Verschiedene Faktoren, die die Maßhaltigkeit von Feingussteilen beeinflussen
Die ständige Verbesserung der Maßhaltigkeit von Feingussteilen und die Reduzierung von Abfall durch Übermaß ist seit jeher eines der Hauptziele der Feingussarbeiter im In- und Ausland.
1. Maßhaltigkeit von Feingussteilen
1. Dimensionsstabilität des Wachsmodells und seine Einflussfaktoren
In den meisten Fällen schwankt die Größe der Wachsform stark, wenn die Größe des Gussstücks schwankt, und es gibt einige Ausnahmen. Insgesamt macht die Größenschwankung der Wachsform 10 bis 70 % der Größenschwankung des Gussstücks aus.
Die Parameter des Formgebungsprozesses haben einen entscheidenden Einfluss auf die Dimensionsstabilität der Wachsform. Die Hauptfaktoren sind wie folgt:
(1) Wachspresstemperatur
Unterschiedliche Formstoffe haben aufgrund des Einflusses der Wachspresstemperatur unterschiedliche Leistungen. Bei der Verwendung von Formstoffen auf Wachsbasis ist die Wachspresstemperatur sehr empfindlich gegenüber dem Einfluss der Dimensionsstabilität der Wachsform, während Formstoffe auf Harzbasis einen geringeren Einfluss haben.
(2) Einspritzdruck
Bei kleinem Druck nimmt die Schrumpfrate der Wachsform bei steigendem Druck deutlich ab. Nach einer gewissen Druckerhöhung (≥ 1.6 MPa) hat der Druck jedoch fast keinen Einfluss auf die Größe der Wachsform. Kein Wunder, dass ausländische Testergebnisse oft zu dem Schluss kommen, dass „der Druck nichts mit der Größe der Wachsform zu tun hat“, aber der Eindruck vieler inländischer Unternehmen ist nicht ganz derselbe.
(3) Durchflussmenge
Die Fließgeschwindigkeit des Formmaterials kann auf zwei Arten verändert werden, aber der Einfluss auf die Größe der Wachsform ist nicht derselbe:
·Durch die Änderung der Fließgeschwindigkeitseinstellung der Wachspresse hat diese Methode wenig Einfluss auf die Schrumpfung der Wachsform. Bei dünnwandigen Teilen mit komplexen Formen oder Wachsformen mit Kernen hat es jedoch einen wichtigen Einfluss auf die Füll- und Oberflächenqualität.
·Diese Methode hat einen großen Einfluss durch die Änderung der Querschnittsfläche der Wachseinspritzöffnung, da eine Erhöhung der Querschnittsfläche der Wachseinspritzöffnung nicht nur die Wachspresstemperatur senken, sondern auch die Erstarrung verlängern kann Zeit des Formstoffs an der Wachseinspritzöffnung, wodurch die Verdichtung der Wachsform erhöht wird Schwindungsgrad und Oberflächenschwindung werden reduziert.
(4) Injektionszeit
Die sogenannte Injektionszeit umfasst dabei drei Zeiträume Füllen, Verdichten und Halten. Die Füllzeit bezieht sich auf die Zeit, die das Formmaterial benötigt, um den Formhohlraum zu füllen; Verdichtung bezieht sich auf die Zeit vom Füllen des Formteils bis zum Schließen der Wachseinspritzdüse; und Halten bezieht sich auf die Zeit vom Schließen der Wachseinspritzdüse bis zum Auswerfen der Form.
Die Einspritzzeit hat einen wesentlichen Einfluss auf die Schrumpfrate der Wachsform. Dies liegt daran, dass durch Erhöhen der Einspritzzeit mehr Formmaterial in die Kavität gequetscht werden kann und die Wachsform kompakter wird, wodurch die Schrumpfrate verringert wird. Das Gewicht des Wachsmodells nimmt mit der verlängerten Verdichtungszeit zu. Die Verdichtungszeit sollte angemessen sein. Wenn die Verdichtungszeit zu lang ist, ist das Formmaterial an der Wachseinspritzöffnung vollständig erstarrt und die Verdichtung funktioniert nicht. Aus Fig. 4 ist auch ersichtlich, dass bei einer kurzen Einspritzzeit (15–25 s) die Wachspresstemperatur ansteigt und die Schrumpfrate zunimmt; aber wenn die Einspritzzeit auf 25-35 s verlängert wird (unter der Voraussetzung, dass die Füllzeit konstant bleibt, wird die tatsächliche Verdichtungszeit verlängert) Der Einfluss der Wachspresstemperatur wird kleiner; Wenn die Einspritzzeit auf mehr als 35 s ansteigt, tritt die umgekehrte Situation ein, dh wenn die Wachspresstemperatur ansteigt, nimmt stattdessen die Schrumpfungsrate der Wachsform ab. Dieses Phänomen kann dadurch erklärt werden, dass eine Erhöhung der Formmaterialtemperatur und eine Verlängerung der Verdichtungszeit die gleiche Wirkung haben wie eine Erhöhung des Grades der Wachsformverdichtung.
(5) Formtemperatur und Wachspressausrüstung
Die Formtemperatur ist hoch, die Wachsform kühlt langsam ab und die Schrumpfrate nimmt zu. Dies liegt daran, dass sich die Wachsform noch im Formpressen befindet, bevor die Form ausgeworfen wird und die Schrumpfung begrenzt ist, aber nachdem die Form ausgeworfen wurde, kann sie frei schrumpfen. Wenn die Wachsformtemperatur hoch ist, wenn die Form freigegeben wird, ist daher die endgültige Schrumpfrate groß und umgekehrt ist die Schrumpfrate klein.
Ebenso kann das Kühlsystem der Wachspresse einen Einfluss von ca. 0.3% auf die Größe der Wachsform haben.
Schließlich ist hervorzuheben, dass Wachspaste bei der Verwendung von wachsbasierten Formstoffen ein dreiphasiges Koexistenzsystem von fest, flüssig und gasförmig ist. Das Volumenverhältnis zwischen den drei Phasen hat einen großen Einfluss auf die Größe der Wachsform. Das Verhältnis zwischen diesen dreien ist in der tatsächlichen Produktion nicht kontrollierbar, was auch ein wichtiger Grund für die schlechte Dimensionsstabilität von Wachsformen mit wachsbasierten Formstoffen ist.
2. Der Einfluss von Schalenmaterial und Schalenherstellungsprozess auf die Dimensionsstabilität von Gussteilen
Der Einfluss des Formmantels auf die Größe des Gussstücks wird hauptsächlich durch die thermische Ausdehnung und thermische Verformung (Hochtemperaturkriechen) des Formmantels während des Brennens sowie die Einschränkung (Verstopfung) des Formmantels auf die Abkühlschwindung des Gießen.
(1) Wärmeausdehnung der Schale
Hängt hauptsächlich vom Schalenmaterial ab. Unterschiedliche feuerfeste Materialien haben unterschiedliche Expansionsraten. Unter den üblicherweise verwendeten feuerfesten Materialien weist Quarzglas die kleinste Expansionsrate auf, gefolgt von Aluminiumsilikat, und Kieselsäure ist am größten und ungleichmäßigsten. Nach dem Test wird festgestellt, dass die Aluminiumsilikathülle von Raumtemperatur auf 1000 erhitzt werden kann, die Hülle kann eine Ausdehnung von etwa 0.25% erzeugen, was einen geringen Anteil an der Gesamtschwindung der Gussgröße ausmacht. Daher, wenn solche feuerfesten Materialien verwendet werden, ist die Schale Es hat eine bessere Dimensionsstabilität, wie beispielsweise Quarzglas, wird zweifellos besser sein. Wird jedoch Kieselsäure verwendet, schwankt die Größe der Schale stark.
(2) Thermische Verformung (Hochtemperaturkriechen)
Beispielsweise weist eine Schale mit Wasserglas als Bindemittel einen deutlich höheren Kriechgrad bei hohen Temperaturen über 1000°C auf als die von Kieselsol- und Ethylsilikatschalen. Obwohl der geschmolzene Korund selbst eine hohe Feuerfestigkeit aufweist, kann die Brenntemperatur der Schale von mehr als 1000 aufgrund des Vorhandenseins von Verunreinigungen wie Natriumoxid auch Kriechen verursachen, was zu einer schlechten Dimensionsstabilität führt.
(3) Die Zurückhaltung der Formschale auf die Schwindung des Gussstücks – das Zurückweichen und Zusammenfallen der Formschale Dies hängt auch hauptsächlich vom Material der Formschale ab.
Zusammenfassend lässt sich sagen, dass feuerfeste Materialien eine große Rolle beim Einfluss der Schale auf die Größenschwankung des Gussstücks spielen, die Rolle des Bindemittels jedoch nicht vernachlässigt werden kann. Im Gegensatz dazu ist der Einfluss des Schalenherstellungsprozesses gering.
3. Einfluss von Spannungen durch ungleichmäßige Abkühlung von Gussstücken auf die Maßhaltigkeit
Die Abkühlgeschwindigkeit jedes Teils des Gussstücks (einschließlich des Angusssystems) ist unterschiedlich, was thermische Spannungen erzeugt und das Gussstück verformt, wodurch die Dimensionsstabilität beeinträchtigt wird. Dies ist häufig in der tatsächlichen Produktion anzutreffen. Die Reduzierung der Abkühlgeschwindigkeit von Gussteilen und die Verbesserung der Angusskombination sind wirksame Präventionsmaßnahmen.
2. Der Schlüssel zur Verbesserung der Genauigkeit – die Schrumpfrate der Form wird richtig zugewiesen
Die oben erwähnte "Maßstabilität" unterscheidet sich von "Maßgenauigkeit" und "Präzision (Präzision)". Dimensionsstabilität (dh Präzision) ist gleichbedeutend mit Dimensionskonsistenz, spiegelt den Grad der Dimensionsschwankung oder -streuung wider und wird normalerweise durch die Standardabweichung σ gemessen. Die Hauptursache für Dimensionsinstabilität ist eine laxe Prozesssteuerung, die ein zufälliger Fehler ist. Genauigkeit bezieht sich auf den Grad, in dem das arithmetische Mittel vieler Messwerte von der Nenngröße für eine bestimmte Größe am Gussstück abweicht, also die Größe der durchschnittlichen Abweichung. Beim Feinguss ist der Hauptgrund für die schlechte Maßhaltigkeit die falsche Zuordnung der Schrumpfrate bei der Profilierungsauslegung, ein systematischer Fehler, der in der Regel durch wiederholte Reparaturen der Form ausgeglichen wird. Die Maßhaltigkeit (Präzision) ist eine Kombination der beiden oben genannten. Um die Maßhaltigkeit von Gussteilen zu verbessern und das Problem der Produktgrößentoleranzen zu lösen, muss daher nicht nur der Prozess streng kontrolliert werden, um Dimensionsschwankungen zu reduzieren, sondern auch die Schrumpfrate jeder Dimension des Gussteils muss bei der Konstruktion des Profils korrekt zugewiesen werden .
Es ist allgemein bekannt, dass die endgültige Gesamtschwindung von Präzisionsgussteilen eine Kombination aus Wachsform, Legierungsschwindung und einer geringen Schalenexpansion ist. Die Schale quillt um ca. 0.25% auf und ihre Wirkung ist begrenzt. Obwohl die lineare Schwindungsrate der Legierung oft größer ist als die der Wachsform, wirkt sich die durch den Wachspressprozess verursachte Maßschwankung stärker aus. Um die Kosten der Formreparatur und die Schwankung der Gussgröße zu reduzieren, ist es sehr wichtig, die Schrumpfrate der Wachsform zu kontrollieren.
1. Wachsformschrumpfung
Die Schrumpfung der Wachsform sollte gemessen werden, nachdem die Größe der Wachsform vollständig stabilisiert ist. Dies liegt daran, dass die Schrumpfung der Wachsform nach dem Auswerfen der Form nicht vollständig aufhört. Die Größe der Wachsform stabilisiert sich manchmal erst wenige Tage nach dem Auswerfen der Form. Der größte Teil der Schrumpfung des Formmaterials ist jedoch grundsätzlich innerhalb von einer bis mehreren Stunden nach dem Auswerfen der Form abgeschlossen. Die Schrumpfrate der Wachsform hat hauptsächlich folgende Einflussfaktoren:
(1) Art des Formmaterials;
(2) Schnittgröße des Wachsmodells;
Hervorzuheben ist, dass die Querschnittsgröße der Wachsform einen signifikanten Einfluss auf die Schrumpfrate hat. Zum Beispiel die Schrumpfrate eines typischen ungefüllten Formmaterials beim Pressen von Wachsformen unterschiedlicher Dicke. Die Dicke des Abschnitts der Wachsform sollte im Allgemeinen 13 mm nicht überschreiten. Bei einer Dicke von mehr als 13 mm kann die Wandstärke durch Verwendung von Kaltwachsblöcken oder Metallkernen reduziert werden, um den Zweck der Schwindungsreduzierung zu erreichen, was insbesondere bei nicht füllstoffhaltigen Formstoffen wichtig ist.
Hinweis: 1. Die Schrumpfrate des wasserlöslichen Formmaterials beträgt ca. 0.25%;
2. Bei Verwendung von löslichen Kernen, Keramikkernen oder Quarzglasrohren gibt es keine lineare Schrumpfung der Wachsform in Kontakt mit dem Kern;
(3) Kerntypen
Die Hohlraumgröße der Wachsform stimmt zweifellos mit der Form des Kerns überein. Daher ist die Verwendung von Kernen zu einer Möglichkeit geworden, die Maßhaltigkeit des Hohlraums der Wachsform zu verbessern.
2. Legierungsschrumpfung
Die Schrumpfung der Legierung hängt hauptsächlich von folgenden Faktoren ab:
· Typ der Gusslegierung und chemische Zusammensetzung;
· Casting-Geometrie (einschließlich Constraint-Zustand und Abschnittsgröße);
· Gießparameter, wie Gießtemperatur, Manteltemperatur, Abkühlgeschwindigkeit des Gießens usw.;
· Verwendung von Keramikkernen, Quarzglasrohren etc.
Da Gießtemperatur, Manteltemperatur, Abkühlgeschwindigkeit des Gusses und andere Prozessparameter während des Produktionsprozesses in der Regel durch Standardprozesskarten streng kontrolliert werden, sind die dadurch bedingten Größenschwankungen zwischen verschiedenen Produktionschargen nicht groß. Selbst wenn die Gießtemperatur den von der Prozessspezifikation geforderten Bereich überschreitet, ist die Schwankung der Gussgröße normalerweise nicht groß. Ähnlich wie bei der Wachsform sind die Querschnittsgröße des Gussstücks und die Randbedingungen der Formschale die Hauptfaktoren, die die Schwindung der Legierung beeinflussen. Die Erfahrung zeigt, dass die Schrumpfrate der vollständig eingeschränkten Größe 85 % bis 89 % der freien Schrumpfrate beträgt; die semi-eingeschränkte Größe beträgt 94 % bis 95 %.
3. Die Mindestanzahl der ersten Probencharge für die Messung
Bei der oben aufgeführten Schrumpfrate handelt es sich um empirische Daten, die auf Erfahrungen aus der Vergangenheit basieren, nicht auf der tatsächlichen Schrumpfrate. Formen nach diesen Angaben konstruieren und herstellen, Reparaturen sind unumgänglich. Um die Genauigkeit und Erfolgsrate von Reparaturen zu verbessern und die Anzahl der Reparaturen zu reduzieren, ist es wichtig, die Größe einer ausreichenden Anzahl von Probegussmustern sorgfältig zu überprüfen. Da die Größe der von uns hergestellten Gussteile nicht exakt gleich sein kann, kann der erhaltene Mittelwert nur bei einer ausreichend großen Anzahl gemessener Proben nahe am wahren arithmetischen Mittel liegen. Daraus ist nicht schwer zu erkennen, dass die Mindestanzahl an Messproben in direktem Zusammenhang mit der Prozessfähigkeit des Produktionsprozesses steht, um die Produktgrößenkonstanz (Process Capability) zu kontrollieren. Wenn die Gussstücke völlig gleich groß sind, muss nur eine Probe geprüft werden; Umgekehrt, wenn die Gussgröße stark schwankt,
Es ist notwendig, viele Proben zu messen, um genauere Schrumpfungsdaten zu erhalten. Wie bereits erwähnt, kann die Fähigkeit des Herstellungsverfahrens, die Größe zu kontrollieren, durch die 6σ der durch dieses Verfahren hergestellten Gussgröße dargestellt werden. Nach dem derzeitigen technologischen Stand der meisten Investitionsgießereien liegt Hp meist über 0.5, sodass die erste Charge von Messproben in der Regel mindestens 11 Proben erfordert.
drei. Messsystemanalyse
Bei der Analyse und Lösung von Produktgrößenproblemen müssen wir auf die Genauigkeit und Zuverlässigkeit des verwendeten Messsystems achten. Neben der häufigen Kalibrierung von Messgeräten und Geräten selbst ist es auch wichtig, Messfehler zu minimieren. Wenn das Messsystem (einschließlich des Bedieners und der Betriebsmethode) einen großen Fehler aufweist, kann nicht nur der Ausschuss als qualifizierte Produkte bewertet werden, sondern auch viele qualifizierte Produkte können als Ausschuss falsch eingeschätzt werden, was beides zu schweren Unfällen oder unnötiger Wirtschaftlichkeit führen kann Verluste. Der einfachste Weg, um festzustellen, ob ein Messsystem für eine bestimmte Messaufgabe geeignet ist, ist die Durchführung von Reproduzierbarkeits- und Wiederholbarkeits-Qualifizierungstests. Die sogenannte Wiederholbarkeit bedeutet, dass derselbe Prüfer dasselbe Instrument (oder dieselbe Ausrüstung) und dieselbe Methode verwendet, um dasselbe Teil zu prüfen und die Konsistenz der Ergebnisse zu erhalten. Reproduzierbarkeit bezieht sich auf die Konsistenz der Ergebnisse, die von verschiedenen Bedienern mit unterschiedlichen Instrumenten zur Prüfung desselben Teils erzielt wurden. Die American Automotive Industry Action Group (Automotive Industry Action Group) legt fest, dass der prozentuale Anteil der integrierten Standardabweichung von Wiederholbarkeit und Reproduzierbarkeit R&R an der Standardabweichung der gemessenen Gussgrößenschwankungen ≤30% als Standard für das Messsystem zur Erfüllung der Anforderungen [5]. Bei der Messung einiger großformatiger und komplex geformter Gussteile können nicht alle Messsysteme diese Anforderung erfüllen. Der zulässige Messfehler beim Messen von Formen sollte kleiner sein, normalerweise 1/3.
vier. Werkzeugaufbau und Verarbeitungsebene
Es ist bekannt, dass die Formstruktur und die Verarbeitungsqualität einen wichtigen Einfluss auf die Größe und Geometrie der Wachsform haben. Zum Beispiel, ob der Positionierungs- und Spannmechanismus genau und zuverlässig ist, ob das passende Spiel der beweglichen Teile (wie bewegliche Blöcke, Bolzen usw.) , etc. Bei einer beträchtlichen Anzahl von inländischen Feingusswerken muss das Niveau der Formenkonstruktion und Herstellung noch dringend verbessert werden.
Fünfer. abschließend
Aus der obigen Analyse ist nicht schwer zu erkennen, dass die Verbesserung der Maßhaltigkeit von Feingussteilen ein systematisches Projekt ist, das alle Aspekte des Herstellungsprozesses von Feingussteilen umfasst. Die wichtigsten Punkte lassen sich wie folgt zusammenfassen:
1) Kontrollieren Sie streng die Parameter des Formverfahrens, insbesondere die Parameter, die einen erheblichen Einfluss auf die Größe des Gussstücks haben.
2) Wählen Sie das geeignete Schalenmaterial.
3) Sammeln, zählen und analysieren Sie die Schrumpfungsdaten mit einer korrekten Methode, die den statistischen Prinzipien entspricht, um die Genauigkeit der Schrumpfungszuordnung zu verbessern.
4) Überwachen Sie häufig das Messsystem (einschließlich Ausrüstung, Prüfpersonal und Technologie), um sicherzustellen, dass die Wiederholbarkeit und die Reproduzierbarkeitsfehler die spezifizierten Anforderungen erfüllen.
5) Kontinuierliche Verbesserung des Formendesigns und der Herstellung.
6) Maßnahmen wie Gusskorrektur und Stabilisierungswärmebehandlung sind nach wie vor in vielen Fällen unabdingbar
Bitte bewahren Sie die Quelle und Adresse dieses Artikels für den Nachdruck auf: Verschiedene Faktoren, die die Maßhaltigkeit von Feingussteilen beeinflussen
Mingh Druckgussunternehmen sind der Herstellung und Bereitstellung von hochwertigen und leistungsstarken Gussteilen gewidmet (das Angebot an Metalldruckgussteilen umfasst hauptsächlich) Dünnwandiger Druckguss,Heißkammerdruckguss,Kaltkammerdruckguss), Runder Service (Druckguss-Service,CNC-Bearbeitung,Formenbau,Oberflächenbehandlung). Alle kundenspezifischen Aluminium-Druckguss-, Magnesium- oder Zamak/Zink-Druckguss- und andere Gussanforderungen können uns gerne kontaktieren.
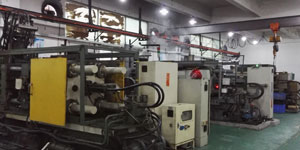
Unter der Kontrolle von ISO9001 und TS 16949 werden alle Prozesse durch Hunderte von fortschrittlichen Druckgussmaschinen, 5-Achsen-Maschinen und anderen Einrichtungen durchgeführt, von Blasgeräten bis hin zu Ultraschall-Waschmaschinen.Minghe verfügt nicht nur über fortschrittliche Ausrüstung, sondern auch über professionelle Team aus erfahrenen Ingenieuren, Bedienern und Inspektoren, um das Design des Kunden zu verwirklichen.
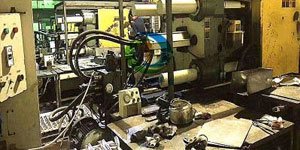
Auftragsfertigung von Druckgussteilen. Zu den Fähigkeiten gehören Kaltkammer-Aluminium-Druckgussteile von 0.15 lbs. bis 6 lbs., Schnellwechseleinrichtung und Bearbeitung. Mehrwertdienste umfassen Polieren, Vibrieren, Entgraten, Kugelstrahlen, Lackieren, Plattieren, Beschichten, Montage und Werkzeugbau. Zu den Materialien, mit denen gearbeitet wird, gehören Legierungen wie 360, 380, 383 und 413.
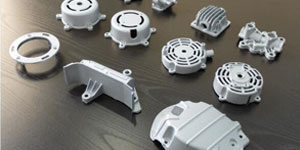
Unterstützung bei der Konstruktion von Zinkdruckguss / gleichzeitige Engineering-Dienstleistungen. Auftragsfertigung von Präzisions-Zink-Druckgussteilen. Es können Miniaturgussteile, Hochdruck-Kokillengussteile, Mehrschieber-Kokillengussteile, konventionelle Kokillengussteile, Einzel- und Einzeldruckgussteile sowie hohlraumdichte Gussteile hergestellt werden. Gussteile können in Längen und Breiten bis zu 24 Zoll in +/-0.0005 Zoll Toleranz hergestellt werden.
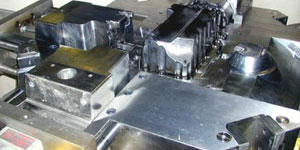
ISO 9001: 2015 zertifizierter Hersteller von Magnesium-Druckguss. Zu den Fähigkeiten gehören Hochdruck-Magnesium-Druckguss bis zu 200 Tonnen Heißkammer und 3000 Tonnen Kaltkammer, Werkzeugdesign, Polieren, Formen, Bearbeitung, Pulver- und Flüssiglackierung, vollständige Qualitätssicherung mit KMG-Fähigkeiten , Montage, Verpackung & Lieferung.
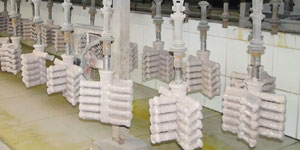
ITAF16949-zertifiziert. Zusätzlicher Casting-Service inklusive Feinguss,Sandguss,Schwerkraftguss, Verlorener Schaumguss,Schleuderguss,Vakuumgießen,Dauerguss,.Zu den Fähigkeiten gehören EDI, technische Unterstützung, Volumenmodellierung und Sekundärverarbeitung.
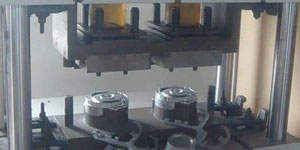
Gussindustrie Teile-Fallstudien für: Autos, Fahrräder, Flugzeuge, Musikinstrumente, Wasserfahrzeuge, optische Geräte, Sensoren, Modelle, elektronische Geräte, Gehäuse, Uhren, Maschinen, Motoren, Möbel, Schmuck, Vorrichtungen, Telekommunikation, Beleuchtung, medizinische Geräte, Fotogeräte, Roboter, Skulpturen, Tongeräte, Sportgeräte, Werkzeuge, Spielzeug und mehr.
Was können wir Ihnen als nächstes helfen?
∇ Zur Startseite gehen für Druckguss China
→Gussteile- Finden Sie heraus, was wir getan haben.
→Bewertete Tipps zu Druckgussdienste
By Minghe Druckgusshersteller |Kategorien: Hilfreiche Artikel |Werkstoff Stichworte: Aluminiumguss, Zinkguss, Magnesiumguss, Titanguss, Edelstahlguss, Messingguss,Bronzeguss,Casting-Video,Unternehmensgeschichte,Aluminiumdruckguss |Kommentare deaktiviert