Der Zusammenhang zwischen Eisenkostensenkung und Hochofenproduktion
Im immer härter werdenden Wettbewerb und der aktuell schwierigen Stahlmarktsituation kann die Kostenreduktion als „ein Zoll Gold“ bezeichnet werden. Wer eine stärkere Kostenkontrolle hat, hat mehr Raum zum Überleben und zur Entwicklung.
Mit dem jüngsten Anstieg der Stahlpreise werden verschiedene Stahlwerke die Produktion wieder aufnehmen, auch die Betriebsrate der Hochöfen wird weiter steigen, die Nachfrage nach Eisenerz wird steigen und der Preis für Eisenerz wird steigen. Bezogen auf vergangene Daten ist der Eisenerzpreis relativ elastisch. Daher wird die derzeitige Gewinnverbesserungssituation für Stahlwerke aufgrund steigender Stahlpreise und nachlassender Erzpreise nicht ewig andauern, und Probleme in nachfolgenden Produktionsorganisationen werden nach und nach aufgedeckt. Daher ist die Kostensenkung ein langfristiger kontinuierlicher Prozess, und es ist auch eine Notwendigkeit für Stahlunternehmen, auf Marktveränderungen zu reagieren.
Die Roheisenkosten machen 70-80% der Kosten der Stahlproduktion aus, was der Schlüssel zur Verbesserung der Kostenkontrolle ist. Mit anderen Worten, die Kosten für geschmolzenes Eisen bestimmen direkt die Kosten für Stahl. Wie organisieren wir uns also, um Kosten zu senken und gleichzeitig die Stabilität des Produktionssystems zu gewährleisten? Kombinieren Sie den Produktionsstatus von Longgang, um über unsere Gedanken und Praktiken zu sprechen.
Der Aufbau einer Hochofendirektproduktion ist der größte Kostenfaktor
Der Hochofenbetrieb ist ein komplexer Prozess, der von allen Aspekten wie Rohstoffen, Ausrüstung, Betriebsebene, Managementebene und peripheren Garantien beeinflusst wird. Der stabile, effiziente und kostengünstige Betrieb des Hochofens ist untrennbar mit der Gewährleistung von Koks-, Pellets-, Stückerzbeschaffung, Sinterproduktionsorganisation, Stromenergie und anderen Verbindungen verbunden. Unter dem bestehenden Managementsystem von Longgang sind alle Verbindungen eng um die stabile und reibungslose Hochofenorganisation herum organisiert.
Der Kern von Hochofen anterograde besteht darin, die untere Flüssigkeitsdurchlässigkeit und die obere Luftdurchlässigkeit sicherzustellen. Um die untere Flüssigkeitsdurchlässigkeit und die obere Gasdurchlässigkeit zu verbessern, muss man sich um die Qualität des Rohbrennstoffs und den Betrieb kümmern. Die Zusammensetzung und die metallurgischen Eigenschaften des Rohbrennstoffs müssen „stabil“ sein, je höher die Stabilität, desto besser. Der Gehalt und die Beladung schädlicher Elemente im Ofen müssen „streng kontrolliert“ und „wissend“ sein, damit der Hochofen rechtzeitig wirksame Maßnahmen ergreifen kann.
Der Hochofenbetrieb muss flexibel sein. Für Unternehmen wie Longgang, die zur Aufrechterhaltung der Produktion auf ausgelagerte Rohstoffe angewiesen sind, ist die Versorgung mit Rohstoffen und Brennstoffen extrem unausgewogen. Was muss man grundsätzlich essen? Die Schwierigkeit, den Hochofenbetrieb einzustellen, wird stark erhöht. Gegenwärtig ist es im Wesentlichen gelungen, welche Art von Rohstoffen und Brennstoffen zur Verfügung stehen und das Konzept des Ofenzustandsmanagements auf welche Art von Betrieb abgestimmt ist, wodurch das bisherige "große einheitliche" oder "langfristig unveränderte" umfangreiche Management entfällt. Die Energie des Hochofenmanagements konzentriert sich hauptsächlich auf die Lösung der Probleme, die die reibungslose Bewegung des Hochofens beeinträchtigen. Sie ist nicht nur die sichere und reibungslose Umsetzung der Produktionsorganisation, sondern auch der Schlüssel zur kontinuierlichen Senkung der Roheisenkosten.
Bestehen Sie auf dem Konzentrat und entspannen Sie sich nicht
Eingeschränkt durch Sinter- und Erzmischressourcen, führt Longgang selten Sinterbechertests durch. Grundsätzlich ist es mit allem Erz ausgestattet, das verfügbar ist. Als Ergebnis weist der Sinterprozess eine langfristige unangemessene Erzvermischung, eine instabile Qualität, eine schlechte physikalische Qualität des gesinterten Erzes und unter dem Hochofentank auf. Die Schaumbildungsrate ist hoch.
Im Jahr 2016 wurden unter der Leitung des technischen Teams der Eisenhütte die Chargenoptimierungsgruppe, der Rohstoffbetriebsbereich, die Rohrgruppe und die technische Stärke des Eisenherstellungs- und Sinterprozesses integriert und eine Plattform für das Management von Voreisenrohstoffen aufgebaut . Das gesamte Voreisensystem nahm seinen Dienst rund um den Hochofen auf. Zum Beispiel werden das technische Team und das Chargenoptimierungsteam den Service voranbringen, indem sie den ganzen Tag über eingehende Materialien, Zutaten und Informationen zu Hofwechseln beherrschen und sich auf die Verfolgung von Änderungen bei Koks, Injektionskohle und anderen Kohlemischungen konzentrieren und Zusammensetzungsänderungen genau vorhersagen müssen und Qualitätsschwankungen im Voraus an den Hochofen senden Die Frühwarninformation minimiert die negativen Auswirkungen von Rohstoff- und Brennstoffänderungen auf die Stabilität des Hochofens und untersucht kontinuierlich die Management- und Betriebsweisen von "Economic Materials" und "Fine Rohre", um den Grundstein für die Langzeitstabilität des Hochofens zu legen.
Sparsame und vernünftige Zutaten
Voraussetzung für wirtschaftliche Inhaltsstoffe sind wissenschaftliche und sinnvolle Inhaltsstoffe, und wir kennen die Eigenschaften aller eingekauften Rohstoffe und Brennstoffe, um unsere Stärken zu maximieren und Schwächen zu vermeiden. Die Produktionsorganisation der Eisenherstellung muss die Kommunikation und Koordination mit verschiedenen Einheiten vor dem Eisen stärken und einen vernünftigen Rohstoffbeschaffungsplan formulieren. Bei der Implementierung von Sinterchargen müssen nicht nur die Effizienz und Qualität der Chargenarbeit verbessert und die Sinterkosten gesenkt werden, sondern auch die Kontrolle verschiedener schädlicher Elemente berücksichtigt werden; es ist notwendig, die Qualität des gesinterten Erzes mit besseren Indikatoren stabiler zu machen, aber auch die Gesamtkosten des Sinterns zu senken und den Hochofen "besser zu essen".
Die vernünftige Chargenstruktur des Hochofens zielt darauf ab, den besten wirtschaftlichen Nutzen für die Eisenerzeugung zu erzielen. Um den Klinkeranteil zu erhöhen, muss weniger oder kein Stückerz verwendet werden. Der Stückpreis von Stückerz ist jedoch niedriger und hat Kostenvorteile, hat aber andere Inhaltsstoffe. Stabil, schlechte metallurgische Eigenschaften, schlechte Partikelgrößenzusammensetzung, Nachteile der Hochofenschmelze.
Gegenwärtig hat Longgang ein Kostenoptimierungsteam aufgebaut, das hauptsächlich aus Schlüsseltechnikern besteht, um die Kommunikation mit der Beschaffungsabteilung zu stärken. Je nach Qualität der Rohstoffe, Preise, Ressourcen, schädlichen Elemente, wissenschaftlichen Inhaltsstoffe und sorgfältigen Berechnungen wird zuerst die Berechnung durchgeführt. Stapeln, durch vernünftige Berechnung und Führung der tatsächlichen Kosten mit theoretischen Kosten, so dass die Zutaten und Materialien im Prozess gut bekannt sind. Wählen Sie gleichzeitig das Chargengefüge unter aktuellen Bedingungen entsprechend dem Produktionsstatus des Hochofens. Bei der Optimierung der Chargenstruktur müssen die ungünstigen Faktoren, die den Hochofen beeinflussen, schrittweise beseitigt werden (hauptsächlich die Kontrolle der Belastung des Ofens mit schädlichen Elementen). Das Optimierungsteam hat auch aktiv mit anderen fortschrittlichen Unternehmen kommuniziert, um Mängel auszugleichen, die Chargenverfahren zu verbessern und im Wesentlichen eigene Modelle zur Chargenoptimierung und Kostenberechnung zu entwickeln.
Allerdings haben wir noch Probleme bei der Auswahl der Hochofenchargenstruktur. Der Anteil an Stückerz erreicht grundsätzlich 15-20%, ohne oder nur 3-5% Pellets. Das Hauptproblem ist die vernünftige Auswahl von Sinter, Pellets und Sinters bei schlechten metallurgischen Eigenschaften von gesintertem Erz (der Niedrigtemperatur-Reduktionspulverisierungsindex (+3.15 mm) lag im Durchschnitt bei 53.97 bzw. 61.64% im Februar und März 2016). Der Anteil an Stückerz muss noch immer von uns ständig erforscht und zusammengefasst werden.
Optimieren Sie den Sinterprozess, um die Qualität des gesinterten Erzes zu verbessern
Gesintertes Erz macht 75-80% der gesamten Rohstoffe des Hochofens aus. Zusammensetzung, Festigkeit, Partikelgrößenzusammensetzung und metallurgische Eigenschaften des gesinterten Erzes wirken sich direkt auf die Stabilität des Hochofens aus. Die hohe Temperatur des Sinters und die Tropfenleistung spielen eine entscheidende Rolle für die Stabilität der Hochofenschmelze.
Von Januar bis März 2016 waren die metallurgischen Eigenschaften des gesinterten Erzes von Longgang schlecht. Der Worst-Case-Niedertemperatur-Reduktions-Pulverisierungsindex (+3.15 mm) betrug nur 44.56%, was der Produktion des Hochofens großen Schaden zufügte, und der Druck war lange Zeit unangenehm. Es kann nur ein Betrieb mit geringer Intensität garantiert werden. Jetzt haben wir die Bedeutung der Sinterqualität erkannt und haben eingehende Forschungen zur Sinterproduktionstechnologie und zur Optimierung der Erzmischung durchgeführt, basierend auf der Verbesserung der metallurgischen Eigenschaften von Sinter, und haben aktiv die Hauptfaktoren untersucht, die die Hochtemperaturleistung beeinflussen von Sinter und die Stärkung des wirtschaftlichen Erzes, um Hochöfen zu beeinflussen. In der Erforschung einer stabilen Produktion wurden mehr als 10 Öfen für Sinterreduktionstests und Niedertemperatur-Pulverisierungstests organisiert, die eine technische Garantie für den großtechnischen Einsatz von wirtschaftlichem Erz, stabiler Sinterqualität, Hochofenindikatoren und -kosten bieten.
Für einen kostengünstigen Betrieb von Hochöfen müssen günstige Voraussetzungen geschaffen werden
Konzentriert auf die Reduzierung der Ofengüte und die große Menge an kostengünstigen Rohstoffen, die in den Sinter- und Hochofen gelangen, bringt dies viele Nachteile für den Hochofen mit sich. Die Produktionsorganisation muss vorausplanen, um die Mindestreserve an Produktionsmaterial sicherzustellen und mehrere Sätze von technischen und betrieblichen Garantieprogrammen wissenschaftlich zu formulieren. Ein raffiniertes Brennstoffmanagement soll die Inkompatibilität des Hochofens durch die Anpassung der Mischmaterialstruktur berücksichtigen und sicherstellen, dass sowohl ein kostengünstiges Erz in den Ofen erreicht werden kann, als auch das Ziel der Sicherstellung des reibungslosen Hochofens gewährleistet werden kann.
Angesichts der derzeitigen Überkapazitäten an Roheisen ist die hochintensive Schmelz- und Produktionsorganisation des 2000 m³-Hochofens von Longgang den Marktanforderungen nicht mehr gewachsen. Die Leistung des Hochofens sollte entsprechend angepasst werden und Möglichkeiten zur Stabilisierung der Produktion und zur Reduzierung des Brennstoffverhältnisses unter verschiedenen Rohstoff- und Brennstoffbedingungen untersucht werden. Die Betriebsweise setzt die langfristig und stabil gute Dynamik des Hochofens fort.
In dieser Phase muss der Hochofen hochwertigen Koks unterstützen, um das Kohleeinspritzverhältnis zu erhöhen und das Koksverhältnis zu senken. Unter der aktuellen Situation der instabilen Rohbrennstoffversorgung und der instabilen Qualität von Longgang ist es notwendig, die Koksqualität zu verbessern, den thermischen Index zu verbessern und den Hochofen zu reduzieren Reduzierung, wodurch günstige Bedingungen für die Reduzierung der Kosten des Eisenfrontsystems geschaffen werden.
Der professionelle Ausbildungsleiter ist unermüdlich
Gegenwärtig nimmt der Druck auf Umweltschutz, Ressourcen, Kosten und Arbeitskräfteüberschuss des ehemaligen Systems von Long Steel zu, und gleichzeitig sieht es sich mit den Schwierigkeiten des Mangels an Reservetalenten und dem langsamen Wachstum des jungen Rückgrats konfrontiert. Nachdem wir nun die Defizite in der Talentförderung erkannt haben, sollten wir kurz-, mittel- und langfristig planen. Je schwieriger und schwieriger die Zeit ist, desto mehr müssen wir die Ausbildung der Talente verstärken. Im Shaanxi Iron and Steel Ironmaking Technology Training Course, der am 20.-25. März organisiert wurde, erklärten die Lehrer die Details, behandelten umfassende Inhalte, schnitten tief in die wichtigsten Punkte ein und kommunizierten mit der tatsächlichen Situation von Longgang. Der gesamte Prozess hat sehr profitiert und wurde von den Studenten gut angenommen.
Gleichzeitig organisiert das Zweigwerk von Zeit zu Zeit Schulungen. Alle Schulungen konzentrieren sich auf die Erfüllung der Produktionsanforderungen und die Lösung praktischer Probleme. Die Lernanforderungen der Bediener werden regelmäßig gesammelt und die Schulungsmaterialien werden entsprechend den Lernanforderungen organisiert, sodass die Trainer verstehen, lernen und sich erinnern müssen. wohnen. Jeder Major organisiert vierteljährlich praktische Schulungen vor Ort, erklärt und bedient gleichzeitig, verbindet Theorie mit Praxis und verbessert den Ausbildungseffekt.
Zusammenfassung
- Das Eisenfrontsystem muss den entsprechenden Zusammenhang zwischen stabiler Hochofenproduktion und Kostensenkung genau beachten, das Bewusstsein der "roten Linie" der Produktionsorganisation des Eisenfrontsystems fest etablieren und wirksame Maßnahmen ergreifen, um eine stabile Hochofenproduktion zu fördern und kontinuierliche Kostensenkung. Achten Sie gleichzeitig auf Prozess- und Anlagenunfälle, analysieren Sie die Unfallursachen sorgfältig und formulieren Sie schnell Pläne, um einen stabilen Betrieb des Hochofens zu gewährleisten.
- Lange Zeit sah sich das Longgang Ironmaking Plant mit den Schwierigkeiten großer Unterschiede in der Qualität von Roh- und Brennstoffen, einer knappen Versorgung und einer komplexen logistischen Bilanz konfrontiert, die die Stabilität der Eisenproduktion vor große Herausforderungen gestellt haben. Angesichts ungünstiger Faktoren haben wir das Ziel „Kostenoptimierung der Eisenschmelze“ intensiv im Blick, eine vertiefte „Vier-Ebenen-Kostenrechnung“ durchgeführt, das Kostenmanagement für alle Mitarbeiter umfassend und prozessbegleitend mitgewirkt, und förderte weiterhin die "fünf Modernisierungen", die im Wesentlichen eine saubere, stabile, verbrauchsarme und kostengünstige Produktion des Eisenfrontsystems erreichten.
Bitte bewahren Sie die Quelle und Adresse dieses Artikels für den Nachdruck auf:Der Zusammenhang zwischen Eisenkostensenkung und Hochofenproduktion
Mingh Druckgussunternehmen sind der Herstellung und Bereitstellung von hochwertigen und leistungsstarken Gussteilen gewidmet (das Angebot an Metalldruckgussteilen umfasst hauptsächlich) Dünnwandiger Druckguss,Heißkammerdruckguss,Kaltkammerdruckguss), Runder Service (Druckguss-Service,CNC-Bearbeitung,Formenbau,Oberflächenbehandlung). Alle kundenspezifischen Aluminium-Druckguss-, Magnesium- oder Zamak/Zink-Druckguss- und andere Gussanforderungen können uns gerne kontaktieren.
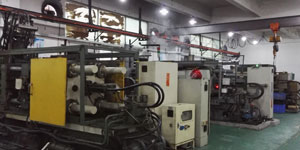
Unter der Kontrolle von ISO9001 und TS 16949 werden alle Prozesse durch Hunderte von fortschrittlichen Druckgussmaschinen, 5-Achsen-Maschinen und anderen Einrichtungen durchgeführt, von Blasgeräten bis hin zu Ultraschall-Waschmaschinen.Minghe verfügt nicht nur über fortschrittliche Ausrüstung, sondern auch über professionelle Team aus erfahrenen Ingenieuren, Bedienern und Inspektoren, um das Design des Kunden zu verwirklichen.
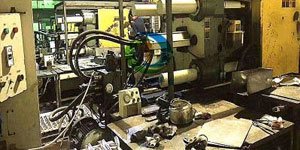
Auftragsfertigung von Druckgussteilen. Zu den Fähigkeiten gehören Kaltkammer-Aluminium-Druckgussteile von 0.15 lbs. bis 6 lbs., Schnellwechseleinrichtung und Bearbeitung. Mehrwertdienste umfassen Polieren, Vibrieren, Entgraten, Kugelstrahlen, Lackieren, Plattieren, Beschichten, Montage und Werkzeugbau. Zu den Materialien, mit denen gearbeitet wird, gehören Legierungen wie 360, 380, 383 und 413.
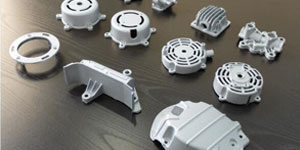
Unterstützung bei der Konstruktion von Zinkdruckguss / gleichzeitige Engineering-Dienstleistungen. Auftragsfertigung von Präzisions-Zink-Druckgussteilen. Es können Miniaturgussteile, Hochdruck-Kokillengussteile, Mehrschieber-Kokillengussteile, konventionelle Kokillengussteile, Einzel- und Einzeldruckgussteile sowie hohlraumdichte Gussteile hergestellt werden. Gussteile können in Längen und Breiten bis zu 24 Zoll in +/-0.0005 Zoll Toleranz hergestellt werden.
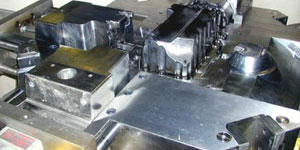
ISO 9001: 2015 zertifizierter Hersteller von Magnesium-Druckguss. Zu den Fähigkeiten gehören Hochdruck-Magnesium-Druckguss bis zu 200 Tonnen Heißkammer und 3000 Tonnen Kaltkammer, Werkzeugdesign, Polieren, Formen, Bearbeitung, Pulver- und Flüssiglackierung, vollständige Qualitätssicherung mit KMG-Fähigkeiten , Montage, Verpackung & Lieferung.
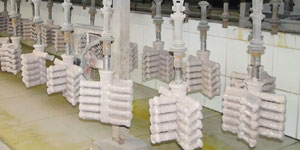
ITAF16949-zertifiziert. Zusätzlicher Casting-Service inklusive Feinguss,Sandguss,Schwerkraftguss, Verlorener Schaumguss,Schleuderguss,Vakuumgießen,Dauerguss,.Zu den Fähigkeiten gehören EDI, technische Unterstützung, Volumenmodellierung und Sekundärverarbeitung.
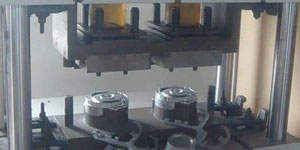
Gussindustrie Teile-Fallstudien für: Autos, Fahrräder, Flugzeuge, Musikinstrumente, Wasserfahrzeuge, optische Geräte, Sensoren, Modelle, elektronische Geräte, Gehäuse, Uhren, Maschinen, Motoren, Möbel, Schmuck, Vorrichtungen, Telekommunikation, Beleuchtung, medizinische Geräte, Fotogeräte, Roboter, Skulpturen, Tongeräte, Sportgeräte, Werkzeuge, Spielzeug und mehr.
Was können wir Ihnen als nächstes helfen?
∇ Zur Startseite gehen für Druckguss China
→Gussteile- Finden Sie heraus, was wir getan haben.
→Bewertete Tipps zu Druckgussdienste
By Minghe Druckgusshersteller |Kategorien: Hilfreiche Artikel |Werkstoff Stichworte: Aluminiumguss, Zinkguss, Magnesiumguss, Titanguss, Edelstahlguss, Messingguss,Bronzeguss,Casting-Video,Unternehmensgeschichte,Aluminiumdruckguss |Kommentare deaktiviert