Wie kann die Stabilität des Grünsandsystems sichergestellt werden?
I. Einleitung
Aufgrund von Änderungen der Produktionsbedingungen und der Umgebung ändern sich unweigerlich andere Parameter des Gussstücks. Wenn der Formsandprozess nicht rechtzeitig angepasst werden kann, wird das Sandsystem instabil, was schließlich zu einer erschwerten Reinigung des Gussteils oder sogar zu Ausschuss führt;
Auf diese Weise ist es notwendig, den ursprünglichen Formsandprozess anzupassen, um das Sandsystem zu stabilisieren; Die stoffliche Zusammensetzung von Formsand besteht hauptsächlich aus Altsand, Rohsand, Bentonit und Additiven. Da mehr als 95 % des Formsandes Altsand ist und der Altsand durch Faktoren wie das unterschiedliche Sand-zu-Eisen-Verhältnis des Gussteils und die unterschiedliche Mischungsmenge des Kernsandes beeinflusst wird, ergeben sich sehr große Schwankungen im die Materialzusammensetzung. Um die Zusammensetzung des Formsandes zu kontrollieren, ist es daher notwendig, den effektiven Bentonitgehalt, den effektiven Additivgehalt und den Schlammgehalt im Formsand zu überprüfen, um die zugegebene Menge an Bentonit, Additiven und Rohsand während des Sandmischens zu bestimmen.
In diesem Artikel wird kurz vorgestellt, wie die Gießerei des Unternehmens des Autors im eigentlichen Produktionsprozess verankert ist.
Je nach Parameteränderung wird der Formsandprozess angepasst, um die Stabilität des Sandsystems zu gewährleisten.
2. Definition der Schlüsselparameter von Formsand:
1. Effektiver Bentonitgehalt: Der effektive Bentonitgehalt (aktiv) wird anhand der Eigenschaften des im Bentonit enthaltenen Montmorillonitminerals bestimmt, das Methylenblau und andere Farbstoffe absorbieren kann; er bezieht sich auf die Titration von 5.00 g Formsand mit 0.20 % Konzentrationsreagenz reiner Methylenblaulösung [ mL]; umgerechnet nach der Standardkurvenformel von Bentonit (%)
2. Effektive Additivdosierung: Sie wird mit der Gasentwicklung von Formsandadditiven verglichen und nach der Formel berechnet; das heißt, die Gasentwicklung von 1.00 g Formsand bei 900 °C [ml] minus der Gasentwicklung des aktivierten Bentonits im Formsand (die durchschnittliche Menge, die vor der Berechnung gemessen wurde) Dann mit 1 g Zusatzgasvolumen (%) vergleichen.
3. Schlammgehalt: Gemäß der nationalen Norm GB/T9442-1998 werden feine Pulverpartikel mit einem Durchmesser von weniger als 20 μm als Schlamm definiert. Der Schlamm wird in der Regel durch das Spülverfahren [2] entfernt.
4. Formsandpartikelgröße: ausgedrückt in AFS-Feinheit, d. h. die durchschnittliche Größe der Sandpartikel wird entsprechend der imaginären Siebmarke wiedergegeben [3];
5. AFS-Feinheitsberechnungsmethode: Die vom American Institute of Foundry vorgeschriebenen AFS-Feinheitsmessverfahren und Berechnungsmethoden sind wie folgt:
. Zunächst ca. 50 g der zu messenden Sandprobe abwiegen, den Schlamm abwaschen, trocknen und dann sieben
. Wiegen und notieren Sie die Qualität der auf jedem Sieb verbleibenden Sandpartikel;
. Berechnen Sie den prozentualen Anteil der auf jedem Sieb verbleibenden Sandpartikelmenge an der Gesamtmenge der Sandproben;
. Multiplizieren Sie den Prozentsatz der auf jedem Sieb verbleibenden Sandpartikelmenge mit dem "AFS-Feinheitsmultiplikator", der jedem Sieb entspricht;
. Addieren Sie die obigen Produkte für jede Siebnummer, um die Summe zu finden:
. Dividieren Sie die in Punkt 5 erhaltene Summe durch die Summe der Prozentsätze an zurückgehaltenem Sand auf jedem Sieb in Punkt 3, um die AFS-Feinheit zu erhalten
3. Anpassungsplan:
Die von der Fabrik verwendete Sandmischanlage ist die Sandmühle DISA und die Formanlage KW statische Druckformanlage; anhand von Datenstatistiken für ein halbes Jahr wurden für seine Formsandanlage folgende Pläne formuliert:
1. Statistik:
① Bestimmen Sie die Menge an Formsand, die jeder Kiste entsprechend dem Einstellwert des Formkörpers hinzugefügt wird, und berechnen Sie das Sand-zu-Eisen-Verhältnis jeder Kiste mit Gussteilen gemäß dem Gewicht jeder Kiste mit Gussteilen und dem Gewicht des Gusses System und die Menge an Kernsand, die beim Gießen verwendet wird;
②Statistik über die ausgetragene Altsandmenge und den Einsatz von Kernsand und Hilfsstoffen
③ Statistik der Entstaubung der Formsandanlage
2. Sandeinstellung:
① Je nach Produktionssituation ist bei kontinuierlicher Produktion eines Gussstücks über zwei oder mehr Tage die Zugabemenge an Formsandzubehör (Bentonit, Additive) festzulegen und die Veränderungen der effektiven Formsandmenge zu zählen, und dann nach und nach während der kontinuierlichen Produktion anderer Gussstücke überprüft Das Verhältnis zwischen Sand-Eisen-Verhältnis und Zugabemenge;
② Einstellung der Partikelgröße des Formsandes: Einstellung nach dem Medianwert von 50/100 Sieb (Kieselsand von 50/100 Sieb, der Medianwert der durchschnittlichen Feinheit beträgt 50 [4]), wenn der AFS des Formsandes . ist kleiner oder gleich 50, durch Zugabe von Feinsand 70/140 oder feineren Neusand 140/70 eingestellt, 30kg-60kg pro Mühle zugegeben und die Veränderung der Partikelgröße analysiert.
③ Anpassung des Schlammgehalts von Formsand: Analyse der Änderung des Schlammgehalts des Formsandsystems durch die Statistik der täglichen Entstaubung;
Viertens der spezifische Anpassungsprozess:
1. Statistik des Verhältnisses von Gusssand zu Eisen:
(Hinweis: Da der X2B1-Zylinderkörper mit integriertem Sandkern gegossen wird, verbrennt er den Formsand nicht, daher wird das Gewicht des äußeren Formsandes des Gussteils mit "0" berechnet)
2. Passen Sie die effektive Menge an das Sand-Eisen-Verhältnis des Gussteils an. Das Sand-zu-Eisen-Verhältnis des 56D-Zylinderblocks beträgt 6.57. Unter den obigen Gussteilen ist das Sand-zu-Eisen-Verhältnis das höchste unter den Zylinderblockgussteilen. Daher wird der 56D-Zylinderblock zuerst getestet:
Wenn 56D an drei aufeinanderfolgenden Tagen hergestellt wurde, betrug die Additivmenge 22 kg/Mill und die Tonadditivmenge 33 kg/Mill; die wirksame Menge an Additiven stieg von 4.55 % auf 5.03 %; die wirksame Tonmenge stieg von 6.56 % auf 7 %; eine Zunahme von etwa 0.5 %; Dies bedeutet, dass bei der Herstellung eines 56D-Zylinders die Zugabemenge höher als der Bilanzwert des Sandsystems eingestellt werden sollte;
Durch die obige Datenanalyse wird die Menge der zugesetzten Hilfsstoffe wie folgt angepasst:
1) Wenn der Zylinder reproduziert wird, wird die Additivmenge auf 19 kg/Million eingestellt, und wenn die Tonadditivmenge 26 kg/Mill beträgt, zeigen Datenstatistiken für drei aufeinanderfolgende Tage, dass sich die effektive Additivmenge von 4.36 % auf 4.29 % geändert hat. ; die effektive Tonmenge hat sich von 4.36 % auf 4.29 % geändert. 7.22 % werden 7.11 %; der effektive Betrag schwankt um 0.1%; daher ist der Prozessanpassungsplan vernünftig und kann das Gleichgewicht des Formsandsystems sicherstellen;
2) In ähnlicher Weise wird die Beziehung zwischen der Menge an Hilfsstoffen, die anderen Gussstücken zugesetzt wird, und der effektiven Menge durch experimentelle Datenanalyse und Theorie berechnet; Passen Sie bei der Reproduktion unterschiedlicher Gussteile die entsprechende Menge der zugesetzten Hilfsstoffe an.
3. Verwenden Sie 70/140 mesh Neusand und 140/70 Neusand, um die Sandgröße anzupassen (der Schlammgehalt des Prototypsands beträgt 11.42%):
① Vom 16. Januar bis 21. Januar insgesamt 4257 Sandschleifzeiten in fünf Tagen, ca. 4257*3/900=14 mal; die Partikelgröße jedes Zyklus ändert sich um 0.26 (pro Mahlung); daher der Formsand am 16. Januar Der AFS-Wert beträgt 49.15; ab 16. Januar, fünf Tage kontinuierlicher Zugabe von 70/140 neuem Sand zur Einstellung der Partikelgröße, 60 kg pro Mill, der AFS-Wert des Formsandes am 21. Januar beträgt 52.84;
② Vom 25. Januar bis 27. Januar insgesamt 2165 Sandschleifzeiten in drei Tagen, ca. 2165*3/900=7 Zyklen; die Korngröße ändert sich bei jedem Zyklus um ca. 0.22 (pro Schleifen); daher, 24. Januar Sand AFS = 52.44, wenn die Partikelgröße des Formsandes 52-53 erreicht, hat die kontinuierliche Zugabe von 70/140 neuem Sand wenig Einfluss auf den AFS des Sandsystems; ab dem 26. Januar werden an drei aufeinanderfolgenden Tagen 140/70 neuer Sand hinzugefügt, um sich anzupassen, und 60 kg werden für jedes Schleifen hinzugefügt. 1 Am 28. beträgt die AFS des Sandes 54.
(Hinweis: ①Der FAW-Unternehmensstandard schreibt vor, dass die Siebrate von 70/140 Quarzsand 70,100,140 ≥80%, davon 70,100 Siebung ≥60%; 140/70 Quarzsand 70,100,140 Siebrate ≥80%, davon 100,140 Siebrate ≥60 % ②Jedes Mahlvolumen beträgt 3 Tonnen und das Systemsandvolumen wird auf 900 Tonnen geschätzt)
4. Vergleich von Schlammgehalt und Staubentfernung für drei aufeinanderfolgende Monate:
Aufgrund des kalten Klimas im Norden von Februar bis März kondensiert und verfestigt sich der Staub in der Kaltentstaubungsleitung, nachdem der heiße Staub entfernt wurde. Wenn die Rohrleitung nicht rechtzeitig gereinigt wird, kommt es häufig zu Verstopfungen und der tägliche Abfluss variiert zwischen 4 und 8 Tonnen. Der Schlammgehalt des Sandsystems schwankt stark. Während dieser Zeit ist die einzige Möglichkeit, die Entstaubungskapazität zu erhöhen und den Schlammgehalt zu reduzieren, die Luftmenge der Entstaubungsanlage zu erhöhen und die Rohre auszubaggern;
Nach Eintritt in den April stieg die Temperatur allmählich an, das Phänomen der Staubkondensation und -verfestigung trat nicht mehr auf, die Staubentfernung stabilisierte sich allmählich und erreichte eine durchschnittliche Abgabe von 7-8 Tonnen pro Tag, und die Schwankungsbreite des Schlammgehalts wurde verringert;
Der Schlammgehalt des Formsandsystems kann auch durch Zugabe von Neusand oder Reduzierung der Zugabe von Hilfsstoffen reduziert werden. Die Nachteile dieser beiden Verfahren werden im Testabschluss erläutert.
5. Testfazit
1. Passen Sie die effektive Menge an Sandzubehör an
Die Bentonitkristalle werden durch Erhitzen bis zu einem gewissen Grad geschädigt und die Nassklebefestigkeit nimmt nach Zugabe von Wasser und Mischen offensichtlich ab. Nach dem Erhitzen bei höherer Temperatur und längerer Zeit wird die Kristallstruktur von Bentonit vollständig zerstört und es wird "toter Ton" ohne Kohäsionskraft. Erhöhte Gussdicke, niedriges Sand-Eisen-Verhältnis, hohe Gießtemperatur und lange Abkühlzeit erhöhen den Brennverlust von Bentonit.
Ob das wirksame Kohlepulver im Formsand ausreicht, lässt sich am direktesten beurteilen, indem man die Glätte der Gussstückoberfläche und das Anhaften von Sand beobachtet. Ein Teil der Kohle im Altsand wird durch die Hitze der gegossenen Metallschmelze verbrannt und muss nachgefüllt werden. Andererseits müssen auch neu hinzugefügte Materialien wie Frischsand, Mischkernsand und Bentonit hinzugefügt werden, um das effektive Kohlenstaubniveau zu erreichen. Die Gesamtmenge des beim Sandmischen zugegebenen Kohlenstaubs ist die Summe aus dem Verbrennungsverlust und der zusätzlichen Zusatzmenge. (Wirksames Kohlepulver entspricht dem wirksamen Zusatz im Text)
2. Einstellung der Sandgröße:
Die Korngröße von Hochdruckformsand beträgt im Allgemeinen 50/140, während die Korngröße von Harzsandkernen meist 50/100 oder gröber ist. Übermäßiges Mischen von Kernsand beeinträchtigt die Vergröberung des gesamten alten nassen Sandes, was die Permeabilität des Sandes erhöht und die Oberfläche des Gussstücks aufrauht.
Damit die Partikelgröße des Formsandes nicht grob wird, können die Partikel aus der Entstaubungsanlage in den Altsand zurückgeführt werden. Oder fügen Sie feinen neuen Sand hinzu, um ihn anzupassen; wie in der Gießerei erwähnt, wenn der AFS des Formsandes etwa 48 erreicht, durch kontinuierliches Hinzufügen von 70/140 oder 140/70 neuem Sand einstellen; jedoch, weil die Gussteile in den Kern des Sandsystems gebrochen werden. Die Sandmenge ist bereits groß. Wenn die Korngröße des Formsandes nicht unerträglich vergröbert wird, ist es nicht empfehlenswert, ständig so viel Neusand zuzugeben, da es sonst andere Leistungsindikatoren des Formsandsystems (Schlammgehalt, Wirkmenge und Festigkeit durch zu viel Neusand). )einfluss haben auf;
3. Anpassung des Schlammgehalts
Die Erhöhung des Schlammgehalts führt dazu, dass die Permeabilität des Formsandes abnimmt und das Phänomen der "Gasexplosion" während des Gießvorgangs auftritt und das Gussstück aufgrund der Explosion und des klebrigen Sandes verschrottet wird. Der Schlammgehalt des Formsandsystems sollte nicht zu hoch sein; der Schlammgehalt des Sandsystems kann durch Verringerung der Menge an Hilfsstoffen verringert werden, aber die Verringerung des effektiven Bentonitgehalts führt dazu, dass die Festigkeit des Formsands abnimmt und die Fähigkeit, Sand aufzuheben und zu widerstehen, verringert wird; die wirksame Dosierung von Decrease führt dazu, dass die Sand-Antihaftfähigkeit des Formsandes abnimmt.
Wenn Sie die Menge an neu hinzugefügtem Sand erhöhen, um den Schlammgehalt anzupassen, berechnen Sie zuerst, wie viel Schlamm die verschiedenen neu hinzugefügten Materialien im Gusssand produzieren, und dann können Sie berechnen, wie viel Rohsand hinzugefügt werden muss, um den Schlammgehalt zu erreichen der Formsand den Verfahrensvorschriften entspricht.
Wie im Artikel erwähnt, kann der Schlammgehalt um 0.1% pro 30 kg Neusand in der Gießerei reduziert werden; die übermäßige Zugabe von Neusand verursacht jedoch nicht nur eine Kostenverschwendung, sondern verringert auch den Anteil an Altsand im Formsandsystem, was die Leistung des Formsandes verringert. , Der Formsand divergiert, was die Formbarkeit des Formsands beeinträchtigt, und das Sandwaschphänomen tritt während des Gießprozesses auf;
Daher ist der Autor der Ansicht, dass es die beste Wahl ist, wenn der Schlammgehalt des Sandsystems durch Einstellen der Entstaubungsausrüstung kontrolliert werden kann.
Insgesamt soll das stabilisierte Sandsystem hochwertige Gussteile herstellen können. Durch dieses Konzept müssen wir den Formsandprozess kontinuierlich den sich ändernden Produktionsbedingungen anpassen, um die Produktionsanforderungen zu erfüllen.
Bitte bewahren Sie die Quelle und Adresse dieses Artikels für den Nachdruck auf: Wie kann die Stabilität des Grünsandsystems sichergestellt werden?
Mingh Druckgussunternehmen sind der Herstellung und Bereitstellung von hochwertigen und leistungsstarken Gussteilen gewidmet (das Angebot an Metalldruckgussteilen umfasst hauptsächlich) Dünnwandiger Druckguss,Heißkammerdruckguss,Kaltkammerdruckguss), Runder Service (Druckguss-Service,CNC-Bearbeitung,Formenbau,Oberflächenbehandlung). Alle kundenspezifischen Aluminium-Druckguss-, Magnesium- oder Zamak/Zink-Druckguss- und andere Gussanforderungen können uns gerne kontaktieren.
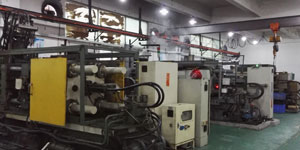
Unter der Kontrolle von ISO9001 und TS 16949 werden alle Prozesse durch Hunderte von fortschrittlichen Druckgussmaschinen, 5-Achsen-Maschinen und anderen Einrichtungen durchgeführt, von Blasgeräten bis hin zu Ultraschall-Waschmaschinen.Minghe verfügt nicht nur über fortschrittliche Ausrüstung, sondern auch über professionelle Team aus erfahrenen Ingenieuren, Bedienern und Inspektoren, um das Design des Kunden zu verwirklichen.
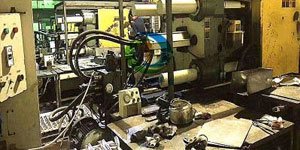
Auftragsfertigung von Druckgussteilen. Zu den Fähigkeiten gehören Kaltkammer-Aluminium-Druckgussteile von 0.15 lbs. bis 6 lbs., Schnellwechseleinrichtung und Bearbeitung. Mehrwertdienste umfassen Polieren, Vibrieren, Entgraten, Kugelstrahlen, Lackieren, Plattieren, Beschichten, Montage und Werkzeugbau. Zu den Materialien, mit denen gearbeitet wird, gehören Legierungen wie 360, 380, 383 und 413.
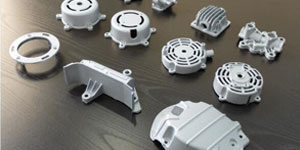
Unterstützung bei der Konstruktion von Zinkdruckguss / gleichzeitige Engineering-Dienstleistungen. Auftragsfertigung von Präzisions-Zink-Druckgussteilen. Es können Miniaturgussteile, Hochdruck-Kokillengussteile, Mehrschieber-Kokillengussteile, konventionelle Kokillengussteile, Einzel- und Einzeldruckgussteile sowie hohlraumdichte Gussteile hergestellt werden. Gussteile können in Längen und Breiten bis zu 24 Zoll in +/-0.0005 Zoll Toleranz hergestellt werden.
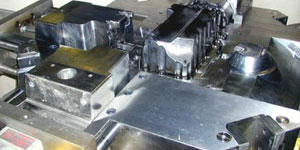
ISO 9001: 2015 zertifizierter Hersteller von Magnesium-Druckguss. Zu den Fähigkeiten gehören Hochdruck-Magnesium-Druckguss bis zu 200 Tonnen Heißkammer und 3000 Tonnen Kaltkammer, Werkzeugdesign, Polieren, Formen, Bearbeitung, Pulver- und Flüssiglackierung, vollständige Qualitätssicherung mit KMG-Fähigkeiten , Montage, Verpackung & Lieferung.
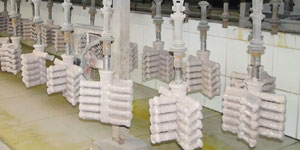
ITAF16949-zertifiziert. Zusätzlicher Casting-Service inklusive Feinguss,Sandguss,Schwerkraftguss, Verlorener Schaumguss,Schleuderguss,Vakuumgießen,Dauerguss,.Zu den Fähigkeiten gehören EDI, technische Unterstützung, Volumenmodellierung und Sekundärverarbeitung.
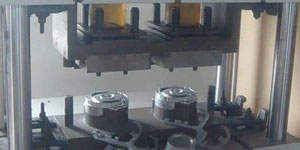
Gussindustrie Teile-Fallstudien für: Autos, Fahrräder, Flugzeuge, Musikinstrumente, Wasserfahrzeuge, optische Geräte, Sensoren, Modelle, elektronische Geräte, Gehäuse, Uhren, Maschinen, Motoren, Möbel, Schmuck, Vorrichtungen, Telekommunikation, Beleuchtung, medizinische Geräte, Fotogeräte, Roboter, Skulpturen, Tongeräte, Sportgeräte, Werkzeuge, Spielzeug und mehr.
Was können wir Ihnen als nächstes helfen?
∇ Zur Startseite gehen für Druckguss China
→Gussteile- Finden Sie heraus, was wir getan haben.
→Bewertete Tipps zu Druckgussdienste
By Minghe Druckgusshersteller |Kategorien: Hilfreiche Artikel |Werkstoff Stichworte: Aluminiumguss, Zinkguss, Magnesiumguss, Titanguss, Edelstahlguss, Messingguss,Bronzeguss,Casting-Video,Unternehmensgeschichte,Aluminiumdruckguss |Kommentare deaktiviert