Das Schmelzwissen von Druckgusslegierungen
Die physikalischen und chemischen Phänomene des Schmelzprozesses
Das Schmelzen von Legierungen ist ein wichtiger Teil des Druckgussprozesses. Der Schmelzprozess besteht nicht nur darin, geschmolzenes Metall zu erhalten, sondern, was noch wichtiger ist, eine chemische Zusammensetzung zu erhalten, die den Anforderungen entspricht, so dass das Druckgussteil eine gute Kristallstruktur und ein Metall mit sehr kleinen Gasen und Einschlüssen erhalten kann.
Während des Schmelzprozesses führt die Wechselwirkung zwischen Metall und Gas und die Wechselwirkung zwischen geschmolzenem Metall und Tiegel zu Veränderungen in der Zusammensetzung, was zu Einschlüssen und Inhalation führt. Daher ist die Formulierung der richtigen Schmelzprozessvorschriften und deren strikte Umsetzung ein wichtiger Garant für den Erhalt hochwertiger Gussteile.
1. Wechselwirkung zwischen Metall und Gas
Beim Schmelzprozess treten als Gase Wasserstoff (H2), Sauerstoff (O2), Wasserdampf (H2O), Stickstoff (N2), CO2, CO usw. auf. Diese Gase lösen sich entweder in der Metallschmelze auf oder reagieren mit ihnen. Wirkung.
2. Die Quelle des Gases
Gas kann aus Ofengas, Ofenauskleidung, Rohstoffen, Flussmitteln, Werkzeugen usw. in die Legierungsflüssigkeit eindringen.
3. Die Wechselwirkung zwischen Metall und Tiegel
Wenn die Schmelztemperatur zu hoch ist, reagiert der Eisentiegel schnell mit der Zinkflüssigkeit, und an der Oberfläche des Tiegels findet eine Eisenoxidationsreaktion statt, um Oxide wie Fe2O3 zu bilden; Darüber hinaus reagiert das Element Eisen auch mit der Zinkflüssigkeit zu einer FeZn13-Verbindung (Zinkschlacke), die in der Zinkflüssigkeit gelöst wird. Die Wandstärke des Eisentiegels wird bis zur Verschrottung kontinuierlich reduziert.
Schmelztemperaturkontrolle
1. Druckgusstemperatur
Der Schmelzpunkt der für den Druckguss verwendeten Zinklegierung beträgt 382 ~ 386 ° C, und die richtige Temperaturkontrolle ist ein wichtiger Faktor bei der Kontrolle der Zusammensetzung der Zinklegierung. Um die gute Fließfähigkeit der Legierungsflüssigkeit zum Füllen des Hohlraums zu gewährleisten, beträgt die Temperatur des geschmolzenen Metalls im Zinktopf der Druckgussmaschine 415 ~ 430 ° C. Die obere Grenze der Druckgusstemperatur von dünnwandigen und komplexen Teilen kann angenommen werden; die untere Grenze von dickwandigen und einfachen Teilen kann übernommen werden. Die Temperatur des geschmolzenen Metalls im zentralen Schmelzofen beträgt 430 ~ 450℃. Die Temperatur der in den Schwanenhals eintretenden Metallschmelze entspricht im Wesentlichen der Temperatur im Zinktopf.
Die Gießtemperatur kann genau kontrolliert werden, indem die Temperatur des geschmolzenen Zinks im Zinktopf kontrolliert wird und erreicht wird:
- ① Das geschmolzene Metall ist eine saubere Flüssigkeit ohne Oxide;
- ② Die Gießtemperatur schwankt nicht.
Schaden durch Übertemperatur:
- ① Verbrennen von Aluminium- und Magnesiumelementen.
- ② Die Oxidationsgeschwindigkeit des Metalls nimmt zu, der Brennverlust nimmt zu und die Zinkschlacke nimmt zu.
- ③ Der Effekt der Wärmeausdehnung führt zum Verklemmen des Hammerkopfes.
- ④ Im Gusstiegel wird mehr Eisen in die Legierung eingeschmolzen und die Reaktion zwischen Zink und Eisen bei hohen Temperaturen beschleunigt. Es bilden sich harte Partikel aus intermetallischen Eisen-Aluminium-Verbindungen, die einen übermäßigen Verschleiß an Hammerkopf und Schwanenhals verursachen.
- ⑤ Der Kraftstoffverbrauch erhöht sich entsprechend.
Zu niedrige Temperatur: Die Legierung hat eine schlechte Fließfähigkeit, was der Umformung nicht förderlich ist und die Oberflächenqualität von Druckgussteilen beeinträchtigt.
Aktuelle Schmelztöpfe oder Öfen von Druckgussmaschinen sind mit Temperaturmess- und Regelsystemen ausgestattet. In der täglichen Arbeit dienen regelmäßige Inspektionen hauptsächlich dazu, die Genauigkeit von Temperaturmessgeräten sicherzustellen. Tragbare Thermometer (Thermometer) werden verwendet, um die tatsächliche Temperatur des Ofens regelmäßig zu messen und zu korrigieren.
Erfahrene Druckguss-Gewerkschaften beobachten die Schmelze mit bloßem Auge. Wenn die Schmelze nach dem Schaben nicht zu viskos und klar ist, steigt die Schlacke nicht schnell auf, was auf eine angemessene Temperatur hinweist; wenn die Schmelze zu viskos ist, weist dies auf eine niedrige Temperatur hin; Nach der Schlacke bildet sich auf der Flüssigkeitsoberfläche eine Reifschicht, und die Schlacke steigt zu schnell an, was darauf hindeutet, dass die Temperatur zu hoch ist und rechtzeitig angepasst werden sollte.
2. So halten Sie die Temperatur stabil
- ① Eine der besten Methoden: Verwenden Sie einen zentralen Schmelzofen und einen Druckgussmaschinenofen als Warmhalteofen, um große Temperaturänderungen zu vermeiden, wenn der Zinkbarren direkt zum Schmelzen in den Zinktopf gegeben wird. Konzentriertes Schmelzen kann die Stabilität der Legierungszusammensetzung sicherstellen.
- ② Die zweitbeste Methode: Die Verwendung eines fortschrittlichen automatischen Zufuhrsystems für Metallflüssigkeiten kann eine stabile Zufuhrgeschwindigkeit, die Temperatur der Legierungsflüssigkeit und den Flüssigkeitsstand des Zinktopfs aufrechterhalten.
- ③ Wenn die aktuellen Produktionsbedingungen eine direkte Zufuhr in den Zinktopf sind, wird empfohlen, den ganzen Legierungsbarren auf einmal zuzugeben, um die durch die Zufuhr verursachten Temperaturänderungen zu reduzieren.
3. Erzeugung und Kontrolle von Zinkschlacke
Es ist ein komplizierter physikalischer und chemischer Prozess, die Legierung von fest zu flüssig zu schmelzen. Das Gas reagiert chemisch mit dem geschmolzenen Metall, und die Sauerstoffreaktion ist am stärksten, und die Oberfläche der Legierung wird oxidiert, um eine bestimmte Menge Schaum zu erzeugen. Die Schlacke enthält Oxide und intermetallische Verbindungen von Eisen, Zink und Aluminium. Die von der Oberfläche der Schmelze abgekratzte Schlacke enthält normalerweise etwa 90 % einer Zinklegierung. Die Reaktionsgeschwindigkeit der Zinkschlackebildung nimmt mit steigender Schmelztemperatur exponentiell zu.
Unter normalen Umständen beträgt der Schlackenausstoß des ursprünglichen Zinklegierungsbarrens weniger als 1%, was im Bereich von 0.3 bis 0.5% liegt; während der Schlackenausstoß von Umschmelzdüsen und Abfallwerkstücken in der Regel zwischen 2 und 5 % liegt.
Kontrolle der Menge an Zinkkrätze
- ① Kontrollieren Sie die Schmelztemperatur streng, je höher die Temperatur, desto mehr Zinkkratze.
- ② Vermeiden Sie das Rühren der Legierungsflüssigkeit im Zinktopf so weit wie möglich, da jede Art des Rührens dazu führt, dass mehr Legierungsflüssigkeit mit Sauerstoffatomen in der Luft in Kontakt kommt, wodurch mehr Schaum gebildet wird.
- ③ Nicht zu häufig abschlacken. Wenn die geschmolzene Legierung der Luft ausgesetzt wird, oxidiert sie und bildet Schaum. Wenn Sie eine dünne Schaumschicht auf der Ofenoberfläche halten, wird die Flüssigkeit im Topf nicht weiter oxidiert.
- ④ Verwenden Sie beim Schlacken einen porösen (Ф6 mm) scheibenförmigen Schlackenrechen, um vorsichtig unter den Schlamm zu kratzen, um ein Aufrühren der Legierungsflüssigkeit so weit wie möglich zu vermeiden, und nehmen Sie die abgekratzte Schlacke auf. Klopfen Sie leicht, damit das geschmolzene Metall in den Zinktopf zurückfließt.
Behandlung von Zinkschlacke
- ① Verkaufen Sie es an den Rohstofflieferanten oder speziellen Verarbeitungsbetrieb zurück, da die Kosten für die Eigenverarbeitung höher sein können.
- ② Das Druckgusswerk erledigt das selbst. Ein separater Ofen ist erforderlich, und die Umschmelztemperatur der Zinkschlacke liegt im Bereich von 420 bis 440 °C. Fügen Sie gleichzeitig Flussmittel hinzu. Um 100 kg Schlacke zu erschmelzen, müssen 0.5 – 1.5 kg Flussmittel zugegeben werden, das zunächst gleichmäßig auf der Metalloberfläche verteilt und dann mit einem Rührwerk gleichmäßig in die Metallschmelze eingemischt wird (ca. 2 – 4 Minuten). Nachdem Sie 5 Minuten gehalten haben, wird die Oberfläche ein Die Schicht ist eher wie Schmutz, also kratzen Sie sie ab.
- ③ Düsenmaterialien, Abfallteile zum Umschmelzen von Düsenmaterialien, Abfallmaterialien, Müllplätze, verschrottete Werkstücke usw. sollten zum Umschmelzen nicht direkt in den Zinktopf der Druckgussmaschine gegeben werden. Der Grund dafür ist, dass die Oberfläche dieser Düsenmaterialien während des Druckgussumformprozesses oxidiert wird und der Gehalt an Zinkoxid viel höher ist als der des ursprünglichen Legierungsbarrens. Wenn diese Düsenmaterialien im Zinktopf umgeschmolzen werden, weil das Zinkoxid unter Hochtemperaturbedingungen in einem viskosen Zustand ist, wird beim Herausnehmen aus dem Zinktopf eine große Menge an Legierungsbestandteilen entfernt. Der Zweck des Umschmelzens des Düsenmaterials und anderer Materialien besteht darin, das Zinkoxid effektiv von der flüssigen Legierung zu trennen. Während des Schmelzens muss etwas Lösungsmittel hinzugefügt und nach dem Gießen in einen Barren verwendet werden.
4. Umschmelzen von Galvanikabfällen
Galvanische Abfälle sollten getrennt von nicht galvanischen Abfällen erschmolzen werden, da Kupfer, Nickel, Chrom und andere Metalle in den Galvanikabfällen in Zink unlöslich sind und als harte Partikel in der Zinklegierung vorhanden sind, was beim Polieren und Bearbeiten zu Schwierigkeiten führt.
Achten Sie beim Umschmelzen von Galvanikschrott auf die Trennung des Beschichtungsmaterials von der Zinklegierung. Geben Sie zuerst den Galvanikschrott in den Tiegel mit der Schmelze der Zinklegierung. Rühren Sie die Schmelze zu diesem Zeitpunkt nicht und fügen Sie kein Flussmittel hinzu. Verwenden Sie das Beschichtungsmaterial, um einen hohen Schmelzpunkt zu haben. Es schmilzt nicht mit der Legierung, sondern schwimmt zunächst auf der Oberfläche der Schmelze. Wenn es vollständig geschmolzen ist, lassen Sie den Tiegel 15-20 Minuten lang stehen, um zu sehen, ob sich Schaum auf der Oberfläche befindet, und kratzen Sie den Schaum sauber. Nach diesem Vorgang werden wir sehen, ob die Zugabe eines Läutermittels erforderlich ist.
5.Angelegenheiten, die beim Schmelzbetrieb beachtet werden müssen
- 1. Tiegel: Vor Gebrauch muss er gereinigt werden, um Öl, Rost, Schlacke und Oxide von der Oberfläche zu entfernen. Um zu verhindern, dass sich das Eisenelement im Gusseisentiegel in der Legierung auflöst, sollte der Tiegel auf 150 ~ 200 ℃ vorgeheizt, eine Farbschicht auf die Arbeitsfläche gesprüht und dann auf 200 ~ 300 ℃ erhitzt werden, um ihn vollständig zu entfernen das Wasser in der Farbe.
- 2. Werkzeuge: Vor dem Einsatz der Schmelzwerkzeuge sollte der Oberflächenschmutz entfernt und die metallberührten Teile vorgewärmt und lackiert werden. Das Werkzeug darf nicht benetzt werden, da es sonst zu Spritzern und Explosion der Schmelze kommt.
- 3. Legierungsmaterial: Vor dem Schmelzen reinigen und vorwärmen, um die an der Oberfläche adsorbierte Feuchtigkeit zu entfernen. Um die Legierungszusammensetzung zu kontrollieren, wird empfohlen, 2/3 des Neumaterials und 1/3 des Recyclingmaterials zu verwenden.
- 4. Die Schmelztemperatur darf 450°C nicht überschreiten.
- 5. Entfernen Sie rechtzeitig den Schaum auf der Flüssigkeitsoberfläche im Zinktopf, füllen Sie das Zinkmaterial rechtzeitig nach und halten Sie die normale Höhe des Schmelzespiegels ein (nicht weniger als 30 mm auf der Tiegeloberfläche), da zu viel Schaum und zu niedriger Flüssigkeitsstand sind leicht Die Materialschlacke dringt in den Schwanenhalszylinder ein, belastet den Stahlzug, den Hammerkopf und den Zylinder selbst, was zum Verklemmen von Hammerkopf, Schwanenhals und Hammerkopfschrott führt.
- 6. Der Schaum auf der Schmelze wird vorsichtig mit einem Schlackenschaber bewegt, um ihn zur Entfernung anzusammeln.
Bitte bewahren Sie die Quelle und Adresse dieses Artikels für den Nachdruck auf: Das Schmelzwissen von Druckgusslegierungen
Mingh Druckgussunternehmen sind der Herstellung und Bereitstellung von hochwertigen und leistungsstarken Gussteilen gewidmet (das Angebot an Metalldruckgussteilen umfasst hauptsächlich) Dünnwandiger Druckguss,Heißkammerdruckguss,Kaltkammerdruckguss), Runder Service (Druckguss-Service,CNC-Bearbeitung,Formenbau,Oberflächenbehandlung). Alle kundenspezifischen Aluminium-Druckguss-, Magnesium- oder Zamak/Zink-Druckguss- und andere Gussanforderungen können uns gerne kontaktieren.
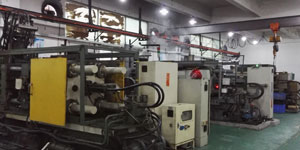
Unter der Kontrolle von ISO9001 und TS 16949 werden alle Prozesse durch Hunderte von fortschrittlichen Druckgussmaschinen, 5-Achsen-Maschinen und anderen Einrichtungen durchgeführt, von Blasgeräten bis hin zu Ultraschall-Waschmaschinen.Minghe verfügt nicht nur über fortschrittliche Ausrüstung, sondern auch über professionelle Team aus erfahrenen Ingenieuren, Bedienern und Inspektoren, um das Design des Kunden zu verwirklichen.
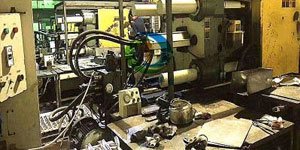
Auftragsfertigung von Druckgussteilen. Zu den Fähigkeiten gehören Kaltkammer-Aluminium-Druckgussteile von 0.15 lbs. bis 6 lbs., Schnellwechseleinrichtung und Bearbeitung. Mehrwertdienste umfassen Polieren, Vibrieren, Entgraten, Kugelstrahlen, Lackieren, Plattieren, Beschichten, Montage und Werkzeugbau. Zu den Materialien, mit denen gearbeitet wird, gehören Legierungen wie 360, 380, 383 und 413.
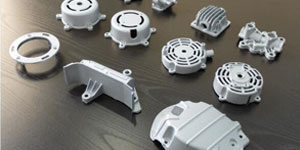
Unterstützung bei der Konstruktion von Zinkdruckguss / gleichzeitige Engineering-Dienstleistungen. Auftragsfertigung von Präzisions-Zink-Druckgussteilen. Es können Miniaturgussteile, Hochdruck-Kokillengussteile, Mehrschieber-Kokillengussteile, konventionelle Kokillengussteile, Einzel- und Einzeldruckgussteile sowie hohlraumdichte Gussteile hergestellt werden. Gussteile können in Längen und Breiten bis zu 24 Zoll in +/-0.0005 Zoll Toleranz hergestellt werden.
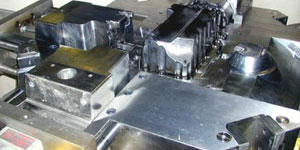
ISO 9001: 2015 zertifizierter Hersteller von Magnesium-Druckguss. Zu den Fähigkeiten gehören Hochdruck-Magnesium-Druckguss bis zu 200 Tonnen Heißkammer und 3000 Tonnen Kaltkammer, Werkzeugdesign, Polieren, Formen, Bearbeitung, Pulver- und Flüssiglackierung, vollständige Qualitätssicherung mit KMG-Fähigkeiten , Montage, Verpackung & Lieferung.
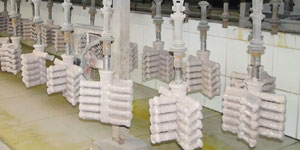
ITAF16949-zertifiziert. Zusätzlicher Casting-Service inklusive Feinguss,Sandguss,Schwerkraftguss, Verlorener Schaumguss,Schleuderguss,Vakuumgießen,Dauerguss,.Zu den Fähigkeiten gehören EDI, technische Unterstützung, Volumenmodellierung und Sekundärverarbeitung.
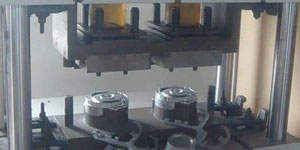
Gussindustrie Teile-Fallstudien für: Autos, Fahrräder, Flugzeuge, Musikinstrumente, Wasserfahrzeuge, optische Geräte, Sensoren, Modelle, elektronische Geräte, Gehäuse, Uhren, Maschinen, Motoren, Möbel, Schmuck, Vorrichtungen, Telekommunikation, Beleuchtung, medizinische Geräte, Fotogeräte, Roboter, Skulpturen, Tongeräte, Sportgeräte, Werkzeuge, Spielzeug und mehr.
Was können wir Ihnen als nächstes helfen?
∇ Zur Startseite gehen für Druckguss China
→Gussteile- Finden Sie heraus, was wir getan haben.
→Bewertete Tipps zu Druckgussdienste
By Minghe Druckgusshersteller |Kategorien: Hilfreiche Artikel |Werkstoff Stichworte: Aluminiumguss, Zinkguss, Magnesiumguss, Titanguss, Edelstahlguss, Messingguss,Bronzeguss,Casting-Video,Unternehmensgeschichte,Aluminiumdruckguss |Kommentare deaktiviert