Sammlung häufiger Fehler und Vorbeugungsmaßnahmen beim Aufkohlen und Abschrecken
Aufkohlen und Abschrecken ist eigentlich ein zusammengesetzter Prozess, nämlich Aufkohlen + Abschrecken. Wir sind es oft gewohnt, über beides zusammen zu sprechen, da die beiden Prozesse, die auf derselben Anlage durchgeführt werden, in der Produktion am häufigsten anzutreffen sind (aber es gibt auch Aufkohlungsluftkühlung, Aufkohlung mit langsamer Abkühlung und dann Wiedererwärmungs- und Abschreckprozesse und sekundäre Abschrecken Prozess) Dann sind einige der unerwünschten Phänomene, die bei der Produktion angetroffen werden, Aufkohlungsprobleme, einige sind Abschreckprobleme und einige sind das Ergebnis der kombinierten Wirkungen von Aufkohlen und Abschrecken.
Wir wissen, dass alle Wärmebehandlungsprozesse untrennbar mit drei Kernthemen verbunden sind: Erwärmung, Wärmeerhaltung und Kühlung. Im Detail, einschließlich Heiztemperatur, Heizrate, Haltezeit, Kühlrate und natürlich Atmosphärenprobleme. Wenn also etwas schief geht, analysieren wir die Ursache gewöhnlich unter diesen Aspekten.
Beim Aufkohlen und Abschrecken testen wir häufig diese Indikatoren: Aussehen der Produktoberfläche, Oberflächenhärte, Kernhärte, aufgekohlte Schichttiefe (effektive Schichttiefe, vollständig gehärtete Schichttiefe), metallographische Struktur und Verformung. Lassen Sie uns meine Ansichten zu diesen Indikatoren teilen.
1. Aussehensproblem
1. Oxidablagerungen: Dies ist hauptsächlich auf Geräteleckagen, unreines Trägergas oder Wassergehalt zurückzuführen. Sie müssen den Grund aus der Ausrüstung und den Rohstoffen finden.
2. Das andere am stärksten problematische Problem ist das Problem der Flecken, das in der modernen Zeit ebenfalls eine neue und herausfordernde Anforderung an die Wärmebehandlung ist. Die Gründe sind kompliziert und sehr tiefgreifend.
zwei. Unqualifizierte Härte
1. Hohe Härte (nicht besprochen)
2. Niedrige Härte: Es gibt zwei Situationen, eine ist das unqualifizierte Aufkohlen. Der Grund dafür kann sein, dass die aufgekohlte Schicht zu flach ist, um die Anforderungen der Zeichnungen zu erfüllen (die aufgekohlte Schicht wird nicht infiltriert), oder der ausgewählte Nachweismaßstab überschreitet den tolerierbaren Bereich der bestehenden aufgekohlten Schicht, wodurch die aufgekohlte Schicht zerstört wird.
Lösung: Füllen Sie die Sickerflüssigkeit auf und folgen Sie dem Inspektionslineal. JBT 6050-2006 "Allgemeine Prinzipien für die Härteprüfung von Stahlteilen durch Wärmebehandlung" Die Tiefe der aufgekohlten Schicht ist tatsächlich eine Funktion von Temperatur, Zeit und Kohlenstoffpotential. Aus den oben genannten Faktoren können wir Wege erwägen, die Heiztemperatur zu erhöhen, die Haltezeit zu verlängern und das Aufkohlungspotenzial zu erhöhen. (Natürlich sollte die Anpassung jedes Parameters vollständig mit den Anforderungen Ihrer eigenen Ausrüstung und Produkte kombiniert werden) Es kann auch an der Existenz von Nicht-Pferdeorganisationen an der Oberfläche liegen. Eine andere Situation tritt ein, wenn die Härte gering ist, d. h. das Aufkohlen ist qualifiziert, das Abschrecken jedoch nicht. Im Allgemeinen wird es nicht gelöscht. Diese Situation ist die komplizierteste, wie das Sprichwort sagt: Bei der Wärmebehandlung wird zu drei Vierteln aufgeheizt und zu sieben Vierteln abgekühlt. Es spiegelt auch die Position wider, die der Kühlprozess im Wärmebehandlungsprozess einnimmt.
Das Folgende ist ein Vergleichstest, den ich entworfen habe. Sie können die Auswirkung der Kühlung auf die Härte diskutieren.
Nehmen Sie 3 Gruppen von Teststäben mit unterschiedlichen Materialien, aber den gleichen Spezifikationen und Abmessungen, deren Größe Φ20 mm x 100 mm beträgt. (Wir nennen Nr. 20 Stahlprüfstab Nr. 1, 20Cr Prüfstab Nr. 2 und 20CrMnTi Prüfstab Nr. 3) Die Prüfstäbe werden in der gleichen Hitze unter Verwendung des gleichen Verfahrens aufgekohlt. Angenommen, die aufgekohlte Schichttiefe der drei Prüfstäbe beträgt 0.6-0.7 mm (ps: Annahme ist nur im Idealzustand begründet).
Bitte beachten Sie folgende Bedingungen:
A. Abschrecken unter den gleichen Bedingungen beenden
B. Abschreckmedium ist langsames Öl, schnelles Öl, klares Wasser, Salzwasser
C. Im gleichen Medium ohne Rühren und intensivem Rühren und Abschrecken werden die drei Prüfstäbe jeweils in zwei Gruppen zur Prüfung entnommen.
Nachdem das Aufkohlen abgeschlossen ist, wird die A-Gruppe bei 800 Grad abgeschreckt und die B-Gruppe wird bei 860 Grad abgeschreckt. Wie ist ihre Härte von hoch nach niedrig? Wie bestellt man die gehärtete Schicht (mit 550HV1.0 als Grenze) von tief nach flach? Nehmen Sie zwei Probestäbe des gleichen Materials und vergleichen und testen Sie, welche Gruppe eine höhere Abschreckhärte und effektive Härteschichttiefe erreichen kann?
Kann aus den obigen Testergebnissen geschlossen werden, dass die Tiefe der aufgekohlten Schicht nicht gleich der Tiefe der wirksamen gehärteten Schicht ist und die tatsächliche gehärtete Schichttiefe von der Härtbarkeit des Materials, der Abschrecktemperatur und der Abkühlung beeinflusst wird? Bewertung. Auch das Kühlverhalten und die Abschreckintensität des Kühlmediums beeinflussen die Abschreckwirkung. Die oben genannten sind die Ansichten der Leute, wenn es Unvollständigkeiten gibt, können Sie sie hinzufügen. Natürlich beeinflusst auch der Größeneffekt der Teile den Härtungseffekt.
Ich denke, ein erfahrener Prüfer kann die wahre Ursache der geringen Härte durch Organisieren und Kombinieren anderer Prüfmethoden feststellen und dann die wahre Ursache finden, um sie zu lösen; als Handwerker, wenn Sie mit den Eigenschaften konventioneller Metallrohstoffe vertraut sind, haben die Kühlleistungen der eigenen Geräte und des Mediums einen gewissen Bekanntheitsgrad erreicht, was bei der Formulierung von Aufkohlungs- und Abschreckprozessen eine große Hilfe ist.
3. Ungleichmäßige Härte: gleichmäßige Ofentemperatur (beeinflusst die Aufkohlungsgleichmäßigkeit), Gerätestruktur, Atmosphärenzirkulation, Ofenbeladung (beeinflusst die Gleichmäßigkeit der Aufkohlungsschicht und beeinflusst gleichzeitig die Abschreckgleichmäßigkeit)
4. Die Kernhärte ist unqualifiziert. Zu hoch: Die Abschrecktemperatur ist zu hoch, die Härtbarkeit des Materials ist zu gut, die Obergrenze der Kohlenstoff- und Legierungszusammensetzung und die mittlere Abkühlgeschwindigkeit ist zu hoch. Die Kernhärte ist gering: im Gegenteil.
Beispielfreigabe: 20# Stahl 1.5 mm Produkt, Anforderungen: Infiltrationsschicht 0.2-0.4 mm Kern HV250, einige Freunde in der gleichen Branche halten die Anforderungen für unangemessen (jeder sollte wissen, dass die höchste Härte von 20# Stahlplatte Martensit sein wird HV450-470) Um dieses Problem zu lösen, müssen wir zuerst die Eigenschaften dieses Materials verstehen: einschließlich Härtbarkeit und Härtbarkeit.
Kombinieren Sie dann die oben genannten Faktoren, die den Abschreckeffekt beeinflussen, und finden Sie Wege zum Heizen und Kühlen. In diesem Fall ist das Material fixiert. Aus der Abschrecktemperatur und der Abkühlgeschwindigkeit können wir einen Weg finden. Dieser Hersteller verwendet zufällig Overspeed-Öl. Wenn die Reduzierung der Abschreckintensität nicht den Anforderungen entspricht, können wir auch die Abschrecktemperatur reduzieren. Methode.
Immer noch derselbe Satz, von 860 bis 760 Grad (wenn die Temperatur auf ein bestimmtes Niveau gesenkt wird, wird eine bestimmte Menge Ferrit aus dem unterkühlten Austenit im Kern ausgeschieden, und die Härte nimmt zu diesem Zeitpunkt ab. , Je mehr die Temperatur sinkt, je mehr Ferrit ausgeschieden wird, desto mehr nimmt die Härte ab.
Hier zur Erinnerung: Es ist notwendig, die bestehenden Bedingungen der Ausrüstung vollständig zu kombinieren und um den besonders günstigen Index der geringen Durchlässigkeit zu rütteln.
3. Die aufgekohlte Schicht oder die wirksame aufgekohlte Schicht ist tiefer und flacher
Wie bereits erwähnt, ist die Tiefe der Infiltrationsschicht eine umfassende Funktion von Temperatur, Zeit und Kohlenstoffkonzentration. Um dieses Problem zu lösen, müssen wir mit der Aufheiztemperatur, Aufheizgeschwindigkeit, Haltezeit, Abkühlgeschwindigkeit und der Kontrolle des Kohlenstoffkonzentrationsgradienten in der Kohlenstoffschicht beginnen. Je höher die Temperatur, desto länger die Zeit, und je höher das Kohlenstoffpotential, desto tiefer die Infiltrationsschicht und umgekehrt.
Tatsächlich ist es aber weit mehr als so einfach. Um einen Aufkohlungsprozess zu entwerfen, müssen Sie auch die Ausrüstung, die Ofenkapazität, die Öleigenschaften, die metallographische Struktur, die Härtbarkeit des Materials, den Kohlenstoffkonzentrationsgradienten in der aufgekohlten Schicht und die Abkühlgeschwindigkeit berücksichtigen. Und viele andere Faktoren. Dies kann mit Bezug auf die vorherige Situation niedriger Härte analysiert werden und wird nicht weiter erläutert.
Viertens, metallographische Organisation
Übermäßiger Martensit: Der Rohstoff ist grobkörnig oder nicht normalisiert und die Aufkohlungstemperatur ist zu hoch. Lösung: Normalisieren oder Mehrfachnormalisieren (es wird empfohlen, dass die Normalisierungstemperatur 20-30 Grad höher ist als die Aufkohlungstemperatur) Wenn möglich, erwägen Sie Aufkohlen und langsames Abkühlen und dann Wiedererhitzen und Abschrecken
Übermäßige Paralympik: Die Abschrecktemperatur ist zu hoch, der Kohlenstoffgehalt im Austenit ist zu hoch (das Kohlenstoffpotential ist zu hoch). Lösung: Vollständige Diffusion und zulassende Bedingungen können die Abschrecktemperatur, Hochtemperatur-Anlassen und Wiedererhitzen und Abschrecken oder kryogene Behandlung reduzieren.
Übermäßiges Karbid: zu hoher Kohlenstoffgehalt im Austenit (zu hohes Kohlenstoffpotential), zu langsamer Abkühlprozess, Karbidausscheidung
Lösung: vollständig diffundieren, die Abkühlgeschwindigkeit kontrollieren, den Temperaturunterschied zwischen Aufkohlen und Abschrecken so gering wie möglich halten und so wenig wie möglich Niedertemperatur- oder Untertemperaturabschrecken verwenden. Wenn dieses Verfahren angewendet werden muss, muss die Ofenbelastung kontrolliert werden. Stellen wir uns vor: Dieselbe Ausrüstung wird bei 920 °C aufgekohlt und bei 820 °C abgeschreckt. Die Ofenkapazität beträgt 1000 kg und 600 kg und die Abkühlgeschwindigkeit ist gleich? Welche dauert länger? Welche Hartmetallsorte ist höher?
Fünfer. Nicht-Pferde- und innere Oxidation
Innere Oxidation: Es ist die Reaktion zwischen Legierungselementen wie Chrom, Mangan und Molybdän im Stahl und der oxidierenden Atmosphäre in der Atmosphäre (hauptsächlich Sauerstoff, Wasser, Kohlendioxid), die die Legierungselemente in der Matrix verarmt, was zu einer Abnahme führt in der Härtbarkeit des Materials. Unter dem Mikroskop ist die schwarze Netzwerkstruktur zu erkennen, ihr Wesen ist die Troostitstruktur, die durch den Abbau von Legierungselementen in der Matrix und die Abnahme der Härtbarkeit entsteht.
Die Lösung besteht darin, Wege zu finden, die Abkühlgeschwindigkeit des Mediums zu erhöhen, die Abschreckintensität zu erhöhen und die oxidierende Atmosphäre im Ofen zu reduzieren (die Reinheit der aufkohlenden Roh- und Hilfsstoffe sicherstellen, die Menge der ausgeglichenen Luft minimieren, die ausgeglichene Luftfeuchtegehalt und stellen Sie sicher, dass das Gerät nicht undicht ist Ausreichende Absaugung) Herkömmliche Geräte sind schwer zu beseitigen. Es wird gesagt, dass die Niederdruck-Vakuum-Aufkohlungsanlage vollständig eliminiert werden kann. Darüber hinaus kann durch kraftvolles Kugelstrahlen auch der interne Oxidationsgrad gesenkt werden.
Ich habe die Meinungen einiger Experten gelesen und einige glauben, dass übermäßiger Ammoniak beim Karbonitrieren auch ernsthafte Unlust verursachen kann. Ich persönlich bin da anderer Meinung: Vielleicht liegt es an einem zu hohen Wassergehalt im Ammoniak? Da ich vielen Karbonitrierungsprozessen ausgesetzt war, wurde bei der Inspektion des Produkts kein offensichtliches Nicht-Pferdegewebe gefunden. (Aber ich glaube nicht, dass diese Ansicht falsch ist) Einige ausländische Maschinenindustrien messen der inneren Oxidation große Bedeutung bei, insbesondere die Zahnradindustrie. Im Inland darf die Tiefe im Allgemeinen nicht mehr als 0.02 mm betragen.
Nicht martensitisch: Eine nicht martensitische Struktur erscheint auf der Oberfläche der aufgekohlten Schicht aufgrund von Aufkohlungs- oder Abschreckproblemen nach dem Abschrecken, wie Ferrit, Bainit und natürlich Troostit vom inneren Oxidationstyp. Der Erzeugungsmechanismus ähnelt der internen Oxidation und die Lösung ist ähnlich.
Sechs. Verformungsproblem
Dies ist ein Systemproblem, und es ist auch das größte Problem für unsere Mitarbeiter in der Wärmebehandlung. Es wird von mehreren Aspekten des Kühlmediums des Rohstoffprozesses garantiert. Der obige Inhalt ist nur eine persönliche Erfahrung. Bei Unstimmigkeiten können Sie mich gerne korrigieren, danke.
Bitte bewahren Sie die Quelle und Adresse dieses Artikels für den Nachdruck auf:Sammlung häufiger Fehler und Vorbeugungsmaßnahmen beim Aufkohlen und Abschrecken
Mingh Druckgussunternehmen sind der Herstellung und Bereitstellung von hochwertigen und leistungsstarken Gussteilen gewidmet (das Angebot an Metalldruckgussteilen umfasst hauptsächlich) Dünnwandiger Druckguss,Heißkammerdruckguss,Kaltkammerdruckguss), Runder Service (Druckguss-Service,CNC-Bearbeitung,Formenbau,Oberflächenbehandlung). Alle kundenspezifischen Aluminium-Druckguss-, Magnesium- oder Zamak/Zink-Druckguss- und andere Gussanforderungen können uns gerne kontaktieren.
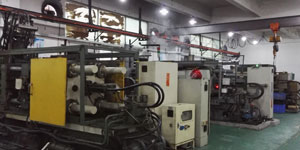
Unter der Kontrolle von ISO9001 und TS 16949 werden alle Prozesse durch Hunderte von fortschrittlichen Druckgussmaschinen, 5-Achsen-Maschinen und anderen Einrichtungen durchgeführt, von Blasgeräten bis hin zu Ultraschall-Waschmaschinen.Minghe verfügt nicht nur über fortschrittliche Ausrüstung, sondern auch über professionelle Team aus erfahrenen Ingenieuren, Bedienern und Inspektoren, um das Design des Kunden zu verwirklichen.
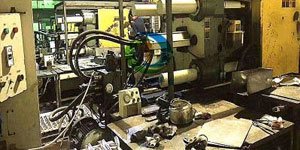
Auftragsfertigung von Druckgussteilen. Zu den Fähigkeiten gehören Kaltkammer-Aluminium-Druckgussteile von 0.15 lbs. bis 6 lbs., Schnellwechseleinrichtung und Bearbeitung. Mehrwertdienste umfassen Polieren, Vibrieren, Entgraten, Kugelstrahlen, Lackieren, Plattieren, Beschichten, Montage und Werkzeugbau. Zu den Materialien, mit denen gearbeitet wird, gehören Legierungen wie 360, 380, 383 und 413.
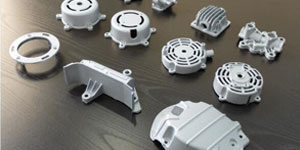
Unterstützung bei der Konstruktion von Zinkdruckguss / gleichzeitige Engineering-Dienstleistungen. Auftragsfertigung von Präzisions-Zink-Druckgussteilen. Es können Miniaturgussteile, Hochdruck-Kokillengussteile, Mehrschieber-Kokillengussteile, konventionelle Kokillengussteile, Einzel- und Einzeldruckgussteile sowie hohlraumdichte Gussteile hergestellt werden. Gussteile können in Längen und Breiten bis zu 24 Zoll in +/-0.0005 Zoll Toleranz hergestellt werden.
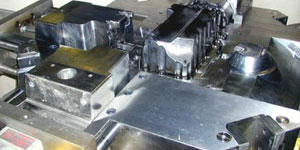
ISO 9001: 2015 zertifizierter Hersteller von Magnesium-Druckguss. Zu den Fähigkeiten gehören Hochdruck-Magnesium-Druckguss bis zu 200 Tonnen Heißkammer und 3000 Tonnen Kaltkammer, Werkzeugdesign, Polieren, Formen, Bearbeitung, Pulver- und Flüssiglackierung, vollständige Qualitätssicherung mit KMG-Fähigkeiten , Montage, Verpackung & Lieferung.
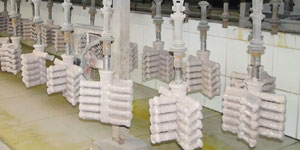
ITAF16949-zertifiziert. Zusätzlicher Casting-Service inklusive Feinguss,Sandguss,Schwerkraftguss, Verlorener Schaumguss,Schleuderguss,Vakuumgießen,Dauerguss,.Zu den Fähigkeiten gehören EDI, technische Unterstützung, Volumenmodellierung und Sekundärverarbeitung.
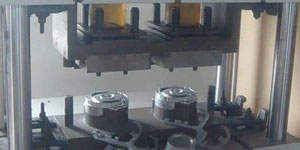
Gussindustrie Teile-Fallstudien für: Autos, Fahrräder, Flugzeuge, Musikinstrumente, Wasserfahrzeuge, optische Geräte, Sensoren, Modelle, elektronische Geräte, Gehäuse, Uhren, Maschinen, Motoren, Möbel, Schmuck, Vorrichtungen, Telekommunikation, Beleuchtung, medizinische Geräte, Fotogeräte, Roboter, Skulpturen, Tongeräte, Sportgeräte, Werkzeuge, Spielzeug und mehr.
Was können wir Ihnen als nächstes helfen?
∇ Zur Startseite gehen für Druckguss China
→Gussteile- Finden Sie heraus, was wir getan haben.
→Bewertete Tipps zu Druckgussdienste
By Minghe Druckgusshersteller |Kategorien: Hilfreiche Artikel |Werkstoff Stichworte: Aluminiumguss, Zinkguss, Magnesiumguss, Titanguss, Edelstahlguss, Messingguss,Bronzeguss,Casting-Video,Unternehmensgeschichte,Aluminiumdruckguss |Kommentare deaktiviert