Die Atmosphärenkontrolle während des Sinterprozesses von Sinterstahl und seine Leistung
Sinteratmosphäre und ihre Auswahl
Betrachtet man nur das Sintern von kohlenstoffhaltigem Stahl, so ist die in der pulvermetallurgischen Industrie verwendete Sinteratmosphäre Wasserstoff, Stickstoff, Stickstoff + Wasserstoff (Kohlenstoffpotential oder kein Kohlenstoffpotential), Zersetzung von Ammoniak, endothermes Gas, endothermes Gas + Stickstoff, Synthese Für Gas und Vakuum erfordert die richtige Auswahl der Sinteratmosphäre das Verständnis der Eigenschaften und Leistung verschiedener Sinteratmosphären und die Auswahl gemäß den Grundsätzen der Qualitätssicherung und Kostensenkung.
Wasserstoff ist eine stark reduzierende Atmosphäre. Viele Leute glauben, dass Wasserstoff eine gewisse Entkohlungswirkung hat, die jedoch hauptsächlich von der Reinheit des verwendeten Wasserstoffs und nicht vom Wasserstoff selbst abhängt. Im Allgemeinen enthält der Wasserstoff nach der Elektrolyse oder katalytischen Umwandlung eine gewisse Menge an Fremdgas, wie H2O, O2, CO und CH4 usw., manchmal kann die Gesamtmenge etwa 0.5% erreichen. Daher ist es am besten, es vor der Verwendung zu trocknen und zu reinigen, um seinen Sauerstoffgehalt und den Taupunkt zu senken. Reiner Wasserstoff wird jedoch aufgrund des hohen Preises von Wasserstoff selten als Sinteratmosphäre verwendet, es sei denn, es liegen besondere Gründe vor.
Stickstoff ist ein sicheres und billiges Inertgas, aber da reiner Stickstoff bei der Sintertemperatur nicht reduzierbar ist, wird reiner Stickstoff selten als Sinteratmosphäre bei der Herstellung von traditionellem pulvermetallurgischem Stahl verwendet. Da in den letzten Jahren die Kosten für die Stickstoffreinigung gesunken sind und sich die Luftdichtheit des Sinterofens verbessert hat, wurde auch damit begonnen, Stickstoff als Sinteratmosphäre zum Sintern von kohlenstoffhaltigem Stahl zu verwenden.
In den letzten Jahren wurde das Stickstoff-Wasserstoff-Gemisch zunehmend beim Sintern von Kohlenstoffstahl verwendet. Stickstoff/Wasserstoff wird normalerweise zwischen 95/5-50/50 verwendet. Diese Mischung hat einen gewissen Grad an Reduzierbarkeit und der Taupunkt kann unter -60 ° C erreichen. Im Allgemeinen muss eine bestimmte Menge CH4 oder C3H8 hinzugefügt werden, um ein bestimmtes Kohlenstoffpotential bei Verwendung dieses Gases bei 1050-1150 ° C während des Sinterns aufrechtzuerhalten Kohlenstoffstahl über 1250℃ braucht das Kohlenstoffpotential nicht zu kontrollieren. Mit dieser Mischung können chromhaltige Legierungen auf Eisenbasis unter 1120 °C ohne Oxidation gesintert werden.
Zersetzter Ammoniak wird durch Zersetzen von Ammoniakgas durch einen erhitzten Katalysator hergestellt, der 75 % H2 und 25 % N2 enthält. Aber im Allgemeinen verbleibt immer eine kleine Menge unzersetzter Ammoniakmoleküle im zersetzten Ammoniak. Wenn sie bei hohen Temperaturen mit heißem Metall in Kontakt kommen, zersetzen sie sich in hochaktive Wasserstoff- und Stickstoffatome, wodurch das Metall nitriert wird. Jüngste Studien haben gezeigt, dass das Sintern von AstaloyCrM bei 1120°C bei richtiger Kontrolle die 90N2/10H2-Mischung mit stärkerer Reduzierbarkeit zersetzt und ammonisiert. Der Hauptgrund ist, dass diese gerade beim Sinterprozess abgebauten aktiven Wasserstoffatome effektiver sind als 90N2/ Der Wasserstoff im 10H2-Mischgas ist stärker reduzierbar und kann die Oxidschicht außerhalb der AstaloyCrM-Partikel effektiv reduzieren. Um das Ammoniak zu reinigen und zu zersetzen, können Sie es durch Wasser leiten und trocknen, oder verwenden Sie aktiviertes Aluminiumoxid oder Molekularsieb, um das restliche Ammoniak zu entfernen.
Endothermes Gas ist eine Art Mischgas, das durch Mischen von Kohlenwasserstoffgas (CH4 oder C3H8) mit Luft in einem bestimmten Verhältnis, Vorwärmen auf 900-1000°C und katalytische Umwandlung durch einen Nickeloxidkatalysator erhalten wird. Je nach Verhältnis von Luft zu Kohlegas wird der Umwandlungsprozess von endothermen oder exothermen Reaktionen begleitet. Das resultierende Mischgas wird als endothermes Gas oder exothermes Gas bezeichnet und die Reaktion kann wie folgt ablaufen:
CmHn+m(O2+3.774N2)—mCO+n/H2+1.887mN2
Wenn die obige Reaktion vollständig durchgeführt werden soll, dh das gesamte C in CmHm hat gerade mit O2 in der Luft reagiert, sollte die erforderliche Luft/Gas m/2 (1+3.774) betragen, was 2.387 m entspricht. Wenn beispielsweise das verwendete Kohlenwasserstoffgas CH4 ist, sollte die erforderliche Luft/das erforderliche Gas 2.387 betragen, und das zu diesem Zeitpunkt erzeugte Mischgas enthält 40.9 % H2, 38.6 % N2 und 20.5 % CO. Nach der Reaktion enthält das Mischgas H2 Der CO- und CO-Gehalt nimmt mit der Zunahme von Luft/Gas ab, aber der Gehalt an H2O und CO2 nimmt zu. Es zeigt auch, dass das Kohlenstoffpotential im Mischgas nach der Reaktion mit der Zunahme von Luft/Gas abnimmt und die Oxidationsleistung zunimmt. Dies ist auch der Hauptgrund, warum beim Sintern von kohlenstoffhaltigem Stahl selten exothermes Gas verwendet wird und das meiste endotherme Gas verwendet wird.
Im Allgemeinen wird das durch Luft/Gas zwischen 2.0-3.0 erzeugte Mischgas als Absorptionsheißgas bezeichnet, und das Mischgas, das erzeugt wird, wenn das Verhältnis größer als 5.0 ist, wird als exothermes Gas bezeichnet. Das Verhältnis zwischen dem Taupunkt des mit CH4 als Rohstoff erzeugten endothermen Gases und Luft/Gas zeigt, dass Luft/Gas nur von 2.4 auf 2.5 und der Taupunkt des erzeugten Mischgases von -25°C auf . ansteigt über 0°C. Wenn Benutzer endothermes Gas selbst herstellen, sollten sie daher besonders darauf achten, das Verhältnis von Luft zu Gas in den Rohstoffen zu kontrollieren (vorzugsweise nicht mehr als 2.4), um endothermes Gas mit einem ausreichend niedrigen Taupunkt zu erhalten. Im Mischgas nach der Reaktion entspricht das Verhältnis der verschiedenen Gase dem Verhältnis am Ende der Reaktion, das im Allgemeinen (1000-1100°C) beträgt.
Wenn sich nach der Reaktion die Temperatur des Gases ändert, ändern sich das Kohlenstoffpotential des Mischgases, der Taupunkt und das Verhältnis der verschiedenen Gase. Viele Pulvermetallurgiehersteller verwenden einen exothermen Gasgenerator, um die erforderliche Sinteratmosphäre für mehrere Sinteröfen gleichzeitig durch die Pipeline zu liefern. Die Temperatur der Atmosphäre wurde vor dem Erreichen des Sinterofens gesenkt. . Ist die Isolierung der Pipeline nicht gut und die Temperatur der Pipelinewand niedriger als 800°C, dann lagert sich ein Teil des Kohlenstoffs im Mischgas in Form von Ruß an der Pipelinewand ab. Mit anderen Worten, wenn das Mischgas im Sinterofen wieder auf die Sintertemperatur erhitzt wird, ist seine Kohlenstoffwärme viel niedriger als das Kohlenstoffpotential, das der endotherme Gasgenerator bereitstellen kann.
In diesem Fall sollte dem Sinterofen eine angemessene Menge Methan oder Propan zugesetzt werden, um das Kohlenstoffpotential im Ofen sicherzustellen. Inzwischen haben einige ausländische Pulvermetallurgiehersteller damit begonnen, neben jedem Sinterofen einen kleinen endothermen Gasgenerator zu installieren und das soeben erzeugte endotherme Gas ohne Kühlung direkt in den Sinterofen zu verwenden, um eine Beeinträchtigung der Sinteratmosphäre durch Temperaturänderungen zu vermeiden . . Ein weiterer zu beachtender Punkt ist, dass selbst bei der katalytischen Wirkung des Nickeloxid-Katalysators eine geringe Menge an Kohlenwasserstoffgas (CH4 oder C3H8 usw.) in dem nach der Förderung erhaltenen Mischgas verbleibt. Außerdem entsteht zwischen den Gasen bei 900-1100℃ Nachdem die Reaktion ein Gleichgewicht erreicht hat, wird eine kleine Menge CO2 und H2O (gasförmig) produziert, die vor der Verwendung getrocknet werden müssen.
Die Zugabe von Stickstoff zum endothermen Gas kann den relativen Gehalt an CO, CO2 und H2O im endothermen Gas reduzieren, um die Empfindlichkeit der Atmosphäre gegenüber Kohlenstoffpotential und Taupunkt zu puffern und einige Korrelationskoeffizienten in der Sinteratmosphäre zu erleichtern kontrollieren.
Synthetisches Gas ist ein Verfahren, das in den letzten Jahren von ausländischen Sinterofenherstellern vorgeschlagen wurde, um (verdünntes) endothermes Gas direkt im Sinterofen zu erzeugen (ohne die Notwendigkeit eines endothermen Gasgenerators außerhalb des Ofens). Es mischt gasförmigen Methylalkohol und Stickstoff in einem bestimmten Verhältnis und leitet es dann direkt in den Sinterofen. In der Hochtemperatur-Sinterzone laufen folgende Reaktionen ab:
CH3OH-CO+2H2
Da das Verhältnis von CO und H2 im zersetzten Gas gleich dem Verhältnis des endothermen Gases ist, das durch das übliche Verfahren mit CH4 erzeugt wird, und der gemischte Stickstoff kombiniert werden kann, um eine gemischte Atmosphäre mit der gleichen Zusammensetzung wie das endotherme Gas (1L Das Methan entspricht 1.05 nm³ Stickstoff). Sein größter Vorteil besteht darin, dass kein endothermer Gasgenerator außerhalb des Ofens benötigt wird. Darüber hinaus können Benutzer unterschiedliche Mengen an Stickstoffgas mischen, um verdünntes endothermes Gas nach ihren eigenen Anforderungen zu produzieren.
Vakuum ist auch eine Art Sinteratmosphäre, die hauptsächlich zum Sintern von Edelstahl und anderen Materialien verwendet wird, jedoch nicht häufig zum Sintern von Kohlenstoffstahl.
Physikalische Eigenschaften der Sinteratmosphäre
Die meisten Veröffentlichungen und Berichte zur Sinteratmosphäre diskutieren hauptsächlich das chemische Verhalten zwischen verschiedenen Sinteratmosphären und dem Sinterkörper während des Sinterprozesses, diskutieren jedoch selten den Einfluss der physikalischen Eigenschaften verschiedener Atmosphären auf das Sintern, obwohl dieser Effekt in vielen Fällen nicht möglich ist ignoriert werden. Beispielsweise verursacht der Unterschied in der Gasviskosität den chemischen Konzentrationsgradienten des Sinterkörpers von der Oberfläche nach innen entlang der Öffnung, wodurch die Oberflächeneigenschaften des Sinterkörpers beeinflusst werden. Zum anderen haben die Wärmekapazität und die Wärmeleitfähigkeit verschiedener Gase einen großen Einfluss auf die Sinterzeit und Abkühlgeschwindigkeit. In diesem Abschnitt werden die wichtigsten physikalischen Eigenschaften einiger Sinteratmosphären bei unterschiedlichen Temperaturen (um die Sintertemperatur herum) zum Nachlesen aufgeführt.
Beispiele für atmosphärenbedingte Probleme beim Sintern
1 Beispiele für Rissbildung an der Oberfläche von Teilen beim Entwachsen
Wenn ein Siebband-Sinterofen verwendet wird und endothermes Gas als Sinteratmosphäre verwendet wird, kommt es zu Oberflächenrissen, wenn die Temperaturanstiegsgeschwindigkeit und die Atmosphäre in der Entparaffinierungszone nicht gut kontrolliert werden. Viele Leute denken, dass dieses Phänomen auf die schnelle Zersetzung des Schmiermittels zurückzuführen ist. Es wird verursacht, ist aber nicht der Fall. Der wahre Grund ist, dass das Kohlenmonoxid im endothermen Gas im Temperaturbereich von 450-700 ° C unter der Katalyse von Eisen, Nickel und anderen Metallen in festen Kohlenstoff und Kohlendioxid zersetzt wird. Es ist der neu abgeschiedene feste Kohlenstoff in den Poren des Sinterkörpers, der sein Volumen ausdehnt und das oben erwähnte Phänomen der Oberflächenrissbildung verursacht.
Die Qualität der Teile variiert mit der Temperatur während des Sinterprozesses in verschiedenen Atmosphären. Darunter ist Atmosphäre 3 trockenes endothermes Kohlegas, und Atmosphären 4 und 5 sind endothermes Kohlegas, dem unterschiedliche Mengen an Wasserdampf zugesetzt wurden. Es ist zu erkennen, dass während des Sinterprozesses die Qualität der Teile ab ca. 200°C nachlässt, der darin befindliche Festschmierstoff kontinuierlich abgebaut wird und den Sinterkörper überläuft und dessen Qualität mindert. Wenn das gemischte Pulver kein festes Schmiermittel enthält, existiert das obige Phänomen natürlich nicht. Wenn die obigen drei Atmosphären verwendet werden, ist dieses Phänomen umso schwerwiegender, je trockener die Atmosphäre von der Qualität des Sinterkörpers bei etwa 450°C ist.
Interessant ist jedoch, dass bei der Verwendung von Gas 3 (trockenes endothermes Gas) unabhängig von der Anwesenheit von Festschmierstoffen ein Oberflächencracken auftritt, was darauf hinweist, dass es nicht direkt mit dem Entparaffinieren zusammenhängt und kohlenstoffreiches Gas in den Rissen gefunden wird. Phänomen, wir können die Richtigkeit der obigen Erklärung bestätigen.
Es gibt mehrere Möglichkeiten, das Auftreten des oben erwähnten Rissbildungsphänomens zu vermeiden. Am direktesten ist es, die Sinteratmosphäre von endothermem Gas auf Wasserstoff-Stickstoff-Gemisch umzustellen, ohne unterbrochene Linien zu knacken. Wenn die Sinteratmosphäre nicht geändert werden kann, gibt es zwei Methoden. Eine besteht darin, einen Teil des endothermen Gases, das Wasserdampf enthält, in die Entparaffinierungszone des Sinterofens einzublasen. Bei diesem Verfahren ist es jedoch schwierig, im tatsächlichen Betrieb eine stabile Steuerung zu erhalten.
Die Luftstromsteuerung des Sinterofens ist nicht gut, und das Phänomen, dass eine Atmosphäre mit hohem Taupunkt in die Sinterzone eindringt, kann die Sinterqualität beeinträchtigen. Die zweite und beste Methode besteht darin, die Erwärmungsrate der Teile in der Entparaffinierungszone des Sinterofens zu erhöhen, damit sie so schnell wie möglich 450 überschreitet. Im Bereich der Rissbildung bei -600 °C wird üblicherweise das sogenannte Schnellentwachsen auf dieses Phänomen ausgelegt.
2 Sinterbeispiel AstaloyCrM
Metallchrom wird wegen seines niedrigen Preises und seiner guten Verstärkungswirkung häufig in legiertem Stahl verwendet. Chromhaltiger Sinterstahl wird jedoch bei seinem Herstellungsverfahren auf viele Probleme stoßen. Eine davon ist die Herstellung von chromhaltigem Eisenpulver, das einem strengen Zerstäubungs- und Glühreduktionsprozess unterzogen werden muss, um Rohmaterialpulver mit geringerem Sauerstoff- und Kohlenstoffgehalt zu erhalten. .
Honganas AB aus Schweden ist derzeit der einzige Hersteller weltweit, der dieses Rohstoffpulver kostengünstig herstellen kann. Die zweite ist, dass selbst wenn hochwertiges chromhaltiges Eisenpulver erhalten werden kann, wenn die Sinterung und die Mediumtemperatur, insbesondere die Sinteratmosphäre, nicht gut kontrolliert werden können, es während des Sinterns und der Oxidation wahrscheinlicher oxidiert wird, und die die Sinterleistung wird reduziert.
Thermodynamische Berechnungen und eine Vielzahl von Versuchen haben bewiesen, dass bei Verwendung des endothermen Gases als Sinteratmosphäre von AsaloyCrM die Sinteranforderungen selbst bei sehr niedrigem Taupunkt nicht erfüllt werden können.
Mit anderen Worten, zum Sintern von AsaloyCrM kann nur reiner Wasserstoff oder Wasserstoff-Stickstoff-Gemisch verwendet werden. Derzeit werden die meisten letzteren verwendet. , Der Anteil von Wasserstoff beträgt 5%-20%. Der Leser sollte daran erinnert werden, nicht nur die Zusammensetzung der Sinteratmosphäre sicherzustellen, sondern auch die Qualität der Sinteratmosphäre sicherzustellen.
Die sogenannte Qualität bezieht sich hier auf den Oxidationsgrad in der Sinteratmosphäre, der im Allgemeinen durch den Sauerstoffpartialdruck in der Atmosphäre kalibriert wird. Wenn beim Sintern bei 1120 °C der Sauerstoffpartialdruck in der Atmosphäre niedriger als 1 × 10 – 14 Pa ist, tritt während des Sinterprozesses keine Oxidation auf.
Wenn die Temperatur gesenkt wird, muss der Sauerstoffpartialdruck in der Atmosphäre, um eine Oxidation zu verhindern, sogar niedrig sein. Die obige Berechnung wurde durch experimentelle Daten bestätigt.
Bitte bewahren Sie die Quelle und Adresse dieses Artikels für den Nachdruck auf: Die Atmosphärenkontrolle während des Sinterprozesses von Sinterstahl und seine Leistung
Mingh Druckgussunternehmen sind der Herstellung und Bereitstellung von hochwertigen und leistungsstarken Gussteilen gewidmet (das Angebot an Metalldruckgussteilen umfasst hauptsächlich) Dünnwandiger Druckguss,Heißkammerdruckguss,Kaltkammerdruckguss), Runder Service (Druckguss-Service,CNC-Bearbeitung,Formenbau,Oberflächenbehandlung). Alle kundenspezifischen Aluminium-Druckguss-, Magnesium- oder Zamak/Zink-Druckguss- und andere Gussanforderungen können uns gerne kontaktieren.
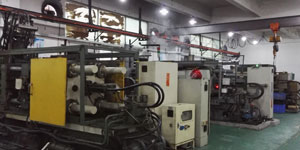
Unter der Kontrolle von ISO9001 und TS 16949 werden alle Prozesse durch Hunderte von fortschrittlichen Druckgussmaschinen, 5-Achsen-Maschinen und anderen Einrichtungen durchgeführt, von Blasgeräten bis hin zu Ultraschall-Waschmaschinen.Minghe verfügt nicht nur über fortschrittliche Ausrüstung, sondern auch über professionelle Team aus erfahrenen Ingenieuren, Bedienern und Inspektoren, um das Design des Kunden zu verwirklichen.
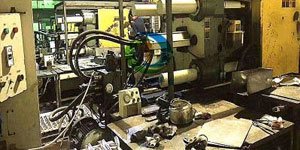
Auftragsfertigung von Druckgussteilen. Zu den Fähigkeiten gehören Kaltkammer-Aluminium-Druckgussteile von 0.15 lbs. bis 6 lbs., Schnellwechseleinrichtung und Bearbeitung. Mehrwertdienste umfassen Polieren, Vibrieren, Entgraten, Kugelstrahlen, Lackieren, Plattieren, Beschichten, Montage und Werkzeugbau. Zu den Materialien, mit denen gearbeitet wird, gehören Legierungen wie 360, 380, 383 und 413.
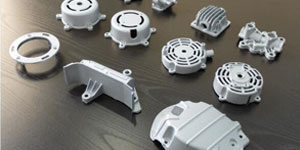
Unterstützung bei der Konstruktion von Zinkdruckguss / gleichzeitige Engineering-Dienstleistungen. Auftragsfertigung von Präzisions-Zink-Druckgussteilen. Es können Miniaturgussteile, Hochdruck-Kokillengussteile, Mehrschieber-Kokillengussteile, konventionelle Kokillengussteile, Einzel- und Einzeldruckgussteile sowie hohlraumdichte Gussteile hergestellt werden. Gussteile können in Längen und Breiten bis zu 24 Zoll in +/-0.0005 Zoll Toleranz hergestellt werden.
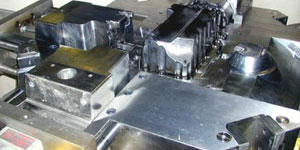
ISO 9001: 2015 zertifizierter Hersteller von Magnesium-Druckguss. Zu den Fähigkeiten gehören Hochdruck-Magnesium-Druckguss bis zu 200 Tonnen Heißkammer und 3000 Tonnen Kaltkammer, Werkzeugdesign, Polieren, Formen, Bearbeitung, Pulver- und Flüssiglackierung, vollständige Qualitätssicherung mit KMG-Fähigkeiten , Montage, Verpackung & Lieferung.
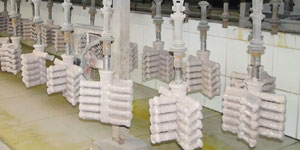
ITAF16949-zertifiziert. Zusätzlicher Casting-Service inklusive Feinguss,Sandguss,Schwerkraftguss, Verlorener Schaumguss,Schleuderguss,Vakuumgießen,Dauerguss,.Zu den Fähigkeiten gehören EDI, technische Unterstützung, Volumenmodellierung und Sekundärverarbeitung.
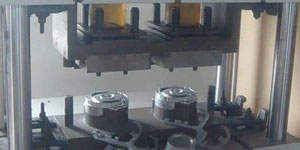
Gussindustrie Teile-Fallstudien für: Autos, Fahrräder, Flugzeuge, Musikinstrumente, Wasserfahrzeuge, optische Geräte, Sensoren, Modelle, elektronische Geräte, Gehäuse, Uhren, Maschinen, Motoren, Möbel, Schmuck, Vorrichtungen, Telekommunikation, Beleuchtung, medizinische Geräte, Fotogeräte, Roboter, Skulpturen, Tongeräte, Sportgeräte, Werkzeuge, Spielzeug und mehr.
Was können wir Ihnen als nächstes helfen?
∇ Zur Startseite gehen für Druckguss China
→Gussteile- Finden Sie heraus, was wir getan haben.
→Bewertete Tipps zu Druckgussdienste
By Minghe Druckgusshersteller |Kategorien: Hilfreiche Artikel |Werkstoff Stichworte: Aluminiumguss, Zinkguss, Magnesiumguss, Titanguss, Edelstahlguss, Messingguss,Bronzeguss,Casting-Video,Unternehmensgeschichte,Aluminiumdruckguss |Kommentare deaktiviert