss von Automobilgussteilen bezeichnete Begriff bezieht sich hauptsächlich auf die Schaumverlust- und Feingusstechnologie. Mit der Entwicklung der Gussumformtechnologie für Automobile bezieht sich die Gusspräzisionsumformung auf eine Art Gussumformverfahren. Mit diesem Umformverfahren hergestellte Gussteile können spanlos oder spanlos direkt verwendet werden. Mit den steigenden Anforderungen an die Maßgenauigkeit von Gussteilen hat sich die Präzisionsgusstechnologie in den letzten Jahren rasant weiterentwickelt und eine Reihe neuer Gussverfahren wie Präzisionssandguss, Schaumverlustguss, kontrollierter Druckguss und Druckguss entstanden. Das Cosworth-Gießverfahren ist ein im Vereinigten Königreich entwickeltes Verfahren, das eine Zirkoniumsandkernanordnung und eine elektromagnetische Pumpe zur Steuerung des Gießens verwendet. Es wurde erfolgreich bei der Massenproduktion von Zylinderblöcken aus Aluminiumlegierungen eingesetzt und es sind viele Verfahrensvarianten entstanden, beispielsweise die Verwendung von Niederdruckgießen anstelle elektromagnetischer Verfahren wie Pumpengießen. Mit dieser Art von Gussverfahren können Zylinder aus Aluminiumlegierung mit einer Wandstärke von 3.5 bis 4.0 mm hergestellt werden, was dem derzeit repräsentativen Verfahren des Präzisionssandgusses entspricht.
Das Schaumgussverfahren wurde 1965 erfunden. Die wichtigsten Gussteile für die Automobilindustrie sind Zylinderblöcke, Zylinderköpfe, Ansaug- und Auspuffrohre und andere Produkte, die mittlerweile in großem Maßstab hergestellt werden. Seit der Einführung der Lost-Foam-Gießtechnologie in den 1990er Jahren des 20. Jahrhunderts hat mein Land begonnen, Gestalt anzunehmen und wurde vom Staat als die am weitesten verbreitete Hoch- und Neutechnologie zur Umgestaltung der traditionellen Gießereiindustrie gefördert. Derzeit gibt es in meinem Land drei Feingussverfahren: Natriumsilikatschale, Verbundschale und Kieselsolschale. Unter anderem kann die Oberflächenqualität des Gussstücks, das bei der Herstellung von Silica-Sol-Hüllen für Automobilprodukte verwendet wird, Ra 1.6 μm erreichen, und die Maßgenauigkeit kann CT4 erreichen. Sorte, die minimale Wandstärke kann 0.5 bis 1.5 mm betragen. Dongfeng Motor Precision Casting Co., Ltd. nutzt das Verfahren zur Schalenherstellung aus Silica-Sol- und Wasserglas-Verbundwerkstoffen, um komplexe Gussteile mit integrierter Struktur herzustellen, was die Produktionskosten erheblich senkt. Der Entwicklungstrend des Feinguss-Technologie-Formverfahrens besteht darin, dass die Gussteile dem Endprodukt immer näher kommen und die Komplexität und Qualität der Produkte immer höher wird. Die Anwendung von CAD, CAM und CAE ist zur Haupttechnologie der Produktentwicklung geworden, und es zeichnet sich eine professionelle Zusammenarbeit ab.
Vakuumguss, sauerstoffgefüllter Druckguss, halbfester metallrheologischer oder thixotroper Druckguss und andere auf der Grundlage des Hochdruckgussverfahrens entwickelte Prozessmethoden sollen Gussfehler beseitigen, die innere Qualität verbessern und den Anwendungsbereich von Druckgussteilen erweitern . Während des Squeeze-Casting-Verfahrens wird die Schmelze unter Druck gefüllt und erstarrt, was die Vorteile von Glätte, keinem Metallspritzer, weniger Metallflüssigkeitsoxidationsverlust, Energieeinsparung, sicherem Betrieb und der Reduzierung von Gusslöchern und anderen Defekten mit sich bringt. Es wird in Hilfsrahmen aus Aluminiumlegierungen usw. verwendet. Die Entwicklung und Anwendung von Gussteilen aus Hochleistungsaluminiumlegierungen ist weit verbreitet.
Das kontinuierliche Wachstum der Automobilproduktion erfordert dringend die Entwicklung der Gussproduktion in Richtung hoher Qualität, hervorragender Leistung, endkonturnaher Form, Vielfalt, geringer Verbrauch und niedriger Kosten. Denn etwa 15 bis 20 % der Teile eines kompletten Fahrzeugs sind Gussteile. Dies erfordert von der Gussindustrie, kontinuierlich verschiedene neue Technologien und neue Materialien anzuwenden, um das Gesamtniveau des Gusses zu verbessern. Die Präzisionsguss-Umformtechnologie von Gussteilen kann die oben genannten Anforderungen von Automobilgussteilen erfüllen und ihre Anwendung wird auch verschiedene Gussherstellungsverfahren von Automobilgussteilen abdecken.
Zusammenfassung
Um sich den immer strenger werdenden Anforderungen der Umweltschutzauflagen anzupassen, entwickeln sich Automobile in Richtung leichteres Gewicht. Pro 10 % weniger Fahrzeuggewicht können der Kraftstoffverbrauch um 5.5 % gesenkt, der Kraftstoffverbrauch um 3 bis 5 % gesteigert und die Emissionen um etwa 10 % gesenkt werden. Die Anwendung von Aluminium-Magnesium- und anderen Nichteisenlegierungsgussteilen, die Entwicklung von großformatigen integrierten Gussteilen mit komplexer Struktur und die weit verbreitete Anwendung der Gusspräzisionsformungstechnologie sind die Hauptwege, um leichte Automobilgussteile zu erzielen. Daher ist es erforderlich, die Forschung und Entwicklung und Produktion von Automobilgussteilen mittels Hochleistungsgusswerkstoffen und umfangreicher Anwendung von Automatisierungsgeräten auf der Grundlage des umfassenden Einsatzes digitaler Technologie zu realisieren, um den Anforderungen der modernen Automobilindustrie gerecht zu werden.
Bitte bewahren Sie die Quelle und Adresse dieses Artikels für den Nachdruck auf: Der Entwicklungstrend von Automobilgussteilen und seiner Fertigungstechnologie
Mingh Druckgussunternehmen sind der Herstellung und Bereitstellung von hochwertigen und leistungsstarken Gussteilen gewidmet (das Angebot an Metalldruckgussteilen umfasst hauptsächlich) Dünnwandiger Druckguss,Heißkammerdruckguss,Kaltkammerdruckguss), Runder Service (Druckguss-Service,CNC-Bearbeitung,Formenbau,Oberflächenbehandlung). Alle kundenspezifischen Aluminium-Druckguss-, Magnesium- oder Zamak/Zink-Druckguss- und andere Gussanforderungen können uns gerne kontaktieren.
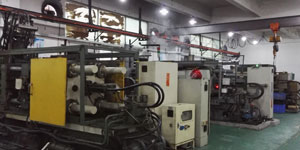
Unter der Kontrolle von ISO9001 und TS 16949 werden alle Prozesse durch Hunderte von fortschrittlichen Druckgussmaschinen, 5-Achsen-Maschinen und anderen Einrichtungen durchgeführt, von Blasgeräten bis hin zu Ultraschall-Waschmaschinen.Minghe verfügt nicht nur über fortschrittliche Ausrüstung, sondern auch über professionelle Team aus erfahrenen Ingenieuren, Bedienern und Inspektoren, um das Design des Kunden zu verwirklichen.
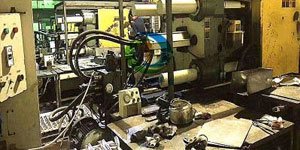
Auftragsfertigung von Druckgussteilen. Zu den Fähigkeiten gehören Kaltkammer-Aluminium-Druckgussteile von 0.15 lbs. bis 6 lbs., Schnellwechseleinrichtung und Bearbeitung. Mehrwertdienste umfassen Polieren, Vibrieren, Entgraten, Kugelstrahlen, Lackieren, Plattieren, Beschichten, Montage und Werkzeugbau. Zu den Materialien, mit denen gearbeitet wird, gehören Legierungen wie 360, 380, 383 und 413.
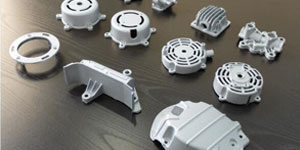
Unterstützung bei der Konstruktion von Zinkdruckguss / gleichzeitige Engineering-Dienstleistungen. Auftragsfertigung von Präzisions-Zink-Druckgussteilen. Es können Miniaturgussteile, Hochdruck-Kokillengussteile, Mehrschieber-Kokillengussteile, konventionelle Kokillengussteile, Einzel- und Einzeldruckgussteile sowie hohlraumdichte Gussteile hergestellt werden. Gussteile können in Längen und Breiten bis zu 24 Zoll in +/-0.0005 Zoll Toleranz hergestellt werden.
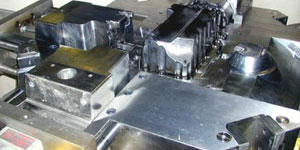
ISO 9001: 2015 zertifizierter Hersteller von Magnesium-Druckguss. Zu den Fähigkeiten gehören Hochdruck-Magnesium-Druckguss bis zu 200 Tonnen Heißkammer und 3000 Tonnen Kaltkammer, Werkzeugdesign, Polieren, Formen, Bearbeitung, Pulver- und Flüssiglackierung, vollständige Qualitätssicherung mit KMG-Fähigkeiten , Montage, Verpackung & Lieferung.
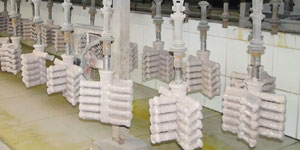
ITAF16949-zertifiziert. Zusätzlicher Casting-Service inklusive Feinguss,Sandguss,Schwerkraftguss, Verlorener Schaumguss,Schleuderguss,Vakuumgießen,Dauerguss,.Zu den Fähigkeiten gehören EDI, technische Unterstützung, Volumenmodellierung und Sekundärverarbeitung.
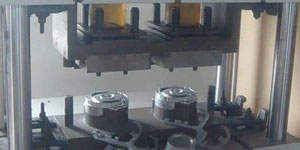
Gussindustrie Teile-Fallstudien für: Autos, Fahrräder, Flugzeuge, Musikinstrumente, Wasserfahrzeuge, optische Geräte, Sensoren, Modelle, elektronische Geräte, Gehäuse, Uhren, Maschinen, Motoren, Möbel, Schmuck, Vorrichtungen, Telekommunikation, Beleuchtung, medizinische Geräte, Fotogeräte, Roboter, Skulpturen, Tongeräte, Sportgeräte, Werkzeuge, Spielzeug und mehr.
Was können wir Ihnen als nächstes helfen?
∇ Zur Startseite gehen für Druckguss China
→Gussteile- Finden Sie heraus, was wir getan haben.
→Bewertete Tipps zu Druckgussdienste
By Minghe Druckgusshersteller |Kategorien: Hilfreiche Artikel |Werkstoff Stichworte: Aluminiumguss, Zinkguss, Magnesiumguss, Titanguss, Edelstahlguss, Messingguss,Bronzeguss,Casting-Video,Unternehmensgeschichte,Aluminiumdruckguss |Kommentare deaktiviert