Verwaltung von Aluminiumlegierungen und Hilfsstoffen in der Druckgussproduktion
Hauptmaterialmanagement
1. Eingangskontrolle von Barren aus Aluminiumlegierungen
Aufgrund des Gasgehalts und der Anforderungen an den harten Punkt von Aluminiumlegierungen müssen Aluminiumbarren-Produktionsanlagen eine gute Arbeit beim Raffinieren, Entgasen und Entfernen von Schlacke leisten, um zu verhindern, dass Defekte wie ein hoher Gasgehalt und viele Verunreinigungen in Aluminiumbarren in die Form vererbt werden. Aluminium flüssig gießen. Nachdem der Barren aus Aluminiumlegierung die Fabrik erreicht hat, besteht der erste Schritt darin, das Aussehen zu überprüfen. Die Oberfläche des Aluminiumbarrens muss glatt, frei von Rauheit, frei von Ölflecken, Schimmel und Oxidzunder sein, und die Bruchstruktur des Aluminiumlegierungsbarrens ist fein und dicht. Es sollte keine ernsthafte Segregation, Schrumpfung oder Schrumpfung auftreten. Schlacke und Einschlüsse. Probenahme der Zusammensetzung jeder Charge und Schmelznummer, um sicherzustellen, dass die verwendete Legierungszusammensetzung qualifiziert ist. Bei der Herstellung von Produkten mit besonderen Anforderungen müssen weitere Prüfpunkte hinzugefügt werden. Bei der Herstellung von Produkten mit mechanischen Leistungsanforderungen ist es beispielsweise erforderlich, wenn der Barren aus Aluminiumlegierung zur Produktion geliefert wird, für jeden Ofen einen Zugprüfstab vorzulegen; Bei der Herstellung von Produkten mit Anforderungen an die Luftdichtheit muss der Pinhole-Grad des Barrens aus Aluminiumlegierung erhöht werden. Erkennen
Die Arten von Aluminiumlegierungen, die in der tatsächlichen Produktion verwendet werden, sind oft nicht auf eine Sorte beschränkt, und die Anforderungen an die chemische Zusammensetzung jeder Sorte von Aluminiumlegierungen sind ziemlich unterschiedlich. Die Hauptelemente einer Legierungssorte sind in einer anderen Legierungssorte enthalten. Es kann als Verunreinigung betrachtet werden. Für die Koexistenz mehrerer Qualitäten ist es notwendig, die Legierungen jeder Qualität deutlich visuell zu unterscheiden, um eine Vermischung während des Gebrauchs zu vermeiden. Die allgemeine Maßnahme besteht darin, die Farbe des Aussehens von Aluminiumlegierungen verschiedener Marken und verschiedener Hersteller eindeutig und einheitlich zu spezifizieren und verschiedene Materialien nach ihrer Ankunft im Werk in verschiedenen Bereichen zu lagern.
2. Kontrolle des Schmelzprozesses der Aluminiumlegierung
Die Produktionspraxis zeigt, dass die Verbesserung der Qualität der Legierungsschmelze ein Schlüsselfaktor für die Verbesserung der Qualität von Druckgussteilen ist. Daher sollte das Rohstoffmanagement streng kontrolliert werden, damit keine unqualifizierten Rohstoffe in die Werkstatt oder in die Produktion gelangen. Streng nach den für den Legierungsschmelzprozess erforderlichen Standards arbeiten und das Management verschiedener Rohstoffe (neue Materialien, recycelte Materialien und Hilfsstoffe) stärken.
Der Schmelzprozess von Aluminiumlegierungen muss klare Vorschriften hinsichtlich der Schmelztemperatur, der Schmelzzeit und des Anteils der nachgebrannten Materialien haben, insbesondere sollten die nachgebrannten Materialien streng klassifiziert und verwaltet werden und dürfen nicht gemischt werden. Das recycelte Material sollte sauber und frei von Öl, Rost, Schlamm, Feuchtigkeit und Einsätzen sein. Die öligen Verunreinigungen im Recyclingmaterial können vom Aluminiumbarrenhersteller umgeschmolzen werden und können nicht direkt in den Schmelzofen eingesetzt werden; Für die verstreuten Aluminiumblöcke müssen diese gesiebt und Staub, Sand und andere Ablagerungen im Inneren entfernt werden. Verwendung: Wenn das geschmolzene Aluminium zum Wiedererhitzen verwendet wird, ist das Verhältnis von Läutermittel und Schlackenentferner größer als wenn nur Barren aus Aluminiumlegierung zum Schmelzen verwendet werden. Bei der Herstellung bei Wetter mit hoher relativer Luftfeuchtigkeit sollte der Anteil des Recyclingmaterials 30 % nicht überschreiten, und das Recyclingmaterial kann bei trockenem Wetter entsprechend erhöht werden, sollte jedoch 40 % nicht überschreiten.
Die Verschlackung und Entgasung von geschmolzenem Aluminium nach dem Schmelzen sollte rechtzeitig erfolgen und die entsprechenden Parameter sind bei Bedarf zu erfassen. Beim zentralisierten Schmelzprozess sollte die chemische Zusammensetzung jedes Topfes mit flüssigem Aluminium getestet werden, um sicherzustellen, dass die chemische Zusammensetzung des Produkts während des Schmelzprozesses qualifiziert ist. Darüber hinaus sollte ein langfristiges Schmelzen vermieden werden, da sonst der Wasserstoffgehalt in der Flüssigkeit der Aluminiumlegierung ansteigt, was die Festigkeit und Luftdichtheit des Druckgussprodukts beeinträchtigt. Im Allgemeinen vergehen nicht mehr als 4 Stunden vom Schmelzen bis zum Druckgießen.
Verwaltung von Hilfsstoffen
1. Kontrolle des Trennmittels
Die Verwendung von Formtrennmitteln kann das flüssige Metallbefüllen reibungslos machen, das Umformen erleichtern, das Verkleben der Form verhindern, Gussteile eine glänzende, glatte und ebene Oberflächenqualität verleihen und einen großen Einfluss auf Produktionsrhythmus, Gussoberfläche und Innenqualität haben. Gleichzeitig kann es die Form schützen, die Erosion von Hochtemperatur-Flüssigmetall auf der Formoberfläche vermeiden, die Wärmeleitfähigkeit und Formtemperatur der Form reduzieren und die Lebensdauer der Form verlängern. Wenn die Form geöffnet wird, trägt dies zum reibungslosen Auswerfen des Gussstücks bei und spielt auch eine wichtige Rolle bei der Verringerung der Reibung und des Verschleißes von Stempel, Auswerferstange und beweglichen Teilen. Die Steuerung des Trennmittels umfasst nicht nur die Auswahl und das Verhältnis des Trennmittels selbst, sondern umfasst auch die Steuerung des Sprühens und Föhnens des Trennmittels durch den Bediener. Generell werden an die Auswahl des Trennmittels folgende Anforderungen gestellt.
- Es hat eine gute Schmierfähigkeit bei hohen Temperaturen und einen niedrigen Verflüchtigungspunkt. Das Wasser im Trennmittel kann sich bei 100-150°C schnell verflüchtigen.
- Es hat keine korrosive Wirkung auf Druckgussformen und Druckgussteile und hat eine stabile Leistung. Das Trennmittel sollte sich nicht zu schnell verflüchtigen und an der Luft verdicken.
- Bei hoher Temperatur wird kein schädliches Gas ausgeschieden, und es tritt keine Verschmutzung auf der Oberfläche des Druckgusshohlraums auf.
Gegenwärtig ist das Sprühen des Trennmittels hauptsächlich ein manueller Vorgang, und ein vernünftiger Sprühvorgang ist ein wichtiger Faktor, um die Qualität des Gusses, die Lebensdauer der Druckgussform und die Produktionseffizienz sicherzustellen. Die Sprühzeit des Formtrennmittels ändert sich auch mit der Formtrennleistung, dem Verdünnungsverhältnis, unterschiedlichen Druckgussformen und unterschiedlichen Formtemperaturen verschiedener Arten von Formtrennmitteln. Das Trennmittel wird aus der Spritzpistole auf die Oberfläche der Form gesprüht und kondensiert zu einem Schutzfilm. Es braucht viel Zeit. Wenn der Prozess nicht abgeschlossen ist, wird der Gießvorgang durchgeführt, der oft die Ursache für die losen Gussfehler ist. Nach den Vorschriften des Druckgussverfahrens sollte für einen anderen Trennmitteltyp und andere Verdünnungsverhältnisse ein vernünftiger Spritzzeitbereich gewählt werden. Druckgussarbeiter müssen die Bedeutung der Ober- und Untergrenzen der Prozessparameter und den Trend des Anpassungseinflusses verstehen und entsprechend der Oberflächenbeschaffenheit der produzierten Druckgussteile entsprechende Anpassungen vornehmen.
Bei der Verwendung von Trennmitteln auf Wasserbasis muss das Verhältnis der Trennmittel streng kontrolliert werden. Wenn das Verhältnis Trennmittel zu Wasser zu dick ist, bildet sich ein dickerer Film auf der Formoberfläche und es bilden sich langsam Trennmittelansammlungen auf der Formoberfläche. Die Feuchtigkeit im Trennmittel kann nicht vollständig abgeleitet werden und es entstehen Gase, die das Druckgussteil herstellen. Die innere Kompaktheit verschlechtert sich. Ist das Verhältnis Trennmittel zu Wasser zu dünn, wird die Wirkung nicht erreicht und die Druckgussteile leiden unter Verspannungen und Formverklebungen.
In der Qualitätskontrolle der Druckgusswerkstatt hat daher das Management des Trennmittels einen größeren Einfluss auf die Qualität der Druckgussteile. Es ist notwendig, das Management in diesem Bereich zu stärken, wie z. B. die Ernennung einer speziellen Person, die für den Anteil des Trennmittels verantwortlich ist, und die klare Festlegung verschiedener Arten von verschiedenen Das Verhältnis von Trennmittel und Wasser im Produktionsprozess von Druckguss Produkte wird nach dem Trennmittel-Herstellungsverfahren bestimmt und quantifiziert. Beim Spritzen muss der Bediener eine strenge Schulung bezüglich der Spritzwirkung durchführen, und die Aktion muss gemäß den Anforderungen und Spezifikationen durchgeführt werden, und es darf nicht mehr, weniger Spritzen oder Fehlspritzen gesprüht werden.
2. Stanzölmanagement
Gegenwärtig werden die meisten Stanzschmieröle oder Partikelschmierungen auf Ölbasis verwendet, egal welche Form der Stanzschmierung, nachdem die Aluminiumflüssigkeit in den Lauf gelangt ist, muss sie in kurzer Zeit vollständig verbrannt und die Rückstände verteilt werden auf der oberen Schicht der Legierungsflüssigkeit, damit der Einfluss des Stempelöls auf das Produkt nicht zu groß ist. Andernfalls gelangen das bei der Verbrennung entstehende Gas und die Rückstände nach der Verbrennung in das Produkt, und das Ergebnis kann man sich vorstellen.
Der einfache Weg, das Stanzöl zu überprüfen, besteht darin, die Farbe des Materialgriffs an der Form zu beobachten. Im Allgemeinen beträgt die Dicke des Materialgriffs 1/3 bis 1/4 des Durchmessers des Stempels, und die Länge der Schwärzung des Stempelöls sollte 3 der Dicke des Materialgriffs nicht überschreiten. /5; Gleichzeitig sollte am Ende des Materialstiels keine deutliche Schwärzung (also zu viel Graphitpulverreste) vorhanden sein. Andernfalls nehmen nach der Verarbeitung des Produkts unweigerlich Defekte wie Poren zu.
Im Produktionsprozess sollten wir auch jederzeit auf den Betriebszustand der Stempelschmiereinrichtung achten. Wird zu viel oder zu wenig Schmierstoff gesprüht, wirkt sich dies negativ auf die Lebensdauer der Druckkammer und des Stempels sowie auf die Qualität des Druckgusses aus. Bei der Einstellung der verwendeten Schmiermittelmenge ist sowohl die Schmierfähigkeit des Stempels als auch die Entformbarkeit der Form zu berücksichtigen. Insbesondere bei der Verwendung von Partikelschmierung besteht unabhängig davon, wie die Wachspellets in der Druckgussform verwendet werden, das Problem der Verflüchtigung organischer Stoffe. Wenn eine große Menge flüchtiger organischer Stoffe nicht gut abgeführt werden kann, hat dies einen großen Einfluss auf die Porenbildung im Druckgussteil.
3. Stanzverwaltung
Stempel und Druckkammer bilden ein voneinander abhängiges System. Unter normalen Umständen kann die Lebensdauer der Druckkammer 2 bis 3 Jahre erreichen, und die Lebensdauer eines Stempels ist kurz, eine Schicht und die lange Lebensdauer kann mehr als 10,000 Mal erreichen. Die unterschiedliche Lebensdauer führt zu Schwankungen in der Produktqualität und zu erheblichen Änderungen der Produktionskosten. Daher kann ein gutes Stempelmanagement nicht nur die Qualität von Druckgussteilen stabilisieren, sondern auch die Produktionskosten des Druckgusses stark reduzieren.
- Design der Stempelgröße. Unter normalen Umständen muss zwischen Stempel und Druckkammer ein gewisses Spiel vorhanden sein. Die Praxis zeigt, dass der ideale Spalt etwa 0.1 mm beträgt. Wenn der Spalt während des Einspritzens zu groß ist, kann die Flüssigkeit aus der Aluminiumlegierung in den Spalt eindringen, und es tritt ein Austreten von Aluminiumflüssigkeit und Rauch auf, was den Verschleiß des Stempels verschlimmert und die Lebensdauer des Stempels verringert; wenn der Spalt zu klein ist, bewegt sich der Stempel im Prozess Es kommt zu einem Verklemmen, die Geschwindigkeit des Stempels kann die vom Prozess vorgegebene Geschwindigkeit nicht erreichen, die Füllzeit der Form verlängert sich und die Qualitätsprobleme des Druckgusses Teile erhöhen. Daher muss die Verarbeitung und Herstellung des Stempels streng nach Zeichnung erfolgen, um den kritischen Spalt endgültig zu kontrollieren, die Lebensdauer des Stempels zu verlängern und die Qualität des Produkts sicherzustellen.
- Die Kühlung des Stempels Da sich durch den Druckgussprozess die Temperatur des Stempels ständig ändert, ändert sich mit der Temperaturänderung auch der Spalt zwischen Stempel und Druckkammer. Diese Veränderungen wirken sich nicht nur auf die Standzeit des Stempels aus, sondern auch auf die Stabilität des Spritzprozesses während des Druckgussprozesses. Um den idealen Spalt beizubehalten, ist es notwendig, den Stempel zu kühlen. Bei der Konstruktion wurde berücksichtigt, dass der Kolben durch den Wasserkern der Spritzstange vollständig gekühlt wird und die Wärme des Stempels maximal abgeführt wird und der ideale Spalt zwischen Stempel und Druckraum eingehalten werden kann stabil. Diese Maßnahmen tragen dazu bei, die Stabilität des Spritzprozesses jeder Form und die Stabilität der Qualität der Druckgussprodukte zu gewährleisten. Die Praxis hat gezeigt, dass das Einspritzsystem mit guter Stempelkühlung die Standzeit des Stempels erheblich verlängern kann und gleichzeitig die Stabilität des Einspritzprozesses gewährleistet. Es ist jedoch erforderlich, den Kühlwasserkreislauf des Stempels gut abzudichten und sich vor dem Austreten von Kühlwasser zu hüten, das durch eine schlechte Abdichtung zwischen dem Stempel und der Einspritzstange verursacht wird. Wenn dem Austreten von Kühlwasser nicht genügend Aufmerksamkeit geschenkt wird, kann dies das Produkt ernsthaft beeinträchtigen. Luftdichtheit.
4. Tiegelmanagement
Die Verwendung von Tiegeln ist beim Druckgießen von Aluminiumlegierungen, insbesondere bei der Verwendung von Gusseisentiegeln, von großer Bedeutung. Wenn die Tiegel nicht streng nach den Tiegelspezifikationen betrieben werden können, kann der Fe-Gehalt in der Aluminiumlegierungszusammensetzung im nachfolgenden Produktionsprozess den Standard überschreiten. Wenn der Gusstiegel nach unseren Erfahrungen mit dem Tiegellack streng nach den Anforderungen für den Einsatz des neuen Topfes gebürstet und alle 3 Tage während des Gebrauchs gebürstet werden kann, steigt im Wesentlichen der Fe-Gehalt während der gesamten Kokille. Der Gussproduktionsprozess wird 0.2% nicht überschreiten (dies sind die statistischen Daten des Unternehmens im Laufe der Jahre, es können einige Unterschiede zwischen verschiedenen Unternehmen bestehen). Unter der Prämisse, die Eingangskontrolle von Barren aus Aluminiumlegierungen zu kontrollieren, kann es vollständig garantieren, dass die Legierungszusammensetzung der hergestellten Druckgussteile den Standardanforderungen entspricht. Obwohl bei der Verwendung von Graphittiegeln keine Bedenken hinsichtlich der Zunahme von Eisen bestehen, sollte dies ebenfalls beachtet werden. Der Trocknungsprozess für den Ersteinsatz von Graphittiegeln muss strikt durchgeführt werden. Diese Vorgänge werden sich in Zukunft auf die Lebensdauer von Graphittiegeln auswirken und wurden nicht gut vorgewärmt. Die Lebensdauer von Graphittiegeln wird stark beeinträchtigt. Der hohe Preis jedes Graphittiegels wirkt sich auf die Produktionskosten des Druckgusses aus.
Zusammenfassung
Unter den fünf Hauptelementen des Qualitätsmanagements werden hier hauptsächlich die Themen "Materialien" und "Menschen" behandelt. Beim Umgang mit Roh- und Hilfsstoffen sollte die Ausbildung und Führung des Personals gut erfolgen und das technische Niveau der Druckgussarbeiter muss weiter verbessert werden. Um die Qualitätsprobleme in der Druckgussproduktion effektiv zu lösen, wenden Sie die Idee des Gesamtqualitätsmanagements auf die Qualitätskontrolle der Druckgusswerkstatt an und verwenden Sie systematische Kenntnisse der Theorie der Druckgussproduktion, um die Produktion zu leiten, die wird sicherlich die Qualitätskontrolle der Druckgusswerkstatt auf eine neue Ebene bringen. .
Bitte bewahren Sie die Quelle und Adresse dieses Artikels für den Nachdruck auf: Verwaltung von Aluminiumlegierungen und Hilfsstoffen in der Druckgussproduktion
Minghe Casting Company widmet sich der Herstellung und Bereitstellung von hochwertigen und leistungsstarken Gussteilen (die Palette der Metalldruckgussteile umfasst hauptsächlich mainly Dünnwandiger Druckguss,Heißkammerdruckguss,Kaltkammerdruckguss), Runder Service (Druckguss-Service,CNC-Bearbeitung,Formenbau,Oberflächenbehandlung). Alle kundenspezifischen Aluminium-Druckguss-, Magnesium- oder Zamak/Zink-Druckguss- und andere Gussanforderungen können uns gerne kontaktieren.
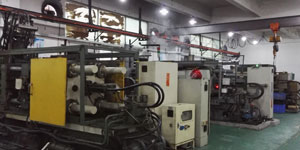
Unter der Kontrolle von ISO9001 und TS 16949 werden alle Prozesse durch Hunderte von fortschrittlichen Druckgussmaschinen, 5-Achsen-Maschinen und anderen Einrichtungen durchgeführt, von Blasgeräten bis hin zu Ultraschall-Waschmaschinen.Minghe verfügt nicht nur über fortschrittliche Ausrüstung, sondern auch über professionelle Team aus erfahrenen Ingenieuren, Bedienern und Inspektoren, um das Design des Kunden zu verwirklichen.
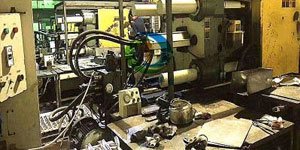
Auftragsfertigung von Druckgussteilen. Zu den Fähigkeiten gehören Kaltkammer-Aluminium-Druckgussteile von 0.15 lbs. bis 6 lbs., Schnellwechseleinrichtung und Bearbeitung. Mehrwertdienste umfassen Polieren, Vibrieren, Entgraten, Kugelstrahlen, Lackieren, Plattieren, Beschichten, Montage und Werkzeugbau. Zu den Materialien, mit denen gearbeitet wird, gehören Legierungen wie 360, 380, 383 und 413.
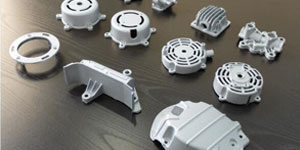
Unterstützung bei der Konstruktion von Zinkdruckguss / gleichzeitige Engineering-Dienstleistungen. Auftragsfertigung von Präzisions-Zink-Druckgussteilen. Es können Miniaturgussteile, Hochdruck-Kokillengussteile, Mehrschieber-Kokillengussteile, konventionelle Kokillengussteile, Einzel- und Einzeldruckgussteile sowie hohlraumdichte Gussteile hergestellt werden. Gussteile können in Längen und Breiten bis zu 24 Zoll in +/-0.0005 Zoll Toleranz hergestellt werden.
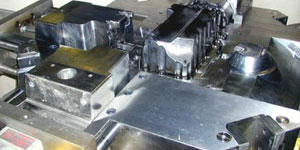
ISO 9001: 2015 zertifizierter Hersteller von Magnesium-Druckguss. Zu den Fähigkeiten gehören Hochdruck-Magnesium-Druckguss bis zu 200 Tonnen Heißkammer und 3000 Tonnen Kaltkammer, Werkzeugdesign, Polieren, Formen, Bearbeitung, Pulver- und Flüssiglackierung, vollständige Qualitätssicherung mit KMG-Fähigkeiten , Montage, Verpackung & Lieferung.
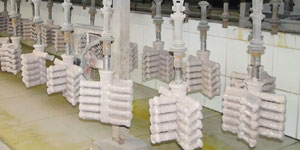
ITAF16949-zertifiziert. Zusätzlicher Casting-Service inklusive Feinguss,Sandguss,Schwerkraftguss, Verlorener Schaumguss,Schleuderguss,Vakuumgießen,Dauerguss,.Zu den Fähigkeiten gehören EDI, technische Unterstützung, Volumenmodellierung und Sekundärverarbeitung.
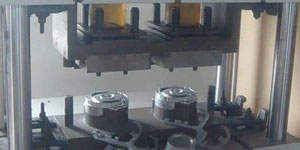
Gussindustrie Teile-Fallstudien für: Autos, Fahrräder, Flugzeuge, Musikinstrumente, Wasserfahrzeuge, optische Geräte, Sensoren, Modelle, elektronische Geräte, Gehäuse, Uhren, Maschinen, Motoren, Möbel, Schmuck, Vorrichtungen, Telekommunikation, Beleuchtung, medizinische Geräte, Fotogeräte, Roboter, Skulpturen, Tongeräte, Sportgeräte, Werkzeuge, Spielzeug und mehr.
Was können wir Ihnen als nächstes helfen?
∇ Zur Startseite gehen für Druckguss China
→Gussteile- Finden Sie heraus, was wir getan haben.
→Bewertete Tipps zu Druckgussdienste
By Minghe Druckgusshersteller |Kategorien: Hilfreiche Artikel |Werkstoff Stichworte: Aluminiumguss, Zinkguss, Magnesiumguss, Titanguss, Edelstahlguss, Messingguss,Bronzeguss,Casting-Video,Unternehmensgeschichte,Aluminiumdruckguss |Kommentare deaktiviert