Mehrere Probleme, die beim Gießen von Natriumsilikatsand beachtet werden sollten
1 Welche Faktoren beeinflussen die „Alterung“ von Wasserglas? Wie kann man die "Alterung" von Wasserglas beseitigen?
Das frisch zubereitete Wasserglas ist eine echte Lösung. Die Kieselsäure im Wasserglas unterliegt jedoch während des Lagerungsprozesses einer Kondensationspolymerisation, die aus der echten Lösung allmählich zu einer makromolekularen Kieselsäurelösung polykondensiert und schließlich zu einem Kieselsäuregel wird. Daher ist Wasserglas eigentlich ein heterogenes Gemisch aus Polykieselsäure mit unterschiedlichen Polymerisationsgraden, das leicht durch Modul, Konzentration, Temperatur, Elektrolytgehalt und Lagerzeit beeinflusst wird.
Während der Lagerung durchlaufen die Moleküle des Wasserglases eine Kondensationspolymerisation, um ein Gel zu bilden, und seine Haftfestigkeit nimmt mit der Verlängerung der Lagerzeit allmählich ab. Dieses Phänomen wird als "Alterung" von Wasserglas bezeichnet.
Das Phänomen "Alterung" kann durch die folgenden beiden Testdatensätze erklärt werden: Hochmoduliges Wasserglas (M=2.89, ρ=1.44g/cm3) nach 20, 60, 120, 180, 240 Tagen Lagerung, das CO2 ausgehärtet Wasserglas wird geblasen Die Trockenzugfestigkeit von Sand sinkt entsprechend um 9.9%, 14%, 23.5%, 36.8% und 40%; Natriumsilikat mit niedrigem Modul (M = 2.44, ρ = 1.41 g/cm3) wird nach dem Trocknen 7, 30, 60 und 90 Tage gelagert. Die Zugfestigkeit nahm um 4.5%, 5%, 7.3% bzw. 11% ab.
Die Lagerzeit von Wasserglas hat einen geringen Einfluss auf die Anfangsfestigkeit von estergehärtetem Wasserglas-Selbsthärtesand, aber sie hat einen erheblichen Einfluss auf die spätere Festigkeit. Bei hochmoduligem Wasserglas wird er laut Messungen um ca. 60 % und bei niedermoduligem Wasserglas um 15-20 % reduziert. . Auch die Restfestigkeit nimmt mit der Verlängerung der Lagerzeit ab.
Während der Lagerung von Wasserglas laufen die Polykondensation und Depolymerisation der Polykieselsäure gleichzeitig ab, das Molekulargewicht wird disproportioniert und schließlich entsteht ein mehrfach dispergiertes System, in dem Monoorthokieselsäure und kolloidale Partikel koexistieren. Das heißt, während des Alterungsprozesses von Wasserglas wird der Polymerisationsgrad der Kieselsäure disproportioniert und der Gehalt an Monoorthokieselsäure und Hochpolykieselsäure steigt mit der Verlängerung der Lagerzeit. Als Folge der Kondensations- und Depolymerisationsreaktion von Wasserglas während der Lagerung wird die Haftfestigkeit verringert, dh es tritt das Phänomen der "Alterung" auf.
Die Hauptfaktoren, die die "Alterung" von Wasserglas beeinflussen, sind: Lagerzeit, Modul und Konzentration von Wasserglas. Je länger die Lagerzeit, desto höher der Modul und je höher die Konzentration, desto gravierender die "Alterung".
Das schon lange bestehende Wasserglas kann auf vielfältige Weise modifiziert werden, um die „Alterung“ zu beseitigen und dem Wasserglas wieder die Leistung von Süßwasserglas zu verleihen:
1. Physische Modifikation
Die Alterung von Wasserglas ist ein spontaner Prozess, der langsam Energie freisetzt. Die physikalische Modifikation von "gealtertem" Wasserglas besteht darin, ein Magnetfeld, Ultraschall, Hochfrequenz oder Erhitzen zu verwenden, um dem Wasserglassystem Energie zuzuführen und die Hochpolymerisation des Polysilikatklebers zu fördern. Die Partikel depolymerisieren erneut und fördern die Homogenisierung des Molekulargewichts der Polykieselsäure, wodurch das Alterungsphänomen, das der Mechanismus der physikalischen Modifikation ist, beseitigt wird. So wird beispielsweise nach der Behandlung mit einem Magnetfeld die Festigkeit von Natriumsilikatsand um 20-30% erhöht, die Zugabemenge von Natriumsilikat um 30-40% reduziert, CO2 eingespart, die Kollabierbarkeit verbessert und es gibt gute Wirtschaftliche Vorteile.
Der Nachteil der physikalischen Modifizierung besteht darin, dass sie nicht dauerhaft ist und die Haftfestigkeit bei Lagerung nach der Behandlung nachlässt, sodass sie so schnell wie möglich nach der Behandlung in der Gießerei verwendet werden kann. Insbesondere bei Wasserglas mit M > 2.6 ist die Konzentration der Kieselsäuremoleküle groß und nach der physikalischen Modifizierung und Depolymerisation wird es relativ schnell polykondensieren. Am besten sofort nach der Behandlung anwenden.
2. Chemische Modifikation
Die chemische Modifizierung besteht darin, dem Wasserglas eine geringe Menge an Verbindungen zuzusetzen. Diese Verbindungen enthalten alle Carboxyl-, Amid-, Carbonyl-, Hydroxy-, Ether-, Amino- und andere polare Gruppen, die an Kieselsäuremolekülen oder kolloidalen Partikeln durch Wasserstoffbrücken oder statisch adsorbiert werden Elektrizität. Oberfläche, ändern ihre potentielle Oberflächenenergie und Solvatationsfähigkeit, verbessern die Stabilität von Polykieselsäure, wodurch das Fortschreiten der "Alterung" verhindert wird.
Bessere Ergebnisse können beispielsweise durch die Zugabe von Polyacrylamid, modifizierter Stärke, Polyphosphat etc. zum Wasserglas erzielt werden.
Das Einbringen von organischem Material in gewöhnliches Wasserglas oder sogar modifiziertes Wasserglas kann eine Vielzahl von Funktionen erfüllen, wie zum Beispiel: Änderung der viskosen Fließeigenschaften von Wasserglas; Verbesserung der Modellierleistung von Wasserglasmischungen; Erhöhung der Klebkraft, um das Wasserglas absolut additiv zu machen Die Menge wird reduziert; die Plastizität des Kieselsäuregels wird verbessert; die Restfestigkeit wird reduziert, so dass sich der Wasserglassand besser für Gusseisen und NE-Legierungen eignet.
3. Physikalisch-chemische Modifikation
Die physikalische Modifizierung ist für "gealtertes" Wasserglas geeignet und kann nach der Modifizierung sofort verwendet werden. Die chemische Modifizierung ist für die Verarbeitung von Süßwasserglas geeignet und das modifizierte Wasserglas ist lange lagerfähig. Durch die Kombination von physikalischer Modifikation und chemischer Modifikation kann das Wasserglas nachhaltig modifizierend wirken. Gute Wirkung hat beispielsweise die Zugabe von Polyacrylamid in den Autoklaven zur Modifizierung des "alternden" Wasserglases. Darunter werden der Druck und der Druck des Autoklaven verwendet. Rühren ist eine physikalische Modifikation und die Zugabe von Polyacrylamid ist eine chemische Modifikation.
2 Wie verhindert man das Auskreiden der Oberfläche von gehärtetem Natriumsilikatsand (Kern) durch CO2-Blasen?
Nachdem Soda-Natrium-Silikat-Sand geblasen wurde, CO2 gehärtet und für eine gewisse Zeit belassen wurde, erscheint manchmal eine Substanz wie Raureif auf der Oberfläche der unteren Form (Kern), die die Oberflächenfestigkeit des Ortes ernsthaft verringert und leicht Sand produziert Waschfehler beim Gießen. Der Hauptbestandteil dieser weißen Substanz ist laut Analyse NaHCO3, die durch übermäßige Feuchtigkeit oder CO2 im Natriumsilikatsand verursacht werden kann. Die Reaktion ist wie folgt:
Na2CO3+H2O→NaHCO3+NaOH
Na2O+2CO2+H2O→2NaHCO3
NaHCO3 wandert leicht mit Feuchtigkeit nach außen und verursacht pulverförmigen Reif auf der Oberfläche der Form und des Kerns.
Die Lösung lautet wie folgt:
1. Kontrollieren Sie den Feuchtigkeitsgehalt des Natriumsilikatsandes nicht zu hoch (insbesondere in der Regenzeit und im Winter).
2. Die Zeit zum Einblasen von CO2 sollte nicht zu lang sein.
3. Die ausgehärtete Form und der Kern sollten nicht für längere Zeit platziert und rechtzeitig geformt und gegossen werden.
4. Die Zugabe von ca. 1% (Massenanteil) des Sirups mit einer Dichte von 1.3 g/cm3 zum Natriumsilikatsand kann die Pulverisierung der Oberfläche wirksam verhindern.
3 Wie kann die Feuchtigkeitsaufnahmebeständigkeit der Wasserglas-Sandform (Kern) verbessert werden?
Der durch CO2- oder Heizmethoden gehärtete Sodawasserglas-Sandkern wird in die nasse Tonform montiert. Wenn es nicht rechtzeitig gegossen wird, nimmt die Festigkeit des Sandkerns stark ab, kann nicht nur kriechen, sogar kollabieren; es wird in einer feuchten Umgebung gelagert. Auch die Festigkeit des Sandkerns wird deutlich reduziert. Tabelle 1 zeigt den Festigkeitswert des CO2-gehärteten Natriumwasserglas-Sandkerns, wenn er in einer Umgebung mit einer relativen Luftfeuchtigkeit von 97% für 24 Stunden platziert wird. Der Grund für den Festigkeitsverlust bei Lagerung in feuchter Umgebung liegt in der Rehydratisierung von Natronwasserglas. Das Na+ und OH– in der Natriumsilikat-Bindemittelmatrix nehmen Feuchtigkeit auf und erodieren die Matrix, wodurch schließlich die Silizium-Sauerstoff-Bindung Si-O-Si aufgebrochen wird, was zu einer deutlichen Abnahme der Bindungsfestigkeit des Natriumsilikatsandes führt.
1. Natriumwasserglas wird mit Lithiumwasserglas versetzt oder Natriumwasserglas mit Li2CO3, CaCO3, ZnCO3 und anderen anorganischen Zusätzen versetzt, da sich relativ unlösliche Carbonate und Silikate bilden können und freie Natriumionen reduziert werden können Absorptionsbeständigkeit des Natriumwasserglas-Bindemittels kann verbessert werden.
2. Fügen Sie dem Natriumwasserglas eine kleine Menge organisches Material oder organisches Material mit Tensidfunktion hinzu. Wenn das Bindemittel ausgehärtet ist, können die hydrophilen Na+- und OH–-Ionen in dem Natriumwasserglasgel durch organische hydrophobe Gruppen ersetzt werden, oder miteinander kombiniert verbessert die freiliegende organische hydrophobe Basis die Feuchtigkeitsaufnahme.
3. Verbessern Sie den Modul von Wasserglas, da die Feuchtigkeitsbeständigkeit von Wasserglas mit hohem Modul stärker ist als die von Wasserglas mit niedrigem Modul.
4. Stärkehydrolysat zu Natriumsilikatsand hinzufügen. Ein besseres Verfahren besteht darin, Stärkehydrolysat zu verwenden, um Natriumwasserglas zu modifizieren.
4 Was sind die Merkmale des CO2-blasenden gehärteten Wasserglas-Alkali-Phenolharz-Sand-Verbundverfahrens?
Um die Qualität von Stahlgussteilen zu verbessern, müssen in den letzten Jahren einige kleine und mittlere Unternehmen dringend das Harz-Sand-Verfahren übernehmen. Aufgrund der begrenzten wirtschaftlichen Kapazität können sie jedoch keine Harzsand-Regenerationsausrüstung kaufen und der Altsand kann nicht recycelt werden, was zu hohen Produktionskosten führt. Um einen effektiven Weg zu finden, um die Qualität von Gussstücken zu verbessern, ohne die Kosten zu stark zu erhöhen, können die Prozesseigenschaften von CO2-Blasen von gehärtetem Natriumsilikatsand und CO2-Blasen von gehärtetem alkalischem Phenolharzsand kombiniert werden, und CO2-Blasen von gehärtetem Natriumsilikat – alkalisch Phenolharz verwendet werden. Der Harzsand-Compoundierprozess verwendet alkalischen Phenolharzsand als Oberflächensand und Wasserglassand als Hintersand, während CO2 zum Aushärten eingeblasen wird.
Das in CO2-alkalischem Phenolharzsand verwendete Phenolharz wird durch Polykondensation von Phenol und Formaldehyd unter Einwirkung eines stark alkalischen Katalysators und Zugabe eines Haftvermittlers hergestellt. Sein pH-Wert beträgt ≥13 und seine Viskosität beträgt ≤500mPa•s. Die dem Sand zugesetzte Menge an Phenolharz beträgt 3 bis 4 % (Massenanteil). Wenn die CO2-Flussrate 0.8~1.0m3/h beträgt, beträgt die beste Blaszeit 30~60s; wenn die Blaszeit zu kurz ist, ist die Härtefestigkeit des Sandkerns gering; Wenn die Blaszeit zu lang ist, erhöht sich die Festigkeit des Sandkerns nicht und es handelt sich um verschwendetes Gas.
CO2 – Alkalischer Phenolharzsand enthält keine schädlichen Elemente wie N, P, S usw., so dass Gussfehler wie Poren, Oberflächenmikrorisse usw., die durch diese Elemente verursacht werden, beseitigt werden; schädliche Gase wie H2S und SO2 werden beim Gießen nicht freigesetzt, was dem Umweltschutz zugute kommt ; Gute Zusammenfaltbarkeit, leicht zu reinigen; hohe Maßgenauigkeit; hohe Produktionseffizienz.
Das CO2-blasende gehärtete Wasserglas-alkalische Phenolharz-Sand-Verbundverfahren kann in großem Umfang bei Stahlguss, Eisenguss, Kupferlegierungen und Leichtmetallguss verwendet werden.
Das Verbundverfahren ist ein einfaches und bequemes Verfahren. Das Verfahren ist wie folgt: Zuerst Harzsand und Natriumsilikatsand getrennt mischen und dann in zwei Sandeimer geben; dann fügen Sie den gemischten Harzsand als Oberflächensand in den Sandkasten hinzu Und Pfund, die Dicke der Oberflächensandschicht beträgt im Allgemeinen 30-50 mm; dann wird Wasserglassand hinzugefügt, um den hinteren Sand zu füllen und zu verdichten; Zum Aushärten wird schließlich CO2-Gas in die Form geblasen.
Der Durchmesser des Blasrohrs beträgt im Allgemeinen 25 mm und der härtbare Bereich beträgt etwa das 6-fache des Durchmessers des Blasrohrs.
Die Blaszeit hängt von der Größe, Form, Gasströmung und Fläche des Auspuffstopfens der Sandform (Kern) ab. Im Allgemeinen wird die Blaszeit innerhalb von 15 bis 40 Sekunden gesteuert.
Nach dem Blasen der harten Sandform (Kern) kann die Form entnommen werden. Die Festigkeit der Sandform (Kern) steigt schnell an. Bürsten Sie die Farbe innerhalb einer halben Stunde nach dem Entnehmen der Form und schließen Sie die Schachtel zum Gießen nach 4 Stunden.
Das Composite-Verfahren eignet sich besonders für Stahlgussanlagen, die über keine Harzsand-Regenerationsanlagen verfügen und hochwertige Gussteile herstellen müssen. Der Prozess ist einfach und leicht zu kontrollieren, und die Qualität der produzierten Gussteile entspricht der anderer Kunstharz-Sandgussteile.
CO2 blasender gehärteter Natriumsilikatsand kann auch mit CO2 blasendem gehärtetem Natrium-Polyacrylat-Harzsand für die Herstellung verschiedener hochwertiger Gussteile compoundiert werden.
5 Was sind die Vor- und Nachteile des CO2-organischen Ester-Verbundverfahrens mit gehärtetem Natriumsilikatsand?
In den letzten Jahren hat das CO2-organische Ester-Komposit-gehärtete Natriumsilikat-Sand-Verfahren einen Trend zu zunehmenden Anwendungen gefunden. Das Verfahren ist wie folgt: Geben Sie während des Sandmischens eine bestimmte Menge organischen Esters hinzu (normalerweise die Hälfte der normalerweise erforderlichen Menge oder 4-6 % des Gewichts von Wasserglas); nach Abschluss des Modellierens CO2 blasen, um die Formtrennfestigkeit zu erreichen (Druckfestigkeit ist im Allgemeinen erforderlich) Die Festigkeit beträgt etwa 0.5 MPa); nach dem Entformen härtet der organische Ester weiter aus und die Festigkeit des Formsandes steigt schneller an; Nachdem das CO2 geblasen und für 3 bis 6 Stunden platziert wurde, kann die Sandform kombiniert und gegossen werden.
Der Härtungsmechanismus ist:
Wenn der Wasserglassand CO2 bläst, versucht das CO2-Gas unter der Wirkung des Gasdruckunterschieds und des Konzentrationsunterschieds, in alle Richtungen des Formsands zu strömen. Nach dem Kontakt des CO2-Gases mit dem Wasserglas reagiert es sofort mit diesem zu einem Gel. Durch den Diffusionseffekt erfolgt die Reaktion immer von außen nach innen und die äußere Schicht bildet zunächst einen Gelfilm, der verhindert, dass das CO2-Gas und das Wasserglas weiter reagieren. Daher ist es in kurzer Zeit, egal welche Methode zur Kontrolle von CO2-Gas verwendet wird, unmöglich, es mit allen Wassergläsern reagieren zu lassen. Laut Analyse, wenn der Formsand die beste Blasstärke erreicht, beträgt der mit CO2-Gas umgesetzte Wasserglasanteil etwa 65 %. Das bedeutet, dass das Wasserglas seine Haftwirkung nicht vollständig entfaltet und mindestens 35 % des Wasserglases nicht reagieren. Der organische Esterhärter kann mit dem Bindemittel eine gleichmäßige Mischung bilden und die Bindungswirkung des Bindemittels voll entfalten. Alle Teile des Kernsandes bauen mit gleicher Geschwindigkeit Festigkeit auf.
Eine Erhöhung der Menge an hinzugefügtem Wasserglas erhöht die Endfestigkeit der Sandform, aber auch ihre Restfestigkeit erhöht sich, was die Reinigung des Sandes erschwert. Bei einer zu geringen Zugabemenge an Wasserglas ist die Endfestigkeit zu gering und kann die Anwendungsanforderungen nicht erfüllen. Bei der tatsächlichen Produktion wird die Menge an zugegebenem Wasserglas im Allgemeinen auf etwa 4% kontrolliert.
Bei alleiniger Verwendung von organischem Ester zum Härten beträgt die allgemeine Menge an zugesetztem organischem Ester 8-15% der Menge an Wasserglas. Bei der Komposithärtung wird geschätzt, dass etwa die Hälfte des Wasserglases beim Blasen von CO2 ausgehärtet ist und etwa die Hälfte des Wasserglases noch nicht ausgehärtet ist. Daher ist es zweckmäßiger, wenn die Menge an organischen Estern 4 bis 6 % der Menge an Wasserglas ausmacht.
Die Verbundhärtungsmethode kann die doppelten Vorteile der CO2-Härtung und der organischen Esterhärtung voll ausspielen und die Bindungswirkung von Wasserglas voll ausschöpfen, um eine schnelle Härtungsgeschwindigkeit, eine frühe Entformung, hohe Festigkeit, gute Zusammendrückbarkeit und niedrige Kosten zu erreichen. Umfassende Wirkung.
Allerdings muss beim CO2-organischen Ester-Composite-Härtungsprozess 0.5 bis 1 % mehr Wasserglas zugegeben werden als bei der einfachen organischen Ester-Härtungsmethode, was die Regenerierung des gebrauchten Wasserglassandes erschwert.
6 Warum ist es einfach, klebrigen Sand herzustellen, wenn das Natriumsilikat-Sand-Verfahren zur Herstellung von Eisenguss verwendet wird? Wie kann man es verhindern?
Wenn die Sandform (Kern) aus Natriumsilikatsand zum Gießen von Eisengussteilen verwendet wird, wird oft stark klebriger Sand erzeugt, was seine Anwendung bei der Herstellung von Gusseisen einschränkt.
Das Na2O, SiO2 im Natriumsilikatsand und das vom flüssigen Metall beim Gießen entstehende Eisenoxid bilden niedrigschmelzendes Silikat. Wenn diese Verbindung, wie bereits erwähnt, mehr schmelzbares amorphes Glas enthält, ist die Bindungskraft zwischen dieser Glasschicht und der Oberfläche des Gussstücks sehr gering, und der Schrumpfungskoeffizient unterscheidet sich von dem des Metalls. Große Spannungen können leicht von der Oberfläche des Gussstücks entfernt werden, ohne dass Sand haften bleibt. Wenn die auf der Oberfläche des Gussstücks gebildete Verbindung einen hohen Gehalt an SiO2 und einen niedrigen Gehalt an FeO, MnO usw. aufweist, hat seine erstarrte Struktur im Wesentlichen eine kristalline Struktur, die fest mit dem Gussstück verbunden wird, was zu klebrigem Sand führt .
Wenn der Natriumsilikatsand zur Herstellung von Eisengussteilen verwendet wird, werden Eisen und Mangan aufgrund der niedrigen Gießtemperatur und des hohen Kohlenstoffgehalts der Eisengussteile nicht leicht oxidiert, und die resultierende klebrige Sandschicht hat eine kristalline Struktur, und es ist schwierig um eine geeignete Schicht zwischen den Eisengussteilen und der klebrigen Sandschicht herzustellen. Die Dicke der Eisenoxidschicht unterscheidet sich vom Harzsand zwischen dem Gussteil und der klebrigen Sandschicht, der bei der Herstellung von Eisengussteilen durch Harzpyrolyse einen hellen Kohlenstofffilm erzeugen kann, sodass die klebrige Sandschicht nicht leicht zu entfernen ist.
Um die Bildung von Sodawasserglassand bei der Herstellung von Eisenguss zu verhindern, können geeignete Beschichtungen verwendet werden. Wie bei Farben auf Wasserbasis muss die Oberfläche nach dem Lackieren getrocknet werden, daher ist eine schnell trocknende Farbe auf Alkoholbasis am besten.
Im Allgemeinen können Eisengussteile dem Natriumsilikatsand auch eine entsprechende Menge Kohlenpulver (z ein heller Kohlefilm. Es wird von Metallen und deren Oxiden nicht benetzt, so dass sich die klebrige Sandschicht leicht vom Guss ablösen lässt.
7 Ist zu erwarten, dass Natriumsilikatsand umweltfreundlicher Formsand ohne Abfallsandaustrag wird?
Wasserglas ist farblos, geruchlos und ungiftig. Es verursacht keine ernsthaften Probleme, wenn es Haut und Kleidung berührt und mit Wasser ausgespült wird, aber es muss vermieden werden, in die Augen zu spritzen. Wasserglas hat keine reizenden oder schädlichen Gase, die beim Sandmischen, Modellieren, Härten und Gießen freigesetzt werden, und es gibt keine schwarze und saure Verschmutzung. Wenn das Verfahren jedoch unsachgemäß ist und zu viel Natriumsilikat hinzugefügt wird, ist die Kollabierbarkeit des Natriumsilikatsandes nicht gut und der Staub wird während der Sandreinigung fliegen, was ebenfalls zu Verschmutzungen führt. Gleichzeitig ist es schwierig, Altsand zu regenerieren, und die Entsorgung von Altsand verursacht eine alkalische Belastung der Umwelt.
Wenn diese beiden Probleme überwunden werden können, kann Natriumsilikatsand zu einem umweltfreundlichen Formsand werden, der praktisch ohne Abfallsandaustrag auskommt.
Die grundlegende Maßnahme zur Lösung dieser beiden Probleme besteht darin, die Menge des zugesetzten Wasserglases auf unter 2% zu reduzieren, wodurch der Sand praktisch abgeschüttelt werden kann. Wenn die Wasserglasmenge reduziert wird, wird auch das restliche Na2O im Altsand reduziert. Mit einem relativ einfachen Trockenregenerationsverfahren ist es möglich, den Rest Na2O im zirkulierenden Sand unter 0.25% zu halten. Dieser wiedergewonnene Sand kann die Anwendungsanforderungen von einfachem Formsand für kleine und mittelgroße Stahlgussteile erfüllen. Auch wenn der alte Natriumsilikatsand derzeit nicht im teuren und komplizierten Nassverfahren regeneriert, sondern im relativ einfachen und kostengünstigen Trockenverfahren verwendet wird, kann er vollständig recycelt werden, im Grunde wird kein Altsand ausgetragen, und das Verhältnis von Sand zu Eisen Es kann auf weniger als 1:1 reduziert werden.
8 Wie regeneriert man Natriumsilikatsand effektiv?
Ist der Na2O-Restgehalt im alten Natriumsilikatsand zu hoch, hat der Formsand nach der Zugabe des Natriumsilikats zum Sand nicht genügend Nutzungszeit und die Anreicherung von zu viel Na2O verschlechtert die Feuerfestigkeit des Quarzsandes. Daher sollte das restliche Na2O bei der Regenerierung des gebrauchten Natriumsilikatsandes so weit wie möglich entfernt werden.
Bitte bewahren Sie die Quelle und Adresse dieses Artikels für den Nachdruck auf:Mehrere Probleme, die beim Gießen von Natriumsilikatsand beachtet werden sollten
Mingh Druckgussunternehmen sind der Herstellung und Bereitstellung von hochwertigen und leistungsstarken Gussteilen gewidmet (das Angebot an Metalldruckgussteilen umfasst hauptsächlich) Dünnwandiger Druckguss,Heißkammerdruckguss,Kaltkammerdruckguss), Runder Service (Druckguss-Service,CNC-Bearbeitung,Formenbau,Oberflächenbehandlung). Alle kundenspezifischen Aluminium-Druckguss-, Magnesium- oder Zamak/Zink-Druckguss- und andere Gussanforderungen können uns gerne kontaktieren.
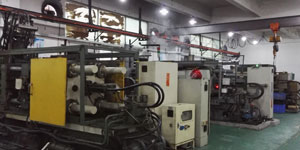
Unter der Kontrolle von ISO9001 und TS 16949 werden alle Prozesse durch Hunderte von fortschrittlichen Druckgussmaschinen, 5-Achsen-Maschinen und anderen Einrichtungen durchgeführt, von Blasgeräten bis hin zu Ultraschall-Waschmaschinen.Minghe verfügt nicht nur über fortschrittliche Ausrüstung, sondern auch über professionelle Team aus erfahrenen Ingenieuren, Bedienern und Inspektoren, um das Design des Kunden zu verwirklichen.
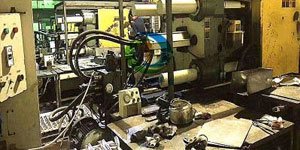
Auftragsfertigung von Druckgussteilen. Zu den Fähigkeiten gehören Kaltkammer-Aluminium-Druckgussteile von 0.15 lbs. bis 6 lbs., Schnellwechseleinrichtung und Bearbeitung. Mehrwertdienste umfassen Polieren, Vibrieren, Entgraten, Kugelstrahlen, Lackieren, Plattieren, Beschichten, Montage und Werkzeugbau. Zu den Materialien, mit denen gearbeitet wird, gehören Legierungen wie 360, 380, 383 und 413.
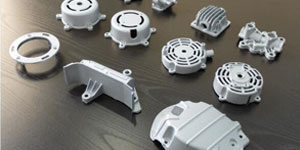
Unterstützung bei der Konstruktion von Zinkdruckguss / gleichzeitige Engineering-Dienstleistungen. Auftragsfertigung von Präzisions-Zink-Druckgussteilen. Es können Miniaturgussteile, Hochdruck-Kokillengussteile, Mehrschieber-Kokillengussteile, konventionelle Kokillengussteile, Einzel- und Einzeldruckgussteile sowie hohlraumdichte Gussteile hergestellt werden. Gussteile können in Längen und Breiten bis zu 24 Zoll in +/-0.0005 Zoll Toleranz hergestellt werden.
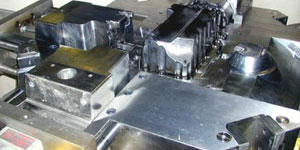
ISO 9001: 2015 zertifizierter Hersteller von Magnesium-Druckguss. Zu den Fähigkeiten gehören Hochdruck-Magnesium-Druckguss bis zu 200 Tonnen Heißkammer und 3000 Tonnen Kaltkammer, Werkzeugdesign, Polieren, Formen, Bearbeitung, Pulver- und Flüssiglackierung, vollständige Qualitätssicherung mit KMG-Fähigkeiten , Montage, Verpackung & Lieferung.
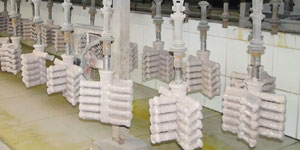
ITAF16949-zertifiziert. Zusätzlicher Casting-Service inklusive Feinguss,Sandguss,Schwerkraftguss, Verlorener Schaumguss,Schleuderguss,Vakuumgießen,Dauerguss,.Zu den Fähigkeiten gehören EDI, technische Unterstützung, Volumenmodellierung und Sekundärverarbeitung.
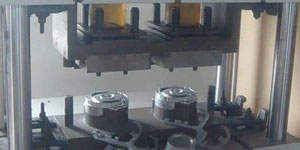
Gussindustrie Teile-Fallstudien für: Autos, Fahrräder, Flugzeuge, Musikinstrumente, Wasserfahrzeuge, optische Geräte, Sensoren, Modelle, elektronische Geräte, Gehäuse, Uhren, Maschinen, Motoren, Möbel, Schmuck, Vorrichtungen, Telekommunikation, Beleuchtung, medizinische Geräte, Fotogeräte, Roboter, Skulpturen, Tongeräte, Sportgeräte, Werkzeuge, Spielzeug und mehr.
Was können wir Ihnen als nächstes helfen?
∇ Zur Startseite gehen für Druckguss China
→Gussteile- Finden Sie heraus, was wir getan haben.
→Bewertete Tipps zu Druckgussdienste
By Minghe Druckgusshersteller |Kategorien: Hilfreiche Artikel |Werkstoff Stichworte: Aluminiumguss, Zinkguss, Magnesiumguss, Titanguss, Edelstahlguss, Messingguss,Bronzeguss,Casting-Video,Unternehmensgeschichte,Aluminiumdruckguss |Kommentare deaktiviert