Der Schmelzprozess von Schrott gehärtetem duktilem Eisen
Beim traditionellen Herstellungsverfahren von Sphäroguss werden im Allgemeinen etwa 10 % des Kohlenstoffschrotts für Zutaten verwendet. Dieser Artikel befasst sich nur mit einigen Aspekten, die im Produktionsprozess nach Erhöhung des Anteils an Kohlenstoffschrott bei der Herstellung von Sphäroguss im Induktionsofen besonders beachtet werden sollten. Entsprechend der Produktionspraxis legt der Autor seine eigenen Ansichten zur Referenz an Kollegen vor.
Die Wahl der Ladung
(1) Stahlschrott
Bei der Herstellung von Sphäroguss verwendeter Schrott sollte Kohlenstoffschrott sein. Es sollte keine Elemente enthalten, die die Graphitisierung behindern, wie z. B. Chrom. Es sollte keine antisphäroidisierenden Legierungselemente enthalten. Die Stahlschrottklumpen sollten zu etwa 30% in Form von dicken Flocken vorliegen, die flach in den Ofen gelegt werden können.
(2) Aufkohler
- ① Hochwertige Cola. Der Schwefelgehalt sollte niedrig sein, die Klumpigkeit beträgt 60-80 mm und es hat eine hohe Festigkeit. Es kann nach dem Verbrennen nicht zerdrückt werden.
- ②Verbrauchter Elektrodenblock. Es ist am besten, eine bestimmte Länge zu haben, um das Schneiden in das geschmolzene Eisen zu erleichtern.
(3) Gusseisen
Es wird hauptsächlich verwendet, um den Kohlenstoffgehalt von geschmolzenem Eisen einzustellen. Ich hoffe, kohlenstoffarmes, schwefelarmes Roheisen mit wC>4% zu verwenden. Der Siliziumgehalt im Roheisen ist entsprechend höher und die Herstellung von Sphäroguss kann weniger Ferrosilizium sein.
(4) Sphäroidisieren
Sphäroidisierungsmittel und Impfmittel werden nach traditionellen Techniken verwendet und gemäß den tatsächlichen Bedingungen jeder Fabrik bestimmt.
Stint
Schmelzprozess: Koksblock + Stahlschrott → Elektrodenblock → Temperaturerhöhung → Koksblock und Elektrodenblock herausziehen → Kohlenstoffgehalt entnehmen und analysieren → Roheisen → Material zurückgeben → Si, Mn entnehmen und analysieren → Temperaturerhöhung → Ferromangan + Ferrosilizium → Entladung →Inokulation + Sphäroidisierung → Gießen.
Die Vorsichtsmaßnahmen während des Schmelzprozesses sind wie folgt:
- Der Koksblock wird am Boden des Ofens installiert, um eine längere Einweichzeit des Koksblocks in der Eisenschmelze zu erreichen. Die Koksblockmenge beträgt etwa 5 % des Schrotts. Etwa 50 % des Schrotts sind geschmolzen und der Koks sollte mit dickem Flockenschrott bedeckt sein. Es ist auch möglich, anstelle von Koks, der am Boden des Ofens als Aufkohler mit einem niedrigeren Schwefelgehalt installiert wird, Altelektrodenblöcke von 60-80 mm zu verwenden, was für die Gewinnung von hochwertigem Sphäroguss vorteilhafter ist.
- Der Anteil des verwendeten Stahlschrotts wird hauptsächlich durch die Effizienz der Kohlenstofferhöhung bestimmt. Für Hersteller, die dieses Verfahren zur Herstellung von Sphäroguss verwenden, sind etwa 30 % besser. Erhöhen Sie nach der Verbesserung der Effizienz der Kohlenstoffsteigerung schrittweise den Anteil an Stahlschrott. Eine übermäßige Verwendung von Stahlschrott, wenn die Effizienz der Kohlenstofferhöhung nicht hoch ist, beeinflusst das Kohlenstoff-Silizium-Äquivalent des Endprodukts.
- Nachdem der Stahlschrott geschmolzen ist, setzen Sie den Elektrodenstab ein, um die Temperatur im Ofen entsprechend zu erhöhen und die Kohlenstoffeffizienz zu erhöhen. Allerdings ist die Ofentemperatur zu hoch, was den Stromverbrauch erhöht und auch der Ofenauskleidung schadet.
- Nachdem der Kohlenstoffgehalt als hoch genug eingeschätzt wurde, nehmen Sie den Koksblock und den Elektrodenstab heraus und nehmen Sie eine Probe und analysieren Sie den Kohlenstoffgehalt.
- Berechnen Sie anhand der Analyseergebnisse die Menge an zugegebenem Roheisen und die Menge an recyceltem Sphäroguss.
- Bestimmen Sie, ob die Gesamtmenge an geschmolzenem Eisen mit dem aufgearbeiteten Material basierend auf der Schätzung des Siliziumgehalts aufgefüllt werden kann.
- Nachdem das Wiedererwärmungsmaterial geschmolzen ist, nehmen Sie eine Probe und analysieren Sie den Gehalt an Si, Mn und anderen Legierungselementen.
- Erhöhen Sie die Temperatur des geschmolzenen Eisens ordnungsgemäß, ergänzen Sie die Legierungselemente gemäß den Analyseergebnissen und fügen Sie Ferrosilizium hinzu, bevor der Ofen die Ofentemperatur erreicht.
- Das Ferrosilicium wird zu einem geschmolzenen Zustand geschmolzen und wird sofort aus dem Ofen freigegeben.
- Sphäroidisieren, Animpfen und Gießen werden wie üblich durchgeführt.
Berechnung der Zusammensetzungsanpassung
Wie wir alle wissen, hängen die mechanischen Eigenschaften von Sphäroguss hauptsächlich von der chemischen Zusammensetzung, der Abkühlgeschwindigkeit (Sphäroguss im Gusszustand) und dem Wärmebehandlungsverfahren ab. Die chemische Zusammensetzung ist die innere Ursache, die Wurzel und die Variable, fast jeder Ofen ist anders. Daher ist es notwendig, die Erkennung chemischer Komponenten zu verstärken und sorgfältige Anpassungen vorzunehmen, und es ist nicht angebracht, eine "Produktion mit festem Verhältnis" zu verwenden. Bei der chemischen Zusammensetzung ist das Kohlenstoffäquivalent besonders wichtig. Insbesondere Sphäroguss, der unter Verwendung von Stahlschrott als Hauptcharge hergestellt wird, da die Effizienz der Kohlenstofferhöhung schwer zu kontrollieren ist und das Kohlenstoffäquivalent stark schwankt, sollte der Einstellung des Kohlenstoffäquivalents besondere Aufmerksamkeit geschenkt werden.
- Berechnen Sie die Menge des hinzugefügten Roheisens. Berechnen Sie die zugegebene Roheisenmenge anhand der Analyse des Kohlenstoffgehalts. Tatsächlich muss das Kohlenstoffäquivalent von Sphäroguss so eingestellt werden, dass das Kohlenstoffäquivalent der sowohl aus Roheisen als auch aus Stahlschrott gebildeten Schmelze das für Sphäroguss erforderliche Kohlenstoffäquivalent erreicht. Die zugegebene Roheisenmenge = die Menge an Schrott hinzugefügt × (erforderlicher Kohlenstoffgehalt von Sphäroguss – Analyse des Kohlenstoffgehalts) / (Kohlenstoffgehalt von Roheisen – erforderlicher Kohlenstoffgehalt von Sphäroguss)
- Berechnung der Zugabemenge von recyceltem Sphäroguss Das Kohlenstoffäquivalent von recyceltem Sphäroguss ist grundsätzlich normal und die Zugabemenge ist nicht groß. Daher wird nach der Zugabe des wiedererhitzten Eisens der Kohlenstoffgehalt des geschmolzenen Eisens im gesamten Ofen bestimmt Eisen hinzugefügt
- Schätzung des Siliziumgehalts Die Berechnungsformel lautet wie folgt: Siliziumgehalt ≈ ((Stahlschrott + Roheisen + Sphäroguss-Zugabemenge) × Siliziumgehalt / Gesamtbeschickung] × 100 % ≤ zulässiger Siliziumgehalt der ursprünglichen EisenschmelzeWenn das geschätzte Silizium Gehalt zu hoch ist, geben Sie eine geringe Menge an recyceltem Sphäroguss hinzu und verwenden Sie die gleiche Menge Roheisen und Schrott im Verhältnis 9:1 für die Gesamtcharge.
- Berechnung der Ferrosilicium-Zugabe Die Berechnungsformel lautet wie folgt: Die Menge des zugesetzten Ferrosiliciums = [Gesamtladungsmenge × (erforderlicher Siliciumgehalt des duktilen Eisens erhöhter Siliciumgehalt durch Impfung-erhöhter Siliciumgehalt durch Sphäroidisierungsanalyse des Siliciumgehalts)] / Siliziumgehalt von Ferrosilizium
- Die Menge an hinzugefügtem Mangan und anderen Legierungselementen wird wie folgt berechnet: Die Menge an hinzugefügtem Legierungseisen = die Gesamtmenge der Ladung × (der erforderliche Legierungsgehalt des duktilen Eisens - Analysegehalt) / Legierungselementgehalt im LegierungseisenDer Brennverlust ist nicht in den obigen Berechnungen enthalten.
Dies liegt daran, dass Sphäroguss im Induktionsofen geschmolzen wird und die Elemente nicht viel verbrannt werden und das Eisen auch zu einem gewissen Grad verbrannt wird. Wenn Sie auf besondere Umstände stoßen, sollten Sie auf das Brennen achten.
Anwendungsbeispiel für die Zusammensetzungsanpassung:
- Bei Verwendung eines 1-t-Induktions-Elektroofens zur Herstellung von perlitischem Sphäroguss QT800-2 beträgt das Gussgewicht 1000 kg.
- "Die chemische Zusammensetzung der Kontrollsubstanz ist: wC = 3.5 %, wSi = 2.5 %, wMn = 0.5 %, wP < 0.07 %, wS < 0.02 %, wMg = 0.03 % 0.06 %, wRE = 0.02 % 0.04 %.
- Nach der Aufkohlung beträgt der Kohlenstoffgehalt des „Schrotts der Schmelze“ im Ofen 2.5 %.
- Die hinzugefügte Menge an Roheisen = 300 × (3.5%-2.5%) / (4%-3.5%) = 600 (kg)
- Die im Ofen verwendete Menge an Sphäroguss = 1000-300-600=100 (kg)
- Geschätzter Siliziumgehalt = (300×0.3%+600×1.8%+100×2.5%)×100%=1.42%
- Wenn der Siliziumgehalt des Nodulizers 0.6% beträgt und der Siliziumgehalt des Impfmittels 0.4% beträgt, sollte der Siliziumgehalt der ursprünglichen Eisenschmelze 1.5% betragen, was höher ist als der geschätzte Siliziumgehalt. Dabei kann Z18-Guss zur Einstellung des Kohlenstoffäquivalents und das nachgebrannte Sphäroguss verwendet werden, um die Gesamtchargenmenge zu kompensieren.
- Der Siliziumgehalt beträgt 1.38% und der Mangangehalt 0.15%, bevor der Ofen freigegeben wird.
- Ferrosilizium-Zusatzmenge = [1000 (2.5%-0.6%-0.4%-1.38%)] / 75% = 1.6kg
- Ferromangan-Zugabemenge = [1000 (0.5%-0.15%)] / 65% = 5.4kg
4. Abschließende Bemerkungen
Bei der Herstellung von Induktions-Elektroöfen verwenden wir Stahlschrott zur Herstellung von QT800-2, die Festigkeit beträgt 800~1000MPa und die Dehnung beträgt mehr als 4%.
Derzeit gibt es viel Stahlschrott auf dem Markt, Roheisen ist teuer und hochwertiges Roheisen noch knapper. Daher schlagen wir vor, dass Hersteller mit Aufgaben in der Herstellung von Sphäroguss auf die oben genannte Annahme und „Ersatz von Eisen durch Stahl“ zurückgreifen können, um Sphäroguss herzustellen.
Bitte bewahren Sie die Quelle und Adresse dieses Artikels für den Nachdruck auf:Der Schmelzprozess von Schrott gehärtetem duktilem Eisen
Mingh Druckgussunternehmen sind der Herstellung und Bereitstellung von hochwertigen und leistungsstarken Gussteilen gewidmet (das Angebot an Metalldruckgussteilen umfasst hauptsächlich) Dünnwandiger Druckguss,Heißkammerdruckguss,Kaltkammerdruckguss), Runder Service (Druckguss-Service,CNC-Bearbeitung,Formenbau,Oberflächenbehandlung). Alle kundenspezifischen Aluminium-Druckguss-, Magnesium- oder Zamak/Zink-Druckguss- und andere Gussanforderungen können uns gerne kontaktieren.
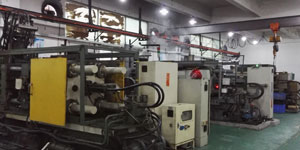
Unter der Kontrolle von ISO9001 und TS 16949 werden alle Prozesse durch Hunderte von fortschrittlichen Druckgussmaschinen, 5-Achsen-Maschinen und anderen Einrichtungen durchgeführt, von Blasgeräten bis hin zu Ultraschall-Waschmaschinen.Minghe verfügt nicht nur über fortschrittliche Ausrüstung, sondern auch über professionelle Team aus erfahrenen Ingenieuren, Bedienern und Inspektoren, um das Design des Kunden zu verwirklichen.
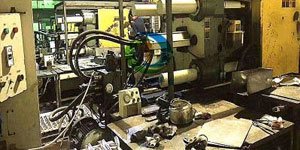
Auftragsfertigung von Druckgussteilen. Zu den Fähigkeiten gehören Kaltkammer-Aluminium-Druckgussteile von 0.15 lbs. bis 6 lbs., Schnellwechseleinrichtung und Bearbeitung. Mehrwertdienste umfassen Polieren, Vibrieren, Entgraten, Kugelstrahlen, Lackieren, Plattieren, Beschichten, Montage und Werkzeugbau. Zu den Materialien, mit denen gearbeitet wird, gehören Legierungen wie 360, 380, 383 und 413.
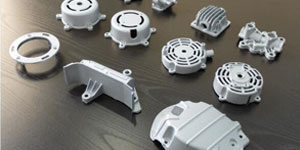
Unterstützung bei der Konstruktion von Zinkdruckguss / gleichzeitige Engineering-Dienstleistungen. Auftragsfertigung von Präzisions-Zink-Druckgussteilen. Es können Miniaturgussteile, Hochdruck-Kokillengussteile, Mehrschieber-Kokillengussteile, konventionelle Kokillengussteile, Einzel- und Einzeldruckgussteile sowie hohlraumdichte Gussteile hergestellt werden. Gussteile können in Längen und Breiten bis zu 24 Zoll in +/-0.0005 Zoll Toleranz hergestellt werden.
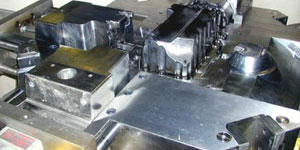
ISO 9001: 2015 zertifizierter Hersteller von Magnesium-Druckguss. Zu den Fähigkeiten gehören Hochdruck-Magnesium-Druckguss bis zu 200 Tonnen Heißkammer und 3000 Tonnen Kaltkammer, Werkzeugdesign, Polieren, Formen, Bearbeitung, Pulver- und Flüssiglackierung, vollständige Qualitätssicherung mit KMG-Fähigkeiten , Montage, Verpackung & Lieferung.
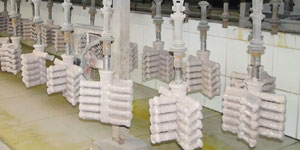
ITAF16949-zertifiziert. Zusätzlicher Casting-Service inklusive Feinguss,Sandguss,Schwerkraftguss, Verlorener Schaumguss,Schleuderguss,Vakuumgießen,Dauerguss,.Zu den Fähigkeiten gehören EDI, technische Unterstützung, Volumenmodellierung und Sekundärverarbeitung.
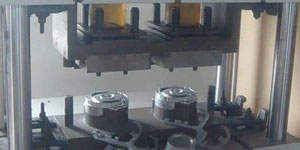
Gussindustrie Teile-Fallstudien für: Autos, Fahrräder, Flugzeuge, Musikinstrumente, Wasserfahrzeuge, optische Geräte, Sensoren, Modelle, elektronische Geräte, Gehäuse, Uhren, Maschinen, Motoren, Möbel, Schmuck, Vorrichtungen, Telekommunikation, Beleuchtung, medizinische Geräte, Fotogeräte, Roboter, Skulpturen, Tongeräte, Sportgeräte, Werkzeuge, Spielzeug und mehr.
Was können wir Ihnen als nächstes helfen?
∇ Zur Startseite gehen für Druckguss China
→Gussteile- Finden Sie heraus, was wir getan haben.
→Bewertete Tipps zu Druckgussdienste
By Minghe Druckgusshersteller |Kategorien: Hilfreiche Artikel |Werkstoff Stichworte: Aluminiumguss, Zinkguss, Magnesiumguss, Titanguss, Edelstahlguss, Messingguss,Bronzeguss,Casting-Video,Unternehmensgeschichte,Aluminiumdruckguss |Kommentare deaktiviert