Grundkenntnisse der Druckgusswerkzeuge aus Aluminiumlegierungen
1. Die grundlegende Definition von Druckgusswerkzeugen aus Aluminiumlegierungen
Der Formenbau bezeichnet die Bearbeitung von Umform- und Platinenwerkzeugen. Darüber hinaus umfasst es auch Stanzformen und Stanzwerkzeuge. Im Allgemeinen besteht die Werkzeugausstattung aus einem oberen Modul und einem unteren Modul. Die Stahlplatte wird zwischen Ober- und Untergesenk gelegt und das Material unter Einwirkung der Presse geformt. Beim Öffnen der Presse wird das durch die Werkzeugform bestimmte Werkstück erhalten bzw. der entsprechende Abfall entfernt. Mit Werkzeugen können so kleine Teile wie elektronische Steckverbinder und so groß wie das Armaturenbrett eines Autos geformt werden.
Progressive Matrize ist ein Werkzeugsatz, der das Werkstück automatisch von einer Station zur anderen bewegen und das Formteil in die letzte Station bringen kann.
Der Werkzeugprozess umfasst: Stanzmatrize, Stanzmatrize, Verbundmatrize, Extrusionsmatrize, Vierschiebermatrize, Folgeverbundmatrize, Stanzmatrize, Stanzwerkzeug usw.
2. Werkzeugtyp
- (1) Metallstanzwerkzeuge: kontinuierliche Matrize, einzelne Matrize, zusammengesetzte Matrize, Ziehmatrize
- (2) Kunststoffform: Spritzgussform, Extrusionsform, Saugform
- (3) Druckgusswerkzeuge: Druckgusswerkzeuge aus Zinklegierung, Druckgusswerkzeuge aus Aluminiumlegierungen
- (4) Schmiedewerkzeuge
- (5) Pulvermetallurgie-Werkzeuge
- (6) Gummiwerkzeuge
3. Werkzeugprozess
- Schneiden: vorderes Matrizenmaterial, hinteres Matrizenmaterial, Einlegematerial, Reihenpositionsmaterial und geneigtes Vortriebsmaterial;
- Offener Rahmen: vorderer Formrahmen und hinterer Formrahmen;
- Öffnung: Öffnung des vorderen Formhohlraums, Öffnung des hinteren Formhohlraums, Öffnung der Trennfuge;
- Kupfermännchen: Kupfermännchen vorne, Kupfermännchen hinten, Kupfermännchen mit Trennwinkelabstand;
- Drahtschneiden: Trennlinie einfügen, Kupferstecker, schräge obere Kissenposition;
- Computergongs: feine Gongs-Trennlinie, feine Gongs nach Formkern;
- EDM: vordere Form dick, kupferne Patrize, männliche Formlinienwinkelreinigung, hintere Formknochenposition, Kissenposition;
- Bohren, Pinhole, Fingerhut; Werkzeugbestückung oben Pinhole Wasserstraße Loch Verarbeitungslinie Position, Reihenposition Pol;
- Schräge Spitze, zusammengesetzter Fingerhut, mit Fingerhut.
4 Sonstiges
- (1) Chui, Codeformgrube, Müllnagel (Grenznagel);
- (2) Flugmodell;
- (3) Düse, Stützkopf, Quelle und Wassertransport;
- (4) Die Position des Sparens der Form, des Polierens, der vorderen Form- und der hinteren Formknochenposition;
- (5) Feine Wasserstruktur, Zugstangen-Schraubhaken, Feder
- (6) Wärmebehandlung, Abschrecken und Nitrieren wichtiger Teile;
5.Werkzeugsoftware
UGNX, Pro / NC, CATIA, Mastercam, SURFCAM, topsolid cam, space-e, camworks, worknc, tebis, hyperMILL, PowerMILL, gibbscam, featurecam, etc.
6. Grundfunktionen
- (1) Ein Werkzeugpaar besteht im Allgemeinen aus einer Matrize, einem Stempel und einer Matrizenbasis, und einige von ihnen können mehrteilige Montagemodule sein. Daher erfordert die Kombination von Ober- und Unterwerkzeug, die Kombination von Einsätzen und Kavitäten sowie der Zusammenbau von Modulen eine hohe Bearbeitungsgenauigkeit. Die Maßhaltigkeit von Präzisionswerkzeugen liegt oft im µm-Bereich.
- (2) Die Formoberfläche einiger Produkte, wie Automobilverkleidungsteile, Flugzeugteile, Spielzeug und Haushaltsgeräte, besteht aus einer Vielzahl von gekrümmten Oberflächen, so dass die Werkzeughohlraumoberfläche sehr komplex ist. Einige Oberflächen müssen rechnerisch behandelt werden.
- (3) Die Serienfertigung von Kleinwerkzeugen ist keine Massenproduktion. In vielen Fällen wird nur eine Lieferung produziert.
- (4) Bei der Werkzeugherstellung gibt es viele Arten von Arbeitsverfahren, wie Fräsen, Bohren, Bohren, Reiben und Gewindeschneiden.
- (5) Die Verwendung von wiederholten Produktionswerkzeugen hat eine lange Lebensdauer. Wenn ein Werkzeugpaar über seine Lebensdauer hinaus verwendet wird, muss es durch ein neues ersetzt werden, so dass sich die Herstellung von Werkzeugen oft wiederholt.
- (6) Teilweise liegen bei der Profilerstellung weder Zeichnungen noch Daten vor und die Profilerstellung sollte objektbezogen erfolgen. Dies erfordert eine hohe Präzision und keine Verformung.
- (7) Werkzeugmaterialien sind ausgezeichnet und haben eine hohe Härte. Die Hauptwerkstoffe der Werkzeuge bestehen aus hochwertigem legiertem Stahl, insbesondere solchen mit hoher Lebensdauer, die oft aus Ledeburit-Stahl wie Crl2 und CrWMn bestehen. An diese Stahlsorte werden strenge Anforderungen vom Blankschmieden über die Verarbeitung bis hin zur Wärmebehandlung gestellt. Daher kann die Vorbereitung der Verarbeitungstechnologie nicht ignoriert werden, die Verformung durch die Wärmebehandlung ist auch ein ernstes Problem bei der Verarbeitung.
Entsprechend den obigen Merkmalen sollte die Auswahl der Werkzeugmaschinen den Verarbeitungsanforderungen so weit wie möglich entsprechen. Zum Beispiel sollte die Funktion des CNC-Systems stark sein, die Präzision der Werkzeugmaschine sollte hoch sein, die Steifigkeit sollte gut sein, die thermische Stabilität sollte gut sein und die Profilierungsfunktion sollte bereitgestellt werden.
7. Anordnung des Prozessablaufs
- (1) Bodenverarbeitung, Verarbeitungsmengengarantie;
- (2) Gussrohling-Benchmark-Ausrichtung, 2D-, 3D-Oberflächentoleranzinspektion;
- (3) Grobbearbeitung von 2D- und 3D-Profilen, Nicht-Installations- und Nicht-Arbeitsebenen-Bearbeitung (einschließlich Sicherheitsplattformoberfläche, Puffermontageoberfläche, Druckplattenebene und Seitenbezugsebene);
- (4) Vor dem Semi-Schlichten sollte die seitliche Bezugsebene richtig gefunden werden, um die Genauigkeit sicherzustellen;
- (5) Halbfertigbearbeitung von 2D- und 3D-Oberflächen, Fertigbearbeitung aller Arten von Installationsarbeitsflächen (einschließlich Begrenzungsblock-Installationsoberfläche und Kontaktoberfläche, Einsatz-Installationsoberfläche und Rückseite, Stanz-Installationsoberfläche, Abfallschneider-Installationsoberfläche und Rückseite, Federinstallation Oberfläche und Kontaktfläche, verschiedene Hubbegrenzungsarbeitsfläche, Keileinbaufläche und -rückseite), alle Arten von Führungsflächen und Führungslöchern halbieren und die Nachbearbeitung berücksichtigen Bezugsbohrung und Höhenbezug bearbeiten und Daten aufzeichnen;
- (6) Überprüfen und erneute Überprüfung der Bearbeitungsgenauigkeit;
- (7) Fitter-Inlay-Prozess;
- (8) Vor dem Schlichten die Bezugsebene der Prozess-Referenzbohrung ausrichten und das Wendeschneidplattenaufmaß prüfen;
- (9) Fertigbearbeitungsprofil 2D, 3D, Seitenstempelprofil und Lochposition, Fertigbearbeitungsprozess-Bezugsloch und Höhenbezug, Fertigbearbeitungs-Führungsfläche und -Führungsloch;
- (10) Prüfen und überprüfen Sie die Bearbeitungsgenauigkeit.
8. Angelegenheiten, die Aufmerksamkeit erfordern
(1) Die Prozessvorbereitung ist prägnant und detailliert, und der Verarbeitungsinhalt wird so numerisch wie möglich ausgedrückt;
(2) Bei den wichtigsten und schwierigen Verarbeitungspunkten ist das handwerkliche Können besonders hervorzuheben;
(3) Es ist notwendig, Verarbeitungsorte zu kombinieren und der Prozess ist klar zum Ausdruck gebracht;
(4) Wenn die Einlage separat verarbeitet werden muss, beachten Sie die Prozessanforderungen an die Verarbeitungsgenauigkeit;
(5) Nach der kombinierten Bearbeitung ist der Prozess für die separat zu bearbeitenden Einlegeteile mit den Benchmark-Anforderungen für die getrennte Bearbeitung während der kombinierten Bearbeitung ausgestattet;
(6) Federn werden bei der Formbearbeitung am leichtesten beschädigt, daher sollten Formfedern mit langer Ermüdungslebensdauer gewählt werden.
Verarbeitungsprobleme von großen Druckgussformen aus Aluminiumlegierungen
1. Riesige Größe und Gewicht
Bei der Verarbeitung von Großformen ist der Umgang mit den eigenen enormen Abmessungen und Gewichten eine große Herausforderung für die verarbeitenden Betriebe. Die Bearbeitung großer Formen erfordert oft viel Arbeitsaufwand, spezielle Ausrüstung und mehrfaches Justieren und Spannen, und auch die Bearbeitungsgenauigkeit wird von vielen möglichen Faktoren beeinflusst und kann nicht ohne weiteres garantiert werden.
2. Die Frage der Anschaffungskosten
Die größten Kosten, die direkt mit der Verarbeitung und Herstellung verschiedener großer Formen zusammenhängen, sind die Anschaffungskosten der Werkzeugmaschine. Die Werkzeugmaschine, die große Formen herstellen kann, ist ziemlich teuer, insbesondere bei der komplexen Prozessanordnung werden mehrere Werkzeugmaschinen benötigt, um alle Prozesse vom Schruppen bis zum Fertigstellen der Form abzuschließen. Solche frühen hohen Inputkosten sind für viele Unternehmen auch das größte Hindernis beim Eintritt in diesen Markt. Daraus können wir sehen, dass, wenn die Schrupp- und Schlichtbearbeitung von großen Formen auf einer geeigneten Werkzeugmaschine realisiert werden kann, auch wenn nur eine Fehlersuche und Aufspannung erforderlich ist, viele Probleme gelöst werden und die Bearbeitungsgenauigkeit gewährleistet werden kann.
Bearbeitungszentren
1. Gusseisenbettstruktur, Werkzeugmaschinenspindel hat Wärmeableitungsfunktion
Gusseisenmaterial hat eine hohe Steifigkeit und Wärmeableitungseigenschaften und ist daher das stabilste Material für die Herstellung von Werkzeugmaschinenstrukturen. Jede Werkzeugmaschine, die zum Fräsen von großen Teilen verwendet wird, muss zunächst eine sehr starke Gussstruktur aufweisen und mit einer Spindel mit Wärmeableitungsfunktion ausgestattet sein.
Was die Hauptwelle der Werkzeugmaschine anbelangt, muss diese eine eingebaute Kühltechnologie verwenden, um die Hauptwelle von der Außenseite des Lagers zu kühlen, um sicherzustellen, dass die Hauptwelle selbst nicht durchgebrannt ist oder aufgrund von thermischen Schäden an Präzision verliert Ausdehnung bei der Langzeitbearbeitung. Diese Faktoren sind sehr wichtig, da die Verarbeitung großer Formen lange dauert und dies unter schweren Schnittbedingungen die Hitze und die Belastung der Form erhöht. Daher müssen die Strukturteile der Werkzeugmaschine gute Steifigkeits- und Wärmeableitungseigenschaften aufweisen, was die Voraussetzung für die Verarbeitung von hochwertigen Druckgussformen aus Aluminiumlegierungen in großem Maßstab ist. Daher ist es erforderlich, die Schwingungen der Werkzeugmaschine während des Bearbeitungsprozesses weitestgehend zu begrenzen und die während des Bearbeitungsprozesses erzeugte Wärme schnell abzuleiten. Durch die Auswahl der richtigen Bearbeitungsmaschinen und Werkzeuge kann eine Win-Win-Situation in Bezug auf Kosten und Zykluszeit erreicht werden.
2. Thermische Stabilitätstechnologie
Aufgrund der langen Verarbeitungszeit muss auch der Einfluss der Umgebungstemperatur berücksichtigt werden. Zum Beispiel führt die Verarbeitung einer großen Druckgussform aus Aluminiumlegierung auf einer gewöhnlichen Werkzeugmaschine, wenn sich die Umgebungstemperatur um 10 °C ändert, zu einer Temperaturänderung von 6 °C in der Werkzeugmaschinensäule, die eine Änderung von 0.07 mm in . verursacht die Parallelität der Spindelwinkelplatte. Daher muss die Konstruktion der Werkzeugmaschine den Einfluss der Umgebungstemperatur berücksichtigen, um den Einfluss der Umgebungstemperatur auf die Genauigkeit der bearbeiteten Teile zu vermeiden.
3. Schnelligkeit
Für ein großes Werkzeugbearbeitungszentrum, das sich schnell bewegen kann, sollte die Spindeldrehzahl der großen Werkzeugmaschine für die Werkzeugbearbeitung mindestens 20000 U/min und die Metallschneidgeschwindigkeit 762 ~ 20000 mm/min erreichen.
4. Präzision
Eine präzise Kontrolle durchläuft immer alle Stufen der Werkzeugbearbeitung. Wenn Sie auf einem Bearbeitungszentrum die Schrupp- und Schlichtbearbeitung von großen Formen umsetzen müssen, müssen Sie die Positioniergenauigkeit und Wiederholgenauigkeit der Werkzeugmaschine streng kontrollieren. Das Bearbeitungszentrum für große Formen hat in der Regel eine Positioniergenauigkeit von ±1.5 µm und eine Wiederholgenauigkeit von ±1 µm. Gleichzeitig sollte die Pitch-Genauigkeit innerhalb von 5 μm gehalten werden.
5. Feedback-Auflösung
Für die hochpräzise Oberflächenbearbeitung ist die Feedback-Auflösung der Werkzeugmaschine selbst sehr wichtig, um die Genauigkeit der bearbeiteten Teile zu erkennen. Mit der standardmäßigen Rückkopplungsauflösung von 1 μm sind die normalerweise erhaltenen Ergebnisse nicht sehr zufriedenstellend. Wenn die Auflösung 0.05 μm erreichen kann, ist das Endergebnis nahezu fehlerfrei. Darüber hinaus kann durch die Steuerung der Werkzeugmaschinenauflösung, Skalenrückmeldung und Kugelgewindetriebe mit kleiner Steigung die Bearbeitungsqualität der Teileoberfläche weiter verbessert werden.
6. Spindel
Die auf dem Großformbearbeitungszentrum eingesetzte Spindel muss den Anforderungen der Schruppbearbeitung, der Vorschlichtung und der hochwertigen Schlichtbearbeitung genügen, und als Referenzstandard sollte die erzielbare Oberflächenbearbeitungsqualität im Bereich von 2 μm kontrolliert werden. Normalerweise ist es für die Endbearbeitung der Formschließfläche und des Trennlinienteils sehr wichtig, aber bei der traditionellen Technologie müssen viele Formenhersteller manuelles Polieren verwenden, um den Mangel an Werkzeugbearbeitungsgenauigkeit auszugleichen. Da großformatige Bearbeitungsmaschinen teuer in der Herstellung sind, ist es offensichtlich unpraktisch, eine multifunktionale Werkzeugmaschine für diesen Prozess zu kaufen.
Darüber hinaus muss eine sinnvolle Spindelauslegung in der Lage sein, die Standzeit des Werkzeugs zu maximieren, damit es während des Bearbeitungszyklus vibrationsarm und mit geringem Temperaturanstieg weiterarbeiten kann. Wenn beispielsweise bei der Bearbeitung von Armaturenbrettformen für Automobile auf einem großen Werkzeugbearbeitungszentrum ein 16-mm-CBN-Einsatz für die Endbearbeitungswerkzeuge verwendet wird, kann die Bearbeitungsgeschwindigkeit 8 m/min erreichen, die Lebensdauer überschreitet 30 Stunden und die Qualität der bearbeiteten Oberfläche kann kontrolliert werden innerhalb von 0.336~3.2μm. Es zeigt sich, dass angesichts der gestiegenen Werkzeugkosten bei der Bearbeitung von Großformen durch den Einsatz speziell ausgelegter Großformenbearbeitungsmaschinen nicht nur die Standzeit der Werkzeuge verlängert, sondern auch jede Menge Werkzeugkosten für die Bearbeitung jeder Form eingespart werden können .
7. Beweglicher Mehrachsen-Bearbeitungskopf
Aufgrund der Beschränkung von Formgröße und Gewicht dauert das Einspannen des Werkstücks in der Regel sehr lange. Daher reduziert die Verwendung eines 3-Achsen-Bearbeitungszentrums nicht nur die Anzahl der Fehlersuch- und Spannzeiten des Werkstücks, sondern beeinflusst auch nicht die Bearbeitungsgenauigkeit der Werkzeugmaschine, wodurch die Produktionskapazität der Werkstatt für die Bearbeitung großer Teile erheblich verbessert wird Formen.
Mit dem beweglichen Mehrachs-Bearbeitungskopf können große Formen mit besonders komplexen Strukturen bearbeitet werden. Der auf die variable Geometrie ausgelegte Bearbeitungskopf ermöglicht eine 3-Achs-Simultanbearbeitung. Mit nur einer Aufspannung des Werkstücks können tiefe Kavitäten gefräst und bearbeitet werden. Formen und Kühllöcher sowie das Schneiden vieler anderer Teile mit komplexen Geometrien. Beispielsweise kann bei optimaler Neigung der Spindel die Nähe des Bearbeitungskopfes zum Fräsbearbeitungspunkt vergrößert werden, so dass der mehrachsige Bearbeitungskopf zur Fertigstellung der Schräglochbearbeitung verwendet werden kann.
Da der Mehrachsen-Bearbeitungskopf die Oberfläche des Werkstücks bearbeitet, wird außerdem die Radiuskante des Werkzeugs anstelle der Werkzeugspitze verwendet, so dass die Oberflächenrauheit verbessert werden kann.
8. Chipmanagement
Beim Zerspanen von Metall wird eine große Menge an Spänen erzeugt. Wenn es nicht rechtzeitig beseitigt werden kann, führt es unweigerlich zum Nachschneiden und zur Erwärmung von Werkzeugmaschinenbauteilen oder Werkstückoberflächen. Unter dem Arbeitstisch eines großen Formenbearbeitungszentrums befinden sich in der Regel 18 Spanlöcher, egal wohin der Arbeitstisch bewegt wird, die Späne können zuverlässig abtransportiert werden. An der Werkzeugmaschine sind 4 klappbare Späneförderbänder eingebaut, die die Späne mit hoher Geschwindigkeit zur Vorderseite der Werkzeugmaschine transportieren.
9. Hochdruckkühlmittel
Bei der Bearbeitung großer Formen spielt Hochdruckkühlmittel eine sehr wichtige Rolle. Wenn beispielsweise das 2+3-Achsen-Bearbeitungsverfahren zum Bohren von geneigten Löchern verwendet wird, ist ein Kühlmittel mit einem Druck von 1000 psi (1 psi = 6890 Pa) erforderlich, um die Späne effektiv zu entfernen und eine höhere Präzision beim Schneiden zu erzielen. Steht kein solches Hochdruck-Kühlmittel zur Verfügung, müssen bei der Bearbeitung von Schrägbohrungen zusätzliche Werkzeugmaschinen hinzugefügt werden, eine Nachinstallation ist erforderlich, was die Bearbeitungsgenauigkeit verringert und die Zykluskosten erhöht. Aus der obigen Analyse ist ersichtlich, dass die einfache Bearbeitung von großen Formen mehr und bessere Funktionen der Werkzeugmaschine erfordert. Das neue von Makino entwickelte 2516-Achsen-Horizontal-Bearbeitungszentrum MCC3VG erreicht eine Spindeldrehzahl von 15000 U / min und verwendet die Methode "Wellenkernkühlung" und die Funktion "Lagerinnendruckschmierung", um sicherzustellen, dass die Spindel und die daran befestigten Lager rechtzeitig und effektiv gekühlt werden.
Darüber hinaus kann sich die Hauptwelle nicht nur entlang der horizontalen X-Achse, der vertikalen Y-Achse und der vorderen und hinteren Z-Achsenrichtung bewegen, sondern kann sich auch mit der A-Achse und der C-Achse drehen. Mit zwei Indexierungsfunktionen kann er nicht nur den Aufwand beim Einstellen reduzieren, sondern auch komplexe Werkstücke wie Stoßfänger, Instrumententafeln und Autoscheinwerfergläser schneiden.
Bitte bewahren Sie die Quelle und Adresse dieses Artikels für den Nachdruck auf:Grundkenntnisse der Druckgusswerkzeuge aus Aluminiumlegierungen
Mingh Druckgussunternehmen sind der Herstellung und Bereitstellung von hochwertigen und leistungsstarken Gussteilen gewidmet (das Angebot an Metalldruckgussteilen umfasst hauptsächlich) Dünnwandiger Druckguss,Heißkammerdruckguss,Kaltkammerdruckguss), Runder Service (Druckguss-Service,CNC-Bearbeitung,Formenbau,Oberflächenbehandlung). Alle kundenspezifischen Aluminium-Druckguss-, Magnesium- oder Zamak/Zink-Druckguss- und andere Gussanforderungen können uns gerne kontaktieren.
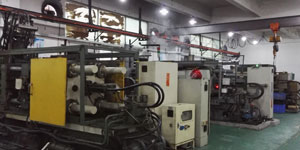
Unter der Kontrolle von ISO9001 und TS 16949 werden alle Prozesse durch Hunderte von fortschrittlichen Druckgussmaschinen, 5-Achsen-Maschinen und anderen Einrichtungen durchgeführt, von Blasgeräten bis hin zu Ultraschall-Waschmaschinen.Minghe verfügt nicht nur über fortschrittliche Ausrüstung, sondern auch über professionelle Team aus erfahrenen Ingenieuren, Bedienern und Inspektoren, um das Design des Kunden zu verwirklichen.
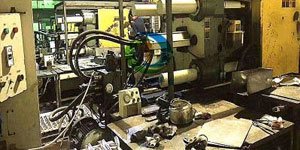
Auftragsfertigung von Druckgussteilen. Zu den Fähigkeiten gehören Kaltkammer-Aluminium-Druckgussteile von 0.15 lbs. bis 6 lbs., Schnellwechseleinrichtung und Bearbeitung. Mehrwertdienste umfassen Polieren, Vibrieren, Entgraten, Kugelstrahlen, Lackieren, Plattieren, Beschichten, Montage und Werkzeugbau. Zu den Materialien, mit denen gearbeitet wird, gehören Legierungen wie 360, 380, 383 und 413.
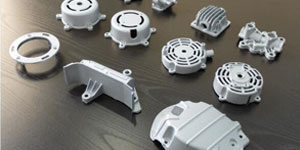
Unterstützung bei der Konstruktion von Zinkdruckguss / gleichzeitige Engineering-Dienstleistungen. Auftragsfertigung von Präzisions-Zink-Druckgussteilen. Es können Miniaturgussteile, Hochdruck-Kokillengussteile, Mehrschieber-Kokillengussteile, konventionelle Kokillengussteile, Einzel- und Einzeldruckgussteile sowie hohlraumdichte Gussteile hergestellt werden. Gussteile können in Längen und Breiten bis zu 24 Zoll in +/-0.0005 Zoll Toleranz hergestellt werden.
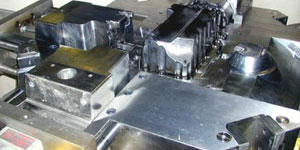
ISO 9001: 2015 zertifizierter Hersteller von Magnesium-Druckguss. Zu den Fähigkeiten gehören Hochdruck-Magnesium-Druckguss bis zu 200 Tonnen Heißkammer und 3000 Tonnen Kaltkammer, Werkzeugdesign, Polieren, Formen, Bearbeitung, Pulver- und Flüssiglackierung, vollständige Qualitätssicherung mit KMG-Fähigkeiten , Montage, Verpackung & Lieferung.
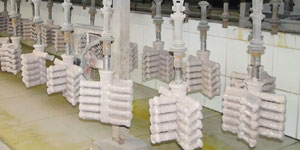
ITAF16949-zertifiziert. Zusätzlicher Casting-Service inklusive Feinguss,Sandguss,Schwerkraftguss, Verlorener Schaumguss,Schleuderguss,Vakuumgießen,Dauerguss,.Zu den Fähigkeiten gehören EDI, technische Unterstützung, Volumenmodellierung und Sekundärverarbeitung.
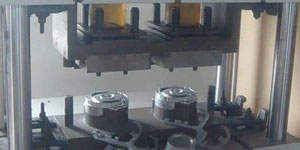
Gussindustrie Teile-Fallstudien für: Autos, Fahrräder, Flugzeuge, Musikinstrumente, Wasserfahrzeuge, optische Geräte, Sensoren, Modelle, elektronische Geräte, Gehäuse, Uhren, Maschinen, Motoren, Möbel, Schmuck, Vorrichtungen, Telekommunikation, Beleuchtung, medizinische Geräte, Fotogeräte, Roboter, Skulpturen, Tongeräte, Sportgeräte, Werkzeuge, Spielzeug und mehr.
Was können wir Ihnen als nächstes helfen?
∇ Zur Startseite gehen für Druckguss China
→Gussteile- Finden Sie heraus, was wir getan haben.
→Bewertete Tipps zu Druckgussdienste
By Minghe Druckgusshersteller |Kategorien: Hilfreiche Artikel |Werkstoff Stichworte: Aluminiumguss, Zinkguss, Magnesiumguss, Titanguss, Edelstahlguss, Messingguss,Bronzeguss,Casting-Video,Unternehmensgeschichte,Aluminiumdruckguss |Kommentare deaktiviert