Die Prozesskontrolle der Vermicular-Eisen-Produktion
Im Vergleich zu Grauguss wird die Zugfestigkeit von Vermiculareisen um mindestens 70 % erhöht, der E-Modul um 35 % erhöht und die Dauerfestigkeit nahezu verdoppelt. Im Vergleich zu einer Aluminiumlegierung sind die Festigkeit und Steifigkeit von Vermiculareisen doppelt so hoch und die Dauerfestigkeit ist doppelt so hoch. Diese Eigenschaften von vermicularem Eisen bieten dem Motor die Möglichkeit, das Leistungs-/Gewichtsverhältnis zu verbessern und den Zylinderdruck zu erhöhen. Die Erhöhung des Zylinderdrucks ist der Schlüssel zur optimalen Leistung des direkteinspritzenden Dieselmotors der nächsten Generation. Um der weit verbreiteten Anwendung von Vermiculareisen gerecht zu werden, bereitet die Gießereiindustrie derzeit aktiv neue Prozesse vor, investiert massiv und baut neue Prozesse auf, um die Produktion von Vermiculareisen stabil und zuverlässig zu gestalten.
Bei Vermicular-Eisen-Motoren vom Prototypen bis zur Massenproduktion ist das Qualitätsrisiko der entscheidende Faktor. Bei hochwertigem Vermiculareisen ist die stabile Zone sehr klein, nur im Bereich von 0.008% Magnesiumgehalt. Eine Spurenmenge, wie beispielsweise ein Verlust von 0.001 % Magnesium, führt zur Bildung von Graphitflocken, wodurch die mechanischen Eigenschaften um 25 bis 40 % sinken. Dieser Artikel beschreibt ein Prozessleitsystem basierend auf thermischen Analysemethoden. Das System misst den Magnesiumverlust und passt den Zustand der Eisenschmelze online an, um die Bildung von Lamellengraphit zu verhindern. Diese Online-Kontrollmethode der Messung und Justierung reduziert die Volatilität bei der Herstellung von Vermiculareisen auf den niedrigsten Punkt und eliminiert grundsätzlich das Qualitätsrisiko, das durch die Herstellung von Vermiculareisen entsteht.
Die Nachfrage nach hoher Leistung, hohem Drehmoment, niedrigen Abgasemissionen und reduziertem Kraftstoffverbrauch wächst weiter. Dies zwingt die Konstrukteure von Hochleistungsdieselmotoren dazu, den Zündspitzendruck zu erhöhen, was die thermische Belastung und die mechanische Belastung des Motors stark erhöht. Gleichzeitig steigen die thermische Belastung und die mechanische Belastung, so dass die derzeit eingesetzten konventionellen Grauguss- und Legierungsgussmotoren (CrMo) die Einsatzobergrenze erreicht oder überschritten haben. Motorenhersteller benötigen Materialien mit höherer Festigkeit und besserer Hitzebeständigkeit.
Vermicular Eisen hat sich schnell zum Material der Wahl für Menschen entwickelt. Es verbessert die Zuverlässigkeit von Zylinderblock, Zylinderkopf und Zylinderlaufbuchse der neuen Lkw-Motorengeneration erheblich. Um die beste Kombination verschiedener Eigenschaften (wie Gusseigenschaften, Zerspanungseigenschaften, Wärmeleitfähigkeit und mechanische Eigenschaften) zu erreichen, müssen diese Teile mit einer Sphäroidisierungsrate von 0% bis 20% (Kriechrate von 80% bis 100% ) Aus vermicularem Eisen. Wenn die Sphäroidisierungsrate 20 % überschreitet, verursacht dies eine Reihe von ungünstigen Faktoren. Beispielsweise ist die Schwindung zu groß und Teile mit komplexen Formen wie Zylinderköpfe sind besonders schwindungsanfällig. Ein weiteres Beispiel ist die Reduzierung der Werkzeugstandzeiten durch übermäßigen Verschleiß während der Bearbeitung. Es gibt auch eine signifikante Abnahme der Wärmeleitfähigkeit, was zu thermischer Belastung usw. führt. Am anderen Ende des Vermiculareisens führt das Auftreten von Lamellengraphit zu einem linearen Rückgang der mechanischen Eigenschaften, sodass der Motor die neuen Anforderungen nicht mehr erfüllen kann. Zusammenfassend lässt sich sagen, dass die Sphäroidisierungsrate von hochfestem Vermiculareisen zwischen 0 % und 20 % liegen muss, um die Anforderungen der neuen Generation von Lkw-Motoren zu erfüllen (d. h. die Kriechrate liegt über 80 %, ohne Flocken).
Ob eine Kontrolle des Produktionsprozesses verwendet wird oder nicht, hängt von der Jahresproduktion des Produkts, der Komplexität des Produkts und dem zulässigen Bereich von Änderungen in der metallografischen Struktur ab. Wie in Abbildung 1 gezeigt, können relativ einfache Kleinserienteile, wie Kokillen, im Allgemeinen mit herkömmlichen Gießverfahren hergestellt werden. Eine Prozesskontrolle ist in der Regel nicht erforderlich und wirtschaftlich nicht wirtschaftlich. Wenn die jährliche Produktion von Komponenten wie Auspuffrohren, Kurbelhülsen und Halterungen steigt, sollte es sinnvoll sein, eine Prozesssteuerung einzuführen. Obwohl diese Art von Produkt eine große Jahresproduktion hat, ist die jährliche Tonnage an Gussteilen nicht hoch. Die Anforderungen an die metallographische Struktur sind nicht sehr streng, so dass die Sphäroidisierungsrate bis zu 50% betragen kann. Außerdem kann aufgrund des geringen Bearbeitungsaufwands solcher Teile durch die Erhöhung des Titangehalts, der bei der Produktion hinzugefügt werden kann, der kontrollierbare Bereich erweitert werden. Für diese Art von Produkten sind herkömmliche Gießverfahren und eine strenge Ausbildung in der Regel für die Herstellung von Vermiculareisen geeignet. Aber aus Sicht der Qualitätskontrolle sollte die Prozesskontrolle sicherer sein. Ebenso gewährleistet die Prozesskontrolle auch die Produktion von großen Schiffsmotorblöcken und Zylinderköpfen. Obwohl die große Größe und die geringe Produktionsmenge der Herstellung von Produkten förderlich sind, reichen die wirtschaftlichen Verluste, die durch die Produkte verursacht werden, die den Standard überschreiten, aus, um ein Prozessleitsystem hinzuzufügen.
Die am stärksten prozesskontrollierten Produkte sind Zylinderblöcke, Zylinderköpfe und Bremsscheiben für Automobilmotoren mit großer Jahresleistung, hoher Komplexität und hohen technischen Anforderungen. Das jährliche Produktionsvolumen und die jährliche Tonnage dieser Produkte sind sehr hoch. Sie haben eine komplexe Größe, stellen hohe Anforderungen an die metallographische Struktur und neigen dazu, Schrumpfungshohlräume zu erzeugen. Diese Produkte dürfen keine Qualitätsrisiken aufweisen, da sonst der Verlust sehr schwerwiegend ist.
Die strengen Anforderungen an die Leistungsfähigkeit von Motorblock, Zylinderkopf und Zylindersitz haben die Grundlage für die Herstellung von Produktspezifikationen gelegt. Um die beste Gesamtleistung von Gießbarkeit, Bearbeitbarkeit und mechanischen Eigenschaften zu erzielen, sollte die Sphäroidisierungsrate in allen Schlüsselteilen des Bauteils im Bereich von 0 % bis 20 % liegen. Noch wichtiger ist, dass Lamellengraphit unbedingt vermieden werden muss, um Schäden an Teilen durch lokale Schwächen zu vermeiden. Um eine gute mechanische Additivität zu erreichen, müssen freie Karbide auf ein Minimum reduziert werden. Daher sollte Titan niemals hinzugefügt werden. Schließlich benötigt die Gießerei aus produktionstechnischer Sicht einen stabilen und zuverlässigen Prozess, um die niedrigste Ausschussrate aufgrund der metallografischen Struktur zu gewährleisten. Hersteller in der Automobilindustrie benötigen eine Qualitätssicherung und 100 % der Gussteile müssen metallografischen Anforderungen genügen. Die zuverlässige Produktion von Zylinderblöcken, Zylinderköpfen und Zylindersitzen in großem Maßstab erfordert eine genaue Analyse und Online-Einstellung der Eisenschmelze, um Schwankungen im Prozess vor dem Gießen zu eliminieren.
Vermikulare Eisenstabilität
Der Grund, warum Kompakteisen nicht in großen Mengen zur Herstellung komplexer Teile (wie Motorblöcke) verwendet wird, liegt darin, dass die stabile Fläche von Kompakteisen zu klein ist, um sicherzustellen, dass in der Produktion kein Risiko besteht. Im Allgemeinen umfasst diese stabile Zone nur die Fläche von 0.008% Magnesium, wie in Abbildung 2 gezeigt. Die Größe und Position der Plattform in der stabilen Zone variieren je nach Produkt. Tatsächlich ist der verfügbare Magnesiumbereich kleiner als dieser. Denn alle 5 Minuten verbrennt aktives Magnesium 0.001%. Der Anfangsgießpunkt der Eisenschmelze muss weit genug vom scharfen Wendepunkt des Presslings zum Grauguss entfernt sein, damit im fertigen Gussteil kein Lamellengraphit auftritt. Wenn dem geschmolzenen Eisen Magnesium zugesetzt wird, erscheint nach etwa 15 Minuten Flockengraphit.
Der Startpunkt sollte nicht zu nah an der rechten Seite der stabilen Plattform liegen (hoher Magnesiumgehalt), da sich sonst im dünneren Teil und im schnell abkühlenden Teil viel Kugelgraphit bildet.
Neben der kleinen verfügbaren Bahnsteigfläche ist die Bahnsteigfläche ständig in Bewegung. Wenn der Gehalt an aktivem Sauerstoff und Schwefel hoch ist, verbrauchen sie mehr aktives Magnesium und die gesamte Plattform bewegt sich nach rechts (hoher Magnesiumgehalt). Umgekehrt bewegt sich die Plattform bei niedrigem Aktivsauerstoff- und Schwefelgehalt nach links (geringer Magnesiumgehalt). Veränderungen in der Zusammensetzung von Rohstoffen, Reinheit, Oxidationsgrad und Feuchtigkeit usw. machen es dem Menschen unmöglich, vermiculares Eisen mit einem festgelegten Bereich der chemischen Zusammensetzung zu kontrollieren.
Obwohl bei der Umwandlung von Vermiculareisen zu Grauguss das aktive Magnesium nur um 0.001 % reduziert werden muss, wird durch das Verbrennen von Magnesium nicht das gesamte Teil zu Lamellengraphit. Wenn das aktive Magnesium nicht ausreicht, bildet Graphit zunächst Flocken und dehnt sich beim Erstarren nach außen aus, und Magnesium sackt ab und konzentriert sich am vorderen Ende der Fest-Flüssig-Grenzfläche. Wenn die Anfangsmenge an aktivem Magnesium angemessen ist, bildet sich Vermiculargraphit an der Grenze des Eutektikums, wie in Abbildung 3 gezeigt. Flockengraphit erscheint zuerst als verstreute Graphitflockenflecken. Im Gegensatz zu allen üblichen Graphitflocken sind diese isolierten Graphitflockenflecken mit Ultraschall schwer zu erkennen. Die Wahrscheinlichkeit, dass sie mit Ultraschall gescannt werden, ist nicht hoch.
Die Empfindlichkeit von Magnesium gegenüber vermicularem Eisen kann in Abbildung 4 gezeigt werden: In einer Tonne Roheisenpfanne, nur 10 Gramm Magnesium hinzufügen, können die in der Φ25-Testprobe verteilten Graphitflockenflecken vollständig in Vermiculargraphit umgewandelt werden. Die Zugfestigkeit des Prüfstabs mit Flockengraphitflecken beträgt nur 300 MPa, während die Zugfestigkeit des gleichen Prüfstabs mit vollständigem Kriechen 450 MPa erreicht.
Das Impfmittel reagiert auch sehr empfindlich auf die stabile Plattform des vermicularen Eisens, wie in Abbildung 5 gezeigt: Die Zugabe von 80 Gramm Impfmittel zu einer Tonne geschmolzenem Eisen erhöht die Sphäroidisierungsrate im Φ25-Teststab von 3 % auf 21 %. Die Impfmenge ist hoch und es gibt viele Kristallkeime, was der Bildung von kugelförmigem Graphit förderlich ist. Dadurch wird die vermiculare Eisenplattform in Richtung hoher Sphäroidisierungsrate angehoben. Durch die geringe Impfrate bewegt sich die Plattform nach unten. Zahlreiche Faktoren, wie die Überhitzungstemperatur des geschmolzenen Eisens, die Haltezeit, die chemische Zusammensetzung der Rohstoffe, der Impfmitteltyp und die Impfmenge, beeinflussen die Position der Vermicular-Eisenplattform.
Die grundlegendste Anforderung an jede Prozessleittechnik ist die genaue Messung und Analyse des Zustands von geschmolzenem Eisen. Bei Vermiculareisen erfordert eine zuverlässige Produktionssteuerung die gleichzeitige Messung des kritischen Punktes des aktiven Magnesiums aus dem Kriech-Asche-Übergang, des Grades des anschließenden Magnesium-Ausbrennens und des Impfgrades.
Die thermische Analyseprobe von 200 Gramm wird durch Einführen der Xinte-Sonde in das geschmolzene Eisen nach der Sphäroidisierung und Inokulation erhalten. Während des dreisekündigen Eintauchvorgangs erreichen die Sondenwand und die Eisenschmelze einen thermischen Gleichgewichtszustand. Anders als der herkömmliche Thermoanalyse-Probenbecher garantiert dieser dünnwandige Probenehmer nicht nur jedes Mal das gleiche Probenvolumen, sondern vermeidet auch eine Oxidation des in den Probenbecher einfließenden geschmolzenen Eisens. Die Messung der Überhitzung ist genauer, da es bei der herkömmlichen thermischen Analyse kein Phänomen wie das Phänomen der heftigen Kondensation gibt.
Wie in Abbildung 6a gezeigt, besteht die Xinte-Sonde aus gepresstem, gestrecktem Stahlblech. Es ist im Grunde ein kugelförmiger Behälter. Die dünne Stahlwand, die das geschmolzene Eisen enthält, hat eine vakuumflaschenartige Isolationsschicht. Die Dicke der Isolationsschicht ist entsprechend der Höhenrichtung symmetrisch verdickt, um eine gleichmäßige Wärmeableitung und Kühlung an die Umgebung zu gewährleisten, und das darin enthaltene Eisen-zz-Wasser kommt der Erstarrung eines kugelförmigen Körpers nahe. Im Schutzrohr der Sonde befinden sich zwei Thermoelemente vom Typ N. Das Thermoelement kann nach jeder Messung herausgezogen und mehr als 100 Mal wiederholt verwendet werden. Eines der beiden Thermoelemente befindet sich am Boden des Behälters und das andere befindet sich im thermischen Zentrum des Behälters. Da der Behälter kugelförmig und frei aufgehängt ist (dies unterscheidet sich von dem herkömmlichen Thermoanalyse-Probenbecher, der auf einer wärmeabsorbierenden Halterung ruht), erzeugt das geschmolzene Eisen einen gleichmäßigen Wärmestrom im Behälter, wie in Fig. 6b gezeigt. Dieser Wärmestrom bewirkt einen ständigen Austausch der Eisenschmelze im Behälter und bildet eine Strömungstrennwand am Boden der Sonde.
Um den natürlichen Verlust von flüssigem Eisen beim Gießen nachzuahmen, befindet sich an der Sondenwand eine Beschichtung, die mit aktivem Magnesium reagiert. Das geschmolzene Eisen strömt, angetrieben durch den Wärmestrom, entlang der beschichteten Wand. Nach der Reaktion nimmt der Magnesiumgehalt des geschmolzenen Eisens ab und sammelt sich in der Kammer am Boden des Behälters. Direkt gesprochen: Das Thermoelement in der Mitte der Sonde misst die nicht umgesetzte Eisenschmelze, den Ausgangszustand des Gießens; das Thermoelement an der Unterseite misst den Zustand nach dem Gießende. Die Rezeptur der reaktiven Beschichtung ist sehr speziell. Es muss genau sichergestellt werden, dass die in der Kammer angesammelte Eisenschmelze um 0.003% weniger aktiv ist als die mittlere Eisenschmelze. Wenn daher der anfängliche Magnesiumgehalt zu nahe am Wendepunkt der Kriechasche liegt, erzeugt das geschmolzene Eisen in der Kammer Graueisen, das von dem Thermoelement in diesem Bereich gemessen wird. Auf diese Weise kann die Werkstatt zu Beginn des Gießens mehr Magnesium hinzufügen, um den unvermeidlichen Magnesiumverbrennungsverlust auszugleichen.
Zeigt das Thermoelement unten eine vermiculare Eisenkurve, ist der anfängliche Magnesiumgehalt so hoch, dass nach dem Gießen kein Lamellengraphit mehr vorhanden ist.
7 ist ein Querschnitts-Erosionsdiagramm der Xinte-Sonde nach der Probenmessung. In der Abbildung erkennt man deutlich den Trennbereich, den Hauptprobenbereich und das Thermoelement-Schutzrohr. Da das aktive Magnesium um 0.003% reduziert wird, bilden sich in der Trennzone D-förmige Graphit- und Ferritmatrix. Die Größe des Flake-Graphit-Bereichs am Boden spiegelt direkt den anfänglichen Magnesiumgehalt im Hauptprobenbereich wider. Die Größe dieser Zone lässt sich aus der am Boden abgegebenen Wärme berechnen. Der Varianzregressionskoeffizient zwischen der Wärmefreisetzung und der Größe der Trennwand überschreitet 0.9, was beweist, dass die Beziehung zwischen den beiden sehr eng ist. Die freigesetzte Wärme wird durch die zeitliche Integration der Abkühlkurve gewonnen. Diese Methode der gleichzeitigen Messung des Zustands des geschmolzenen Eisens beim Strom und am Ende des Gießens gewährleistet die Genauigkeit des Magnesiumgehalts vor dem Gießen.
Da Vermiculareisen sehr empfindlich gegenüber Sphäroidisierungs- und Impfmitteln ist, ist es für Gießereien unmöglich, die bei der Herstellung von Grauguss und Sphäroguss verwendeten übermäßigen Behandlungsmethoden anzuwenden. Wie in Abbildung 8 gezeigt, ist vermiculares Eisen aufgrund seiner Empfindlichkeit nur innerhalb eines quadratischen Fensters stabil, nicht nur im Bereich der Magnesiumplattform. Ein zuverlässiger Herstellungsprozess für vermiculares Eisen muss die Sphäroidisierung und Inokulation von Anfang bis Ende kontrollieren, um sicherzustellen, dass die metallographische Struktur das Ziel erfüllt.
Egal wie viel Aufwand betrieben wird, egal wie streng das Management ist, die Fluktuation der Eisenschmelze ist immer unvermeidlich. Ganz zu schweigen davon, wie genau die Leute über die Behandlung von geschmolzenem Eisen Bescheid wissen, einstufige Behandlungsmethoden wie die Sandwich-Methode können nicht garantieren, dass jede Behandlung innerhalb des engen Vermikulareisenfensters liegt. Zahlreiche Produktionsvariablen, wie Mischungsverhältnis, Ofentemperatur, Haltezeit, Vorwärmgrad der Schmelzpfanne, Abstichgeschwindigkeit, Abstichposition der Abstichschmelze (Innen- oder Außenmessung), Abstichgewicht, Legierungssackzustand, Sphäroidisiermittel der tatsächliche Magnesiumgehalt von (PeSiMg), die Legierungsanordnung jeder Schicht im Sandwich-Verfahren und die Bedeckung von Eisenschrott usw. beeinflussen die Absorption von Magnesium. Zusätzlich zu diesen Faktoren verändert auch der Gehalt an aktivem Sauerstoff und aktivem Schwefel die Größe und Position des vermicularen Eisenfensters. Änderungen der Verweilzeit des geschmolzenen Eisens in der Pfanne, der Transportzeit und der Gießzeit ändern alle die verfügbare Brennzeit.
Die unvorhersehbarsten Fluktuationsfaktoren sind jedoch Bedienerfehler oder Unterschiede zwischen verschiedenen Bedienern aufgrund unterschiedlicher Arbeitsgewohnheiten.
In der Massenproduktion im großen Maßstab ist die Messung der Erstarrungseigenschaften des geschmolzenen Eisens nach der Behandlung der einzige sichere Weg. Auf diese Weise wurden verschiedene Faktoren, die die Größe, Position und Legierungsaufnahme des vermicularen Eisenfensters beeinflussen, umfassend gemessen, analysiert und berücksichtigt. Dann kann die entsprechende Menge Magnesium und Impfmittel zugegeben werden. Jede Pfanne mit flüssigem Eisen wird gegossen, nachdem sie in einen idealen Zustand gebracht wurde. Diese zweistufige Mess- und Einstellprozesssteuerungsmethode minimiert Produktionsschwankungen und eliminiert das Risiko von Flockengraphit im Gussstück vollständig.
Prozesskontrolle der Vermiculareisenproduktion mit Hot Metal Pfanne
Wie in Abbildung 9 gezeigt, beginnt die Prozesskontrolle mit der thermischen Analyse des geschmolzenen Eisens nach der anfänglichen Sphäroidisierung und Impfbehandlung. Entsprechend dem Analyseergebnis zeigt das Drahtvorschubgerät automatisch die Länge des mit Magnesium und Impfmittel zu ergänzenden Drahtes an und wartet auf den Start durch den Bediener. Wenn die Beschickungslinie fertiggestellt ist, wird die Pfanne sofort an die Gießlinie geschickt. Der gesamte Mess- und Justiervorgang dauert etwa drei Minuten. In dieser Zeit kann die Werkstatt konventionelle Vorgussbehandlungen, wie zum Beispiel die Entschlackung, durchführen. Dies gewährleistet die Kontinuität der Gießlinie.
Aus betrieblicher Sicht enthält rohes geschmolzenes Eisen kein Magnesium und auch seine Inkubationsfähigkeit ist sehr begrenzt. Nach der Sphäroidisierung und Impfung fressen Magnesium und Impfmittel zuerst den aktiven Sauerstoff und Schwefel in der Eisenschmelze und "springen" dann die Eisenschmelze an eine bestimmte Position auf dem Brett. Im Beispiel in Abbildung 10 betragen der Magnesiumindex und der Impfindex von geschmolzenem Eisen 65 bzw. 45. Da sich die wesentlichen Änderungsparameter der Schattenbildung in der Eisenschmelze nach Messung und Behandlung zeigen, spiegeln die Ergebnisse der thermischen Analyse direkt den aktuellen Zustand der Eisenschmelze wider. Es bleibt nur noch die entsprechende Menge Magnesium und Impfmittel zuzugeben, um die Eisenschmelze von ihrer aktuellen Position auf den gewünschten Startpunkt zu heben. Im Beispiel in Abbildung 10 werden zuerst sieben Einheiten Magnesiumkabel und dann 23 Einheiten Impfkabel hinzugefügt. Das entsprechende Verhältnis zwischen Indexeinheit und Kabellänge wird produkt- und werkstattgerecht kalibriert und im Programm zusammengestellt. Basierend auf den Erfahrungen aus der Vergangenheit von fast 100,000 Vermiculareisengussteilen beträgt die durchschnittliche Menge an hinzugefügtem Magnesiumkabel 5 Meter pro Tonne. Es enthält 12 Gramm Magnesium pro Meter und bei einer Aufnahmerate von 50 % beträgt die zugesetzte Magnesiummenge pro Tonne geschmolzenem Eisen nur 30 Gramm. Da die Zugabemenge sehr gering ist und die wesentlichen Veränderungen bereits bei der Erstbehandlung eingetreten sind, ist die Einstellung sehr effektiv und zuverlässig. Nach der Einstellung ist keine thermische Analyse erforderlich.
Bei der Erstbehandlung sollte der Zustand nach der Behandlung niedriger sein als die anfängliche Gießposition, damit selbst wenn alle Faktoren, die für die Aufnahme von Magnesium und Impfmittel günstig sind, den optimalen Wert erreichen, das geschmolzene Eisen nur den anfänglichen Gießzustand erreicht . Außer zur Überbehandlung ist das geschmolzene Eisen nach der Behandlung nicht im Zustand von Graueisen und Weißeisen. Um den Gießprozess effizienter zu gestalten, werden der Magnesiumindex und der Impfindex jeder Pfanne mit flüssigem Eisen im Prozessblockdiagramm angezeigt. Entsprechend dem sich ändernden Trend des Blockdiagramms kann der Bediener die Menge an geschmolzenem Eisen anpassen, die der nächsten Pfanne zugeführt wird. Der Kohlenstoffäquivalentwert wird auch auf dem Bildschirm angezeigt. Diese Daten wurden aufbereitet und im Produktionsprotokoll nachvollziehbar und lückenlos gespeichert und erfüllen zudem die Anforderungen der Qualitätssicherung.
Obwohl eine thermische Analyse und anschließende Anpassungen die Produktion von Vermiculareisen sicherstellen können, wird empfohlen, Proben aus dem Angussbecher des endgültigen Gussstücks zur Analyse zu entnehmen. Im Vergleich zur herkömmlichen Qualitätsprüfung kann dieses thermische Analyseergebnis eine Online-Analyse bereitstellen und Gussteile bei Bedarf klassifizieren. Die Simulation des Magnesiumverlustes in der Sonde macht diese „zerstörungsfreie“ Prüftechnik effektiver als metallographische und Ultraschallverfahren. Da diese Methode eine größere Probengröße misst, erkennt sie auch, wie sich das geschmolzene Eisen in den nächsten 10-15 Minuten verfestigen wird.
Um zusammenzufassen
Die Wahl des Prozessleitsystems hängt vom Produkt und Gießverfahren ab. Beim Gießen komplexer Produkte wie Motordeckel und Zylinder aus Vermiculareisen muss das System gleichzeitig den Gehalt an Magnesium und Impfmittel kontrollieren, damit er vom Beginn bis zum Ende des Gießens innerhalb eines sehr engen Fensters liegt. Die Sphäroidisierungsrate muss zwischen 0% und 20% liegen (Kriechrate 80% bis 100%), um die beste Gießbarkeit, mechanische Additivität und andere umfassende Leistung und die beste Gebrauchsfunktion zu gewährleisten. Graphitflockenflecken müssen vollständig beseitigt werden, um lokale Defekte und Schwächen zu vermeiden.
Der Ausgangspunkt jedes Prozesssteuerungssystems ist die genaue und effektive Messung des Zustands des geschmolzenen Eisens. Zuverlässige großmaßstäbliche Vermicular-Eisenproduktion muss über praktikable Kontrollmethoden verfügen, um Prozessänderungen und menschliche Bedienungsfehler zu eliminieren. Der effektivste Weg, um Prozessänderungen zu eliminieren, ist die Durchführung einer thermischen Analyse von geschmolzenem Eisen nach der Sphäroidisierung und Inokulation. Gemäß den Ergebnissen der thermischen Analyse wird vor dem Gießen eine genaue Menge an Magnesium und Impfmittel hinzugefügt. Diese Online-Mess- und Einstellungsmethode gewährleistet die Stabilität der Gussproduktionslinie und eliminiert verschiedene Risiken, die durch die groß angelegte Herstellung von Vermiculareisen entstehen.
Bitte bewahren Sie die Quelle und Adresse dieses Artikels für den Nachdruck auf: Die Prozesskontrolle der Vermicular-Eisen-Produktion
Mingh Druckgussunternehmen sind der Herstellung und Bereitstellung von hochwertigen und leistungsstarken Gussteilen gewidmet (das Angebot an Metalldruckgussteilen umfasst hauptsächlich) Dünnwandiger Druckguss,Heißkammerdruckguss,Kaltkammerdruckguss), Runder Service (Druckguss-Service,CNC-Bearbeitung,Formenbau,Oberflächenbehandlung). Alle kundenspezifischen Aluminium-Druckguss-, Magnesium- oder Zamak/Zink-Druckguss- und andere Gussanforderungen können uns gerne kontaktieren.
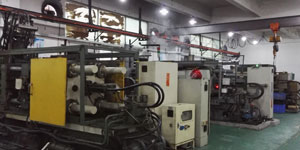
Unter der Kontrolle von ISO9001 und TS 16949 werden alle Prozesse durch Hunderte von fortschrittlichen Druckgussmaschinen, 5-Achsen-Maschinen und anderen Einrichtungen durchgeführt, von Blasgeräten bis hin zu Ultraschall-Waschmaschinen.Minghe verfügt nicht nur über fortschrittliche Ausrüstung, sondern auch über professionelle Team aus erfahrenen Ingenieuren, Bedienern und Inspektoren, um das Design des Kunden zu verwirklichen.
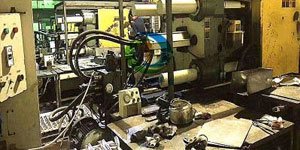
Auftragsfertigung von Druckgussteilen. Zu den Fähigkeiten gehören Kaltkammer-Aluminium-Druckgussteile von 0.15 lbs. bis 6 lbs., Schnellwechseleinrichtung und Bearbeitung. Mehrwertdienste umfassen Polieren, Vibrieren, Entgraten, Kugelstrahlen, Lackieren, Plattieren, Beschichten, Montage und Werkzeugbau. Zu den Materialien, mit denen gearbeitet wird, gehören Legierungen wie 360, 380, 383 und 413.
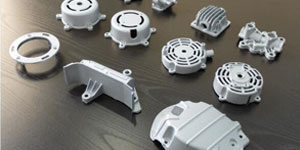
Unterstützung bei der Konstruktion von Zinkdruckguss / gleichzeitige Engineering-Dienstleistungen. Auftragsfertigung von Präzisions-Zink-Druckgussteilen. Es können Miniaturgussteile, Hochdruck-Kokillengussteile, Mehrschieber-Kokillengussteile, konventionelle Kokillengussteile, Einzel- und Einzeldruckgussteile sowie hohlraumdichte Gussteile hergestellt werden. Gussteile können in Längen und Breiten bis zu 24 Zoll in +/-0.0005 Zoll Toleranz hergestellt werden.
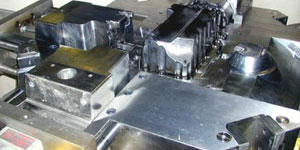
ISO 9001: 2015 zertifizierter Hersteller von Magnesium-Druckguss. Zu den Fähigkeiten gehören Hochdruck-Magnesium-Druckguss bis zu 200 Tonnen Heißkammer und 3000 Tonnen Kaltkammer, Werkzeugdesign, Polieren, Formen, Bearbeitung, Pulver- und Flüssiglackierung, vollständige Qualitätssicherung mit KMG-Fähigkeiten , Montage, Verpackung & Lieferung.
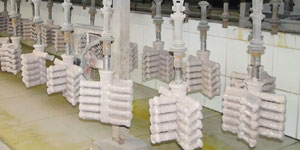
ITAF16949-zertifiziert. Zusätzlicher Casting-Service inklusive Feinguss,Sandguss,Schwerkraftguss, Verlorener Schaumguss,Schleuderguss,Vakuumgießen,Dauerguss,.Zu den Fähigkeiten gehören EDI, technische Unterstützung, Volumenmodellierung und Sekundärverarbeitung.
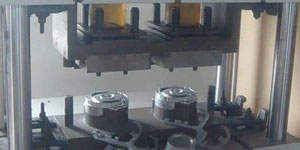
Gussindustrie Teile-Fallstudien für: Autos, Fahrräder, Flugzeuge, Musikinstrumente, Wasserfahrzeuge, optische Geräte, Sensoren, Modelle, elektronische Geräte, Gehäuse, Uhren, Maschinen, Motoren, Möbel, Schmuck, Vorrichtungen, Telekommunikation, Beleuchtung, medizinische Geräte, Fotogeräte, Roboter, Skulpturen, Tongeräte, Sportgeräte, Werkzeuge, Spielzeug und mehr.
Was können wir Ihnen als nächstes helfen?
∇ Zur Startseite gehen für Druckguss China
→Gussteile- Finden Sie heraus, was wir getan haben.
→Bewertete Tipps zu Druckgussdienste
By Minghe Druckgusshersteller |Kategorien: Hilfreiche Artikel |Werkstoff Stichworte: Aluminiumguss, Zinkguss, Magnesiumguss, Titanguss, Edelstahlguss, Messingguss,Bronzeguss,Casting-Video,Unternehmensgeschichte,Aluminiumdruckguss |Kommentare deaktiviert