"Alkali" und "Magnesium" zur Verbesserung der Pelletleistung
Oxidierte Pellets weisen eine gute mechanische Festigkeit und metallurgische Eigenschaften auf und sind zu einer unverzichtbaren hochwertigen Charge für die Eisenherstellung im Hochofen geworden. Der Mangel an inländischem Angebot an Magnetitkonzentrat hat jedoch dazu geführt, dass viele inländische Stahlwerke importiertes Hämatit zur Herstellung von Oxidpellets verwenden. Im Vergleich zu Magnetitpellets haben Hämatitpellets eine hohe Rösttemperatur und einen engen Bereich (1300℃~1350℃) und die Pellets haben eine geringe Druckfestigkeit. Darüber hinaus weisen die sauren Hämatitpellets schlechte metallurgische Eigenschaften auf. Unter diesen gehört Specularit zu einer wichtigen Hämatitart, und die Röstleistung und die metallurgischen Eigenschaften von Pellets sind schlechter als bei gewöhnlichen Hämatitpellets.
Forscher haben viel darüber geforscht, wie Hämatit zur Herstellung hochfester oxidierter Pellets verwendet werden kann. Studien haben gezeigt, dass die Zugabe von Magnetit zu Hämatit zur Herstellung oxidierter Pellets die Vorwärm-Rösttemperatur wirksam senken und die Druckfestigkeit der vorgewärmten Röstpellets erhöhen kann; Die Zugabe von Flussmittel zur Herstellung gefluxter Hämatitpellets ist ebenfalls eine Lösung.
Inländische Pelletfabriken verwenden im Allgemeinen Hämatit und Magnetit, um hochfeste Pellets herzustellen. Mit zunehmendem Hämatitanteil wird die Wirkung der Magnetitzugabe jedoch stark abgeschwächt. Durch die Zugabe von CaO-Flussmittel zur Herstellung von Flussmittelpellets kann eine höhere mechanische Festigkeit und eine bessere Reduzierbarkeit bei niedrigeren Temperaturen erreicht werden, die Hochtemperatur-Reflow-Leistung ist jedoch schlecht und die Reduktionsexpansion ist schwerwiegend. Frühe Studien haben gezeigt, dass die Zugabe von MgO zu den Pellets die Reduktionsexpansionsrate verringern und die Hochtemperatur-Reflow-Leistung verbessern kann.
Derzeit gibt es relativ wenige Berichte über die Auswirkung der Alkalität und des MgO-Gehalts auf die Festigkeit und metallurgischen Eigenschaften von Specularit-Pellets, insbesondere über die Auswirkung von Alkalität und MgO auf die metallurgischen Eigenschaften von Pellets. Daher hat dieser Artikel, der die Auswirkungen der Alkalität und des MgO-Gehalts auf die Festigkeit und metallurgischen Eigenschaften von Spekularitpellets untersucht, einen wichtigen theoretischen Wert für die Verbesserung des Pelletröstens und die Stärkung der Eisenherstellung im Hochofen.
Rohstoffeigenschaften und Forschungsmethoden
Die in diesem Experiment verwendeten Rohstoffe sind brasilianischer Spekularit, Bentonit, Kalkstein und Magnesit. Da brasilianischer Spekularit, Kalkstein und Magnesit eine relativ grobe Partikelgröße haben, werden sie im Labor mit einer Kugelmühle auf die Partikelgröße und spezifische Oberfläche gemahlen, die für die Pelletproduktion erforderlich sind. Spiegelit hat einen hohen Eisengehalt, weniger Gangmineralien und andere schädliche Verunreinigungen und ist ein hochwertiger Pellet-Rohstoff. Kalkstein und Magnesit haben einen niedrigen SiO2-Gehalt und wenige andere schädliche Verunreinigungen. Es handelt sich um hochwertige Calcium-Magnesium-Flussmittel.
Das im Test verwendete Bindemittel ist hochwertiger Bentonit auf Natriumbasis. Die Indikatoren lauten wie folgt: Der Gehalt an Montmorillonit beträgt 92.76 %, das Quellvolumen beträgt 20 ml/g, die Wasserabsorptionsrate in 2 Stunden beträgt 342 % und Der Inhalt von -0.074 mm erreicht 100 %.
Die experimentelle Forschung umfasst den Prozess des Dosierens, Mischens, der Vorbereitung grüner Kugeln, der Trocknung grüner Kugeln, des Vorheizens trockener Kugeln und des Testens der Leistung von Röstpellets. Der SiO2-Gehalt der fertigen Pellets wird durch Zugabe von fein gemahlenem Quarzsand auf 3.0 % bis 3.1 % kontrolliert. Die Alkalität und der MgO-Gehalt der fertigen Pellets werden durch Zugabe von Kalkstein und Magnesit angepasst und die Auswirkungen von Änderungen der Alkalität und des MgO-Gehalts auf die Druckfestigkeit, den Reduktionsgrad, die Reduktionsexpansion, die Reduktionspulverisierung bei niedriger Temperatur und das Weichschmelzen bei hoher Temperatur beeinflusst Eigenschaften der gerösteten Pellets werden untersucht. Beeinflussen.
Testergebnisse und Wirkungsanalyse
„Der Einfluss von Alkalität und MgO-Gehalt auf Druckfestigkeit und Porosität.“ Die Druckfestigkeit von Pellets ist ein wichtiger Indikator für den Druck, dem die Pellets während des Transport- und Lagerungsprozesses sowie im Reduktionsofen standhalten können. Große Hochöfen erfordern eine Druckfestigkeit der Pellets von mehr als 2500 N/Stück.
Bei natürlichem MgO-Gehalt nimmt die Druckfestigkeit von Pellets zunächst mit zunehmender Alkalität zu. Wenn die Alkalität auf 0.2 steigt, erhöht sich die Druckfestigkeit von Pellets von 2400 N/Stück natürlicher Alkalität auf 3,500 N/Stück; Ab Erreichen von 0.4 erhöht sich die Druckfestigkeit von Pellets nicht mehr. Dies ist auf die Erhöhung der Alkalität von CaO, Fe2O3 und SiO2, wie z. B. Calciumferrit und Calciumsilikat, zurückzuführen. Die richtige flüssige Phase begünstigt die Rekristallisation von Hämatit, aber zu viel flüssige Phase trägt nicht zur Verbesserung der Druckfestigkeit der Pellets bei. Unter natürlicher Alkalität nimmt die Druckfestigkeit der Pellets mit zunehmendem MgO-Gehalt ab. Dies liegt daran, dass sich das Magnesit beim Vorwärmen und Rösten der Pellets zersetzt, was die Porosität der Pellets erhöht.
Wenn Alkalität und MgO bei gleichem MgO-Gehalt zusammenarbeiten, ist die Wirkung der Alkalität auf die Druckfestigkeit der kalzinierten Pellets grundsätzlich dieselbe wie die Wirkung der Alkalität auf die Druckfestigkeit der Pellets bei natürlichem MgO-Gehalt, d. h. die Druckfestigkeit der Pellets. Mit zunehmender Alkalität nimmt die Festigkeit zunächst zu. Ab einem bestimmten Wert der Alkalität steigt die Druckfestigkeit der Pellets nicht mehr wesentlich an; Bei gleicher Alkalität nimmt die Druckfestigkeit der Pellets mit zunehmendem MgO-Gehalt ab, was darauf zurückzuführen ist, dass mit zunehmendem MgO-Gehalt die Porosität der Pellets zunimmt und gleichzeitig MgO in die Schlackenphase eindringt, um die Porosität zu erhöhen Schmelzpunkt der Gangmineralien, was eine gewisse hemmende Wirkung auf die Bildung der flüssigen Phase hat. Die Testergebnisse zeigen, dass bei einer Alkalität über 0.2 die Druckfestigkeit von Spekularitpellets mit unterschiedlicher Alkalität und unterschiedlichem MgO-Gehalt mehr als 2500 N/Stück erreichen kann.
Mit zunehmender Flussmittelmenge vergrößern sich auch die Poren, die durch die Zersetzung des Flussmittels beim Vorwärmen und Rösten entstehen. Die Zugabe von Flussmitteln beeinflusst nicht nur die chemische und mineralische Zusammensetzung der Pellets, sondern auch die Struktur und Porosität der Pellets. Dies wirkt sich in gewissem Maße auf die Druckfestigkeit und die metallurgischen Eigenschaften der Pellets aus.
Der Einfluss von Alkalität und MgO-Gehalt auf den Reduktionsgrad. Der Reduktionsgrad (RI) ist ein wichtiger Indikator zur Beurteilung der Tendenz und Schwierigkeit der Sauerstoffentfernung aus Eisenerz unter den Temperatur- und Atmosphärenbedingungen in der Reduktionszone des Hochofens. Zu den Faktoren, die den Reduktionsgrad von Eisenerz beeinflussen, gehören Partikelgröße, Porosität, Mineralzusammensetzung und -struktur sowie die Zusammensetzung des Ganggesteins.
Der Reduktionsgrad saurer Pellets mit natürlicher Alkalität und natürlichem MgO-Gehalt ist gering und beträgt nur 62.22 %. Mit zunehmendem MgO-Gehalt nimmt der Reduktionsgrad zu. Bei einem MgO-Gehalt von 3.0 % kann der Reduktionsgrad der Pellets 68 % erreichen; Wenn der MgO-Gehalt die Alkalität erhöht, wird der Reduktionsgrad von Specularit-Pellets erheblich verbessert. Bei einer Erhöhung der Alkalität auf 1.2 steigt der Reduktionsgrad der Pellets auf 72.82 %. Dies liegt daran, dass die Zugabe von Kalkstein die Porosität der Pellets erhöht und gleichzeitig CaO mit Fe2O3 reagiert, um leicht reduzierbares Calciumferrit zu bilden.
Wenn Alkalität und MgO bei gleicher Alkalität zusammenwirken, nimmt der Reduktionsgrad von Mirrorit-Pellets mit zunehmendem MgO-Gehalt zu; Bei gleichem MgO-Gehalt nimmt der Reduktionsgrad mit zunehmender Alkalität zu.
Wenn die Alkalität 1.2 erreicht und der MgO-Gehalt auf 3.0 % ansteigt, beträgt der Reduktionsgrad der Pellets bis zu 76.94 %. Dies liegt daran, dass Magnesit auch die Porosität der Pellets während des Vorheizens und Röstens der Pellets erhöht und MgO den Schmelzpunkt der Schlackenphase und des Schwimmkörpers erhöhen kann, so dass es während des Reduktionsprozesses nicht leicht zu schmelzen ist. und die Poren der Pellets werden nicht geschmolzen. Das Material ist gefüllt, um eine hohe Porosität aufrechtzuerhalten, die die Gasdiffusion begünstigt.
Der Einfluss von Alkalität und MgO-Gehalt auf die Reduktionsexpansion.
Unter dem natürlichen MgO-Gehalt nimmt die Reduktionsexpansionsrate von Specularit-Pellets zunächst zu und dann ab, und die Alkalität erreicht den Maximalwert zwischen 0.4 und 0.6, und der Maximalwert liegt bei bis zu 32 %.
Dies liegt daran, dass ein kleiner Teil des den Pellets zugesetzten CaO mit Fe2O3 unter Bildung von Calciumferrit reagiert und der größte Teil davon in die Schlackenphase gelangt. Wenn es nicht reduziert wird, wird die Schlackenphase vom binären System CaO-SiO2 dominiert. Wenn die Alkalität zwischen 0.4 und 0.6 liegt, liegt der SiO2-Gehalt in der Schlackenphase zwischen 62.5 % und 70 %, was dem Intervall der binären eutektischen Punktzusammensetzung von Calciummetasilikat (CaOSiO2) und SiO2 und seinem Tiefpunkt entspricht Der eutektische Temperaturpunkt liegt bei 1436℃, aber unter reduzierenden Bedingungen wird diese Schlackenphase aufgrund der Zugabe von FeO zum ternären Schlackensystem CaO-SiO2-FeO. In diesem Schlackesystem bleibt das Verhältnis von CaO und SiO2 unverändert. Der Schmelzpunkt der Schlackenphase steigt mit zunehmendem FeO-Gehalt stark an. Im reinen ternären Schlackesystem kann sie bis zu 1093 °C betragen, und die Schlackenphase mit niedrigem Schmelzpunkt verschlechtert lediglich die Reduktion und Ausdehnung der Pellets.
Unter natürlicher Alkalität nimmt die Reduktionsexpansionsrate von Pellets mit zunehmendem MgO-Gehalt leicht ab, dies ist jedoch nicht offensichtlich. Dies ist auf die natürliche Alkalität und die natürliche MgO-Pelletschlackenphase mit einem Schmelzpunkt von 1700℃ zurückzuführen, wenn der SiO2-Gehalt 90 % beträgt. Durch die Zugabe von MgO wird die Schlackenphase vom MgO-SiO2-Binärsystem dominiert, dessen niedrige eutektische Temperatur jedoch auch eine niedrige eutektische Temperatur aufweist. 1543°C. Wenn Alkalität und MgO zusammenarbeiten, ist der Einfluss der Alkalität auf die Reduktionsexpansionsrate von Pellets im Wesentlichen derselbe wie der natürliche MgO-Gehalt bei gleichem MgO-Gehalt. Bei der Zugabe von MgO erhöht sich der Schmelzpunkt der Schlackenphase durch das Einschmelzen von MgO in die Schlackenphase. Gleichzeitig wird durch MgO in der Schlackenphase auch der Schmelzpunkt der Schlackenphase erhöht.
Daher kann bei gleicher Alkalität eine Erhöhung des MgO-Gehalts die Reduktionsexpansion verringern.
Die Volumenausdehnung des Hämatits in den oxidierten Pellets wird zu Magnetit und Floatit reduziert. Diese Ausdehnung wird hauptsächlich durch die Änderung der Kristallstruktur bei der Reduktion des Hämatits zu Magnetit verursacht. Die Reduktionsexpansionsrate von Pellets hängt von der Gangartzusammensetzung und der Fähigkeit der Schlackenphase ab, der durch die Reduktion von Hämatitpartikeln erzeugten Belastung standzuhalten.
Die Schlackenphase mit hohem Schmelzpunkt ist während des Reduktionsprozesses nicht leicht zu schmelzen, und die Aufrechterhaltung einer hohen Festigkeit kann die Reduktionsexpansionsrate der Pellets wirksam begrenzen, während die Schlackenphase mit niedrigem Schmelzpunkt die Reduktionsexpansion der Pellets verschlechtern wird.
Die Reduktionsexpansionsrate von Pellets unter 20 % gehört zum normalen Expansionsbereich, und die Alkalität von Spekularitpellets sollte im Bereich von weniger als 0.2 oder größer oder gleich 1.0 kontrolliert werden.
In der allgemeinen industriellen Produktion muss die Reduktionsexpansionsrate von Pellets jedoch unter 15 % gehalten werden. Bei Spekularitpellets mit natürlicher Alkalität, die 3.0 % bis 3.1 % SiO2 enthalten, beträgt die Reduktionsexpansionsrate weniger als 15 % und der Reduktionsgrad beträgt nur 62.2 %. Wenn der Reduktionsgrad durch Erhöhen der Alkalität verbessert wird, ist es notwendig, die Alkalität zu reduzieren. Erst wenn der Grad der Erhöhung auf 1.0 und der MgO-Gehalt auf 3.0 % oder die Alkalität auf 1.2 und der MgO-Gehalt ≥ 1.0 % steigt, kann die Reduktionsausweitung erfolgen Steuersatz niedriger als 15 % sein.
Der Einfluss von Alkalität und MgO-Gehalt auf die Pulverisierung bei niedriger Temperaturreduktion. Die Niedertemperaturreduktionspulverisierung (RDI) spiegelt die Tendenz von Pellets wider, Pulver zu erzeugen, wenn sie im oberen Teil des Hochofens oder Direktreduktionsschachtofens bei einer Temperatur von 400 °C bis 600 °C reduziert werden. Der Hauptgrund für die Reduktion und Pulverisierung bei niedrigen Temperaturen ist die Volumenausdehnung und Gitterverzerrung, die durch die Umwandlung der Kristallstruktur bei der Reduktion von Hämatit zu Magnetit verursacht wird.
Beim Vorwärmen und Rösten von Pellets entstehen im Wesentlichen drei Bindungsmethoden:
Eisenoxid-Rekristallisation, Silikatbindung und Ferritbindung.
Unter diesen ist die Hämatit-Rekristallisationsbindung die häufigste und stärkste, aber Hämatit ist unter reduzierenden Bedingungen äußerst instabil, während die Silikatbindungsphase aufrechterhalten werden kann, wenn Hämatit zu Magnetit reduziert wird. Ändern.
Daher ist es möglich, diese gleichmäßige Verteilung zu erhöhen und eine stabile Bindungsphase unter Reduktionsbedingungen bei niedriger Temperatur aufrechtzuerhalten, indem man ein Flussmittel hinzufügt, um so die Reduktion und Pulverisierung von Mirrorit-Pellets bei niedriger Temperatur zu reduzieren.
Bei den Pellets mit natürlicher Alkalität und natürlichem MgO-Gehalt handelt es sich hauptsächlich um Hämatit-Festphasendiffusionsverfestigung mit weniger Silikatbindungsphase. Daher wird bei der Niedertemperaturreduktion mehr Pulver erzeugt, und sein RDI-3.15-mm-Wert beträgt bis zu 12.75. %. Unter dem natürlichen MgO-Gehalt stieg die Alkalität auf 0.2 und der RDI-3.15-mm-Wert der Pellet-Niedertemperatur-Reduktionspulverisierungsrate sank schnell auf 0.52 %; Die Alkalität stieg weiter an und der RDI-3.15-mm-Wert blieb im Wesentlichen bei etwa 0.5 %. Dies liegt daran, dass die Zugabe von CaO es den Pellets ermöglicht, mehr flüssige Silikatphasen zu bilden, die während der Niedertemperaturreduktion während des Vorheizens und Kalzinierens stabil sind, wodurch der Zweck der Reduzierung der Niedertemperaturreduktion und Pulverisierung der Pellets erreicht wird.
Bei natürlicher Alkalität sinken bei steigendem MgO-Gehalt die Niedertemperaturreduktion und die Pulverisierungsrate der Pellets, RDI-3.15 mm, alle unter 3.0 %. Wenn die Alkalität und MgO zusammenarbeiten, ist der RDI-3.15-mm-Wert von Pellets bei der Niedertemperatur-Reduktionspulverisierung niedrig. RDI-3.15 mm nimmt mit zunehmender Alkalität ab und steigt mit zunehmendem MgO-Gehalt leicht an. Dies ist auf MgO zurückzuführen. Es kann die Bildung von Silikat in flüssiger Phase behindern.
Der Einfluss von Alkalität und MgO-Gehalt auf die Reflow-Eigenschaften. Die Schmelzeigenschaften von Pellets können die Bildung der Pellets in der Weichschmelzzone im unteren Teil des Hochofens und ihre Leistung in der Weichschmelzzone widerspiegeln. Die Reflow-Eigenschaften der Charge haben einen größeren Einfluss auf den Betrieb des Hochofens. Die Erweichungstemperatur der Pellets ist niedrig und das Reflow-Intervall ist groß, und die Luftdurchlässigkeit der Reflow-Zone im unteren Teil des Hochofens wird schlecht, was der Konvektion des Reduktionsgases und der Charge nicht förderlich ist beeinträchtigt den Reduktionsprozess erheblich.
Die Säurepellets mit natürlicher Alkalität und natürlichem MgO-Gehalt beginnen bei 1009 °C zu erweichen und die Tropftemperatur beträgt 1272 °C. Bei natürlichem MgO-Gehalt erhöht sich die Alkalität auf 1.2, die Erweichungstemperatur der Pellets steigt auf 1034 °C, das Erweichungsintervall und das Erweichungsintervall verengen sich und auch die Tropftemperatur steigt auf 1299 °C. Wenn die Alkalität 1.2 beträgt, kann eine Erhöhung des MgO-Gehalts die Erweichungsstarttemperatur und die Tropftemperatur erhöhen. Wenn der MgO-Gehalt 1.0 % beträgt, steigt die Pellet-Erweichungstemperatur auf 1072 °C, die Tropftemperatur erreicht 1319 °C, der MgO-Gehalt steigt weiter an und die Pellet-Erweichungstemperatur steigt nicht .
Die Reflow-Eigenschaften von Pellets werden hauptsächlich durch die bei der Reduktion entstehenden niedrig schmelzenden flüssigen Phasen wie Fusterit und Schlacke beeinflusst. Die schlechten Hochtemperatur-Reflow-Eigenschaften von Säurepellets sind hauptsächlich auf den niedrigen Schmelzpunkt der FeO-reichen Olivin-Schlackenphase während des Reduktionsprozesses zurückzuführen, und die Zugabe von MgO kann den Schmelzpunkt der Schlackenphase erhöhen. Die Bildung einer festen Lösung mit einem hohen Schmelzpunkt wird auch eine Rolle bei der Verbesserung der Hochtemperatur-Reflow-Eigenschaften der Pellets spielen.
Bitte bewahren Sie die Quelle und Adresse dieses Artikels für den Nachdruck auf: "Alkali" und "Magnesium" zur Verbesserung der Pelletleistung
Mingh Druckgussunternehmen sind der Herstellung und Bereitstellung von hochwertigen und leistungsstarken Gussteilen gewidmet (das Angebot an Metalldruckgussteilen umfasst hauptsächlich) Dünnwandiger Druckguss,Heißkammerdruckguss,Kaltkammerdruckguss), Runder Service (Druckguss-Service,CNC-Bearbeitung,Formenbau,Oberflächenbehandlung). Alle kundenspezifischen Aluminium-Druckguss-, Magnesium- oder Zamak/Zink-Druckguss- und andere Gussanforderungen können uns gerne kontaktieren.
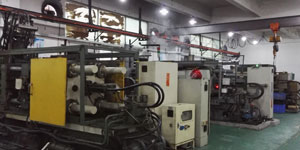
Unter der Kontrolle von ISO9001 und TS 16949 werden alle Prozesse durch Hunderte von fortschrittlichen Druckgussmaschinen, 5-Achsen-Maschinen und anderen Einrichtungen durchgeführt, von Blasgeräten bis hin zu Ultraschall-Waschmaschinen.Minghe verfügt nicht nur über fortschrittliche Ausrüstung, sondern auch über professionelle Team aus erfahrenen Ingenieuren, Bedienern und Inspektoren, um das Design des Kunden zu verwirklichen.
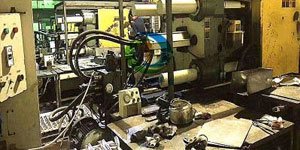
Auftragsfertigung von Druckgussteilen. Zu den Fähigkeiten gehören Kaltkammer-Aluminium-Druckgussteile von 0.15 lbs. bis 6 lbs., Schnellwechseleinrichtung und Bearbeitung. Mehrwertdienste umfassen Polieren, Vibrieren, Entgraten, Kugelstrahlen, Lackieren, Plattieren, Beschichten, Montage und Werkzeugbau. Zu den Materialien, mit denen gearbeitet wird, gehören Legierungen wie 360, 380, 383 und 413.
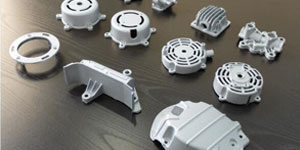
Unterstützung bei der Konstruktion von Zinkdruckguss / gleichzeitige Engineering-Dienstleistungen. Auftragsfertigung von Präzisions-Zink-Druckgussteilen. Es können Miniaturgussteile, Hochdruck-Kokillengussteile, Mehrschieber-Kokillengussteile, konventionelle Kokillengussteile, Einzel- und Einzeldruckgussteile sowie hohlraumdichte Gussteile hergestellt werden. Gussteile können in Längen und Breiten bis zu 24 Zoll in +/-0.0005 Zoll Toleranz hergestellt werden.
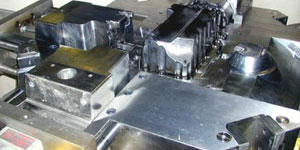
ISO 9001: 2015 zertifizierter Hersteller von Magnesium-Druckguss. Zu den Fähigkeiten gehören Hochdruck-Magnesium-Druckguss bis zu 200 Tonnen Heißkammer und 3000 Tonnen Kaltkammer, Werkzeugdesign, Polieren, Formen, Bearbeitung, Pulver- und Flüssiglackierung, vollständige Qualitätssicherung mit KMG-Fähigkeiten , Montage, Verpackung & Lieferung.
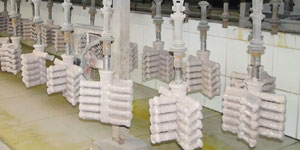
ITAF16949-zertifiziert. Zusätzlicher Casting-Service inklusive Feinguss,Sandguss,Schwerkraftguss, Verlorener Schaumguss,Schleuderguss,Vakuumgießen,Dauerguss,.Zu den Fähigkeiten gehören EDI, technische Unterstützung, Volumenmodellierung und Sekundärverarbeitung.
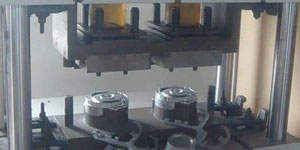
Gussindustrie Teile-Fallstudien für: Autos, Fahrräder, Flugzeuge, Musikinstrumente, Wasserfahrzeuge, optische Geräte, Sensoren, Modelle, elektronische Geräte, Gehäuse, Uhren, Maschinen, Motoren, Möbel, Schmuck, Vorrichtungen, Telekommunikation, Beleuchtung, medizinische Geräte, Fotogeräte, Roboter, Skulpturen, Tongeräte, Sportgeräte, Werkzeuge, Spielzeug und mehr.
Was können wir Ihnen als nächstes helfen?
∇ Zur Startseite gehen für Druckguss China
→Gussteile- Finden Sie heraus, was wir getan haben.
→Bewertete Tipps zu Druckgussdienste
By Minghe Druckgusshersteller |Kategorien: Hilfreiche Artikel |Werkstoff Stichworte: Aluminiumguss, Zinkguss, Magnesiumguss, Titanguss, Edelstahlguss, Messingguss,Bronzeguss,Casting-Video,Unternehmensgeschichte,Aluminiumdruckguss |Kommentare deaktiviert